Factors Affecting Ball Mill Grinding Efficiency
For example, Turner (1979) has demonstrated an overall increase in capacity of almost 800 percent by ball addition to an ore of …
اقرأ أكثر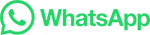
How to Improve Cement Ball Mill Performance
The equation below shows the relationship between ball mill grinding efficiency and material fineness: Kd = G2/G1 = (d1/d2) X (1) *Note. Kd: the relative productivity of the mill; G1 & G2: respectively represent the mill output (T / h) when the feed particle size is d1 and d2; X: the index, which is related to material characteristics, product ...
اقرأ أكثر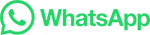
Temperature Reduction for Ball Mill Optimization …
Heat taken away by ventilation systems can accounts for roughly 20% of the total heat discharged by the ball mill. Improving that ventilation system brings more cool air into the inside of the ball bill, gradually reducing the …
اقرأ أكثر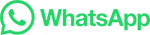
Ball Mills
Ball Mills. In all ore dressing and milling Operations, including flotation, cyanidation, gravity concentration, and amalgamation, the Working Principle is to crush and grind, often with rod mill or ball mill, the ore in order to liberate the minerals. In the chemical and process industries, grinding is an important step in preparing raw ...
اقرأ أكثر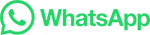
Comparison of energy efficiency between ball mills and stirred mills …
At product sizes finer than 80% passing 75 μm, the efficiency of ball mill grinding rapidly decreases. The practical limit to ball mill product fineness is considered to be 40–45 μm (Gao and Weller, 1994). Although ball mills can still be found in the regrind circuits in a number of mineral processing plants, their energy consumption is ...
اقرأ أكثر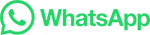
Energies | Free Full-Text | Increasing Energy Efficiency and
To increase efficiency, designers of mining equipment tried to improve all the elements of ball mills, such as the geared mechanical drives, bearings, their lubrication systems, and electric motors. Moreover, efforts have been made to optimize the size of the grinding bodies, control the filling level of the drum with the material, and ...
اقرأ أكثر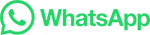
BALL MILLS Ball mill optimisation
Ball mill optimisation As grinding accounts for a sizeable share in a cement plant's power consumption, optimisation of grinding equipment such as ball mills can provide …
اقرأ أكثر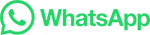
Factors Affect The Output and Quality of Ball Mills And How …
From the perspective of production technology, the influencing factors are mainly the following 10 points: 1. Particle size of grinding materials. The grinding materials' particle size affects the ball mill's output and quality. If the particle size is small, the production and quality of the mill will be high, and the power consumption ...
اقرأ أكثر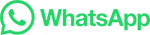
Impact energy of particles in ball mills based on DEM simulations …
Ball mill is one of the most commonly used mills for the crushing and grinding of mineral ore. It is generally used to grind material down to the particle size of 20 to 75 μm and can vary in size from a small batch mill up to a mill with outputs of hundreds of tonnes per hour. ... Any slight improvement in grinding efficiency will be of ...
اقرأ أكثر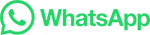
(PDF) Improving the efficiency of the coal grinding process in ball …
Curves of mill productivity, power consumed, specific surface of coal dust in terms of the relative rotational speed of the ball drum mill Composition of the balls loading the mill with a standard ...
اقرأ أكثر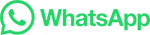
Diameter factors affecting ball mill scale-up
96 V2 (D2)2 V1 - (D1)2 (3) As mill diameters increase, the power drawn by ball mills increases by the mill diameters to at least the 2.3 power (Bond, 1960 ). Not allowing for any gain in efficiency, the potential increase in mill capacity is the same as mill power. Increases in grinding efficiency with increasing ball mill diameters makes …
اقرأ أكثر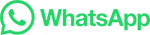
What Factors Will Influence Ball Mill Grinding Efficiency?
Ball mill grinding efficiency is influenced by many factors: ore grindability, feed size, grinding product size, ball mill diameter and length, ... If the length of the ball mill is too long, it will increase energy consumption and cause over-grinding of the material. If the length is too short, it may not complete the specified particle size ...
اقرأ أكثر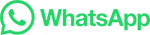
Moisture Removing & Increasing Efficiency in "Ball Mill" …
1) To remove moisture from ball mill. 2) Increase efficiency of ball mill. It is an industrial research which is held in MATRUKRUPA CALCINE INDUSTRY GUJARAT. II. COMPANY PROFILE A. Company Production: Tiles surface finishing powder Raw material for refectories cement Calcine bauxite B. Row Material: Raw bauxite
اقرأ أكثر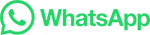
How Ball Mill Ore Feed Size Affects Tonnage & Capacity
Hard ore Work Index 16 = 100,000/65,000 = 1.54 kwh/t. For the purposes of this example, we will hypothesize that the the crushing index of the hard ore with the increased energy input of 1.54 kw/t reduces the ball mill feed size to 6,500 micrometers. As a result, the mill output will increase with this reduced size to approximately 77,000 tons ...
