(PDF) Effects of Ball Size Distribution and Mill Speed and …
For this purpose, batch ball mill experiments were conducted with three narrow-size fractions (−3.35 + 2.36 mm, −1.70 + 1.18 mm, and −0.85 + 0.60 mm) of the feed and product samples of an ...
اقرأ أكثر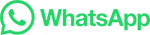
Combined DEM and SPH simulation of overflow ball mill …
Numerical modelling (such as by Discrete Element Modelling (DEM) and Smoothed Particle Hydrodynamics (SPH) methods) of solids/fluid flow inside mills and …
اقرأ أكثر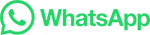
Combined DEM and SPH simulation of overflow ball mill …
Screening efficiency for a trommel depends on the residence time of material based on the length and inclination of the screen and the flow inside the trommel. ... The model includes the last 1.5 m axial length of the end section of a 6 m diameter overflow ball mill with a trommel screen attached for collecting the mill discharge as shown in ...
اقرأ أكثر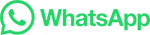
Ball Mill Design/Power Calculation
The basic parameters used in ball mill design (power calculations), rod mill or any tumbling mill sizing are; material to be ground, characteristics, Bond Work Index, bulk density, specific density, desired mill tonnage capacity DTPH, operating % solids or pulp density, feed size as F80 and maximum 'chunk size', product size as P80 and maximum …
اقرأ أكثر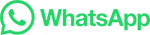
Energies | Free Full-Text | Energy-Efficient Advanced …
When used as a medium, the detritor mill utilises a screen size of 300 mm to preserve sand . presently produces them in ... Musa, F. Comparison of energy efficiency between ball mills and stirred mills in coarse grinding. Miner. Eng. 2009, 22, 673–680. [Google Scholar] Shi, F.; Lambert, S.; Daniel, M. A study of the effects of …
اقرأ أكثر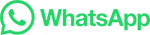
Ball Mill
where d b.max is the maximum size of feed (mm); σ is compression strength (MPa); E is modulus of elasticity (MPa); ρb is density of material of balls (kg/m 3); D is inner diameter of the mill body (m).. Generally, a maximum allowed ball size is situated in the range from D /18 to D/24.. The degree of filling the mill with balls also influences productivity of the …
اقرأ أكثر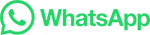
Closed circuit ball mill – Basics revisited | Request PDF
One of these, "Circuit Classification System Efficiency" (CSE), is the fraction of "coarse" material inside the ball mill upon which grinding energy is deliberately expended, versus the remaining ...
اقرأ أكثر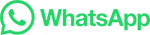
Grinding efficiency of ball mill calculating equation
Grinding efficiency of ball mill can be calculated using the following equation: Efficiency = (ground volume / waste produced) x . Ball mills are primary grinding devices in the production of fine powders and coffee. A ball mill is a cylindrical device with a series of balls (or, more recently, disks) that are mounted on an axle and rotated ...
اقرأ أكثر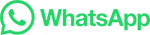
Closed circuit ball mill – Basics revisited
Highlights Circulating load and classification efficiency effect on ball mill capacity revisited. Relative capacity model introduced and validated. Relationship between circulating load and classification efficiency verified by industrial data. Existing fine screening technology could increase ball mill circuit capacity 15–25%.
اقرأ أكثر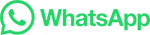
Determining the Bond Efficiency of industrial grinding …
1. Conduct screen analyses of the circuit feed and product samples. 2. Conduct Wi test(s) on the circuit feed (see Section 8).. Use a 1,190 µm screen to close the rod mill Wi test …
اقرأ أكثر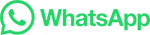
Ball Charge and Grinding Efficiency
What are the dimensions of the ball mill you are looking at? 40% ball charge is quite high (unless you are looking at a small mill). A difference (duty vs. maximum) of 5% to 10% is fairly typical and you would likely struggle to perceive an energy efficiency difference between the two operating points.