اقرأ أكثر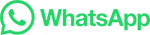
Addition of pebbles to a ball-mill to improve grinding efficiency …
The implication of this data is that a build-up of scats in the ball-mills will cause the circulating load to increase in a closed ball-mill circuit, despite the presence of trommels. Table 3.2.2 . Effect of scats particles on ball-milling - Particle size distributions (4 kg of 19/13.2 mm scats added in the feed for the tests of ball-milling ...
اقرأ أكثر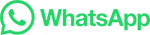
Ten Ways to Improve the Grinding Efficiency of …
Moreover,the efficiency of crushing is obviously higher than that of grinding, and the energy consumption of crushing is low, which is about 12%~25% of the grinding. 3. Reasonable filling rate of ...
اقرأ أكثر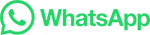
How to Improve Ball Mill Performance
Ball Mill Breakage Efficiency. Consider a ball mill circuit processing material of a given feed size and at a given throughput rate to …
اقرأ أكثر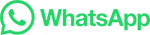
Effect of ball size and powder loading on the milling efficiency …
The effect of ball size on the particle size reduction has been investigated first for varying rotation speed of the container. Percent passing and size distributions of the milled Al 2 O 3 powder are shown in Fig. 1, Fig. 2, respectively, as a function of particle size for varying ball size.The average particle sizes (d 50) of the milled Al 2 O 3 powder are …
اقرأ أكثر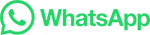
How to improve working efficiency of ball mill
Increasing the effective volume of the ball mill can increase the efficiency of the mill production. Ordinary alloy linings are thick and heavy, which reduces the effective volume of the mill and increases the power consumption, which reduces the production efficiency of the ball mill. Therefore, the material of the lining is very important.
اقرأ أكثر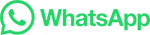
How to Improve Working Efficiency of Energy-Saving Grid Ball Mills …
Factors Affecting Ball Mill Efficiency. 1. Physical properties of ore. The physical properties such as hardness, particle size, and mud content of the ore have a significant impact on the ...
اقرأ أكثر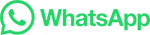
Cement Separator & Ball Mill Optimization
4. Sampling inside mill (mill test) Sampling of material. – Take ~1 kg sample every 1 m along mill axis. – Each sample collected from 3 point in the same cross section. – Removed some balls and taken sample. -First …
اقرأ أكثر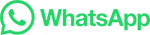
Improvement of methods to ensure energy efficiency of …
Ball mills are used for the stage of grinding ore in mining operations with the alignment of grinding balls. Controlling the operating conditions of ball mills is a key factor for optimal mill operation and high mill productivity. The main factors affecting the efficiency of a ball mill are ball loading, drum rotation, lining wear.
اقرأ أكثر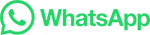
Seven Tips Increasing Ball Mill Grinding …
4.Reasonably add steel balls. During the long period of operation, the ore grinding will lead to the wear of steel ball. It leads to the ratio change of different size steel balls. It changes the ...
اقرأ أكثر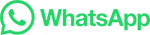
(PDF) Grinding Media in Ball Mills-A Review
are currently being mined, which has forced many mines to upgrade the size of their mills, to increase the mill through- put. Larger mills have a low energy efficiency, hence costly to operate [5].
اقرأ أكثر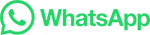
(PDF) INVESTIGATION OF EFFECTS OF GRINDING MEDIA …
Worn balls Worn balls perform more poorly than spheres, reduce the grinding chamber in the mill, and increase power consumption. [9] Spherical balls are mostly used for ball mill processes but are ...
اقرأ أكثر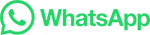
Key Factors for Ball Mill Optimization in the Mining Industry
You can optimize the grinding efficiency of your ball mill by optimizing factors such as mill design and operating conditions, grinding media size, shape, quantity, and feed …
اقرأ أكثر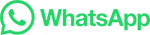
U.S. Department of Energy Office of Energy Efficiency …
can greatly increase the energy efficiency • Reduces ball consumption by of grinding mills. Besides mill optimization, the impact 20% due to its ability to optimize spectra obtained could be used in three ball to rock ratio. additional ways. First, the signature data The grinding efficiency of semi - • Improves equipment life and
اقرأ أكثر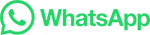
(PDF) Analysis of the efficiency of the grinding process in …
Abstract. Ball mills for fine grinding cement clinker and additives are widely used around the world. To improve the efficiency of a ball grinding the ball mills are transferred in closed circuit ...
اقرأ أكثر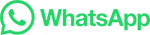
Rationed Ball Mill Charging to Improve …
The most dramatic advantage of rationed charging of martensitic alloy steel balls as compared to use of 76 mm pearlitic carbon steel balls has been a 16.6% to 25.0% reduction in grinding ball …
اقرأ أكثر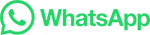
Improvement of the structure of a ball mill with the purpose …
That is why this work is aimed at choosing a way to improve the design of the ball mill in order to increase the efficiency of grinding material. This will provide a better process of grinding the ...
اقرأ أكثر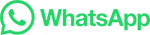