اقرأ أكثر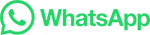
Closed circuit ball mill – Basics revisited
This efficiency was chosen as an industrial practice "average" from the data presented in Fig. 6. The relative capacity of a closed ball mill circuit as function of circulating load was calculated for three different classification arrangements: 1. cyclones with 38% of fine material reporting (by-pass) to coarse product (cyclone underflow), 2.
اقرأ أكثر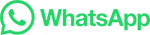
Screening Efficiency
Case studies on the use of chip thickness screening (CTS) for improving pulp mill operations, reducing costs, improving productivity, yield, and overall operational …
اقرأ أكثر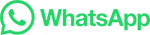
mill/sbm efficient ball mill vibrating screen power …
Contribute to crush2022/mill development by creating an account on GitHub.
اقرأ أكثر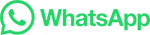
Vibrating screen working principle & screening efficiency
Screening is the process of separating a mixture of different particle sizes of materials into several different particle size levels by means of a single or multi-layer screen. The screening process of loose materials consists of two stages. 1. The particles that can easily pass through the holes of the screen reach the screen surface through ...
اقرأ أكثر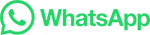
Intro to Size Reduction
Full Circle Screen Hammer Mills This next group also features the same grinding mechanism as the first two, and the same thin hammers as the pneumatic hammer mills. The amount of screen coverage is what sets them apart. The nearly 300 degree coverage of the rotor translates to a greater surface area for the processed material to
اقرأ أكثر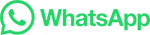
Ball Mill (Ball Mills Explained)
Crushed ore is fed to the ball mill through the inlet; a scoop (small screw conveyor) ensures the feed is constant. For both wet and dry ball mills, the ball mill is charged to approximately 33% with balls (range 30-45%). Pulp (crushed ore and water) fills another 15% of the drum's volume so that the total volume of the drum is 50% charged.
اقرأ أكثر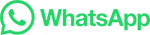
Ball Mill
Ball mill mode with diameter reach 6000 mm. Easy operate and maintenance. Equipped with feeding trolley, slow drive, hydraulic jack systmer, relining manipulator, bolts hammmer, hydrulic wrench for ensure easily operation and maintenance. Automation control system. PLC system with touch screen display to realize the automation control.
اقرأ أكثر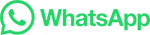
Keys to best practice comminution
If it is too coarse for efficient ball mill grinding, the problem can go undetected for many months. If the mills are tightly sized this could be the difference between making production targets or failing to do so. ... 5 mm Screen: Ball: 20: 29.4: 13.0: 6.0: 75: Good Choice: 7: SAG: 28: 12.7: 11.0: 5.6: 12.1: 3400: 10 mm Screen: Ball: 20: 31.6:
اقرأ أكثر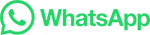
CHAPTER 3 Size Reduction and Size Separation
rotated at the critical speed of ball mill. The optimum size reduction in a ball mill depends o the following factors: Feed quantity: Too much feed will produce cushioning effect and too little feed will produce loss of efficiency of the mill. Speed of rotation of the cylinder: At low speed the mass of balls will
اقرأ أكثر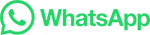
THE BENEFITS OF HIGH CLASSIFICATION EFFICIENCY IN CLOSED BALL MILL …
Keywords: Ball Mill, Energy, Efficiency, Screens, Flotation, ... used 100μm screen, of raw materials are given below.CircuitBond work index (kWh/t)Specific energy consumption (kWh/t)HPGR-ball ...
اقرأ أكثر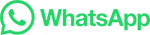
Energy Efficient Ball Mill Circuit – Equipment Sizing …
SIZING BALL MILL IN CLOSE CIRCUIT WITH SCREEN ... E classification efficiency (fraction) For a standard ball mill circuit the circulating load is usually 250%, as established by Bond (1962).
اقرأ أكثر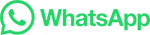
Solved 1. One tone per hour of dolomite is produced by a
Question: 1. One tone per hour of dolomite is produced by a ball mill operating in closed circuit grinding with a 100 mesh screen. The screen analysis (weight %) is given below. Calculate the screen efficiency
اقرأ أكثر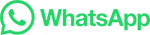
e clAssificAtion efficiency on hpgr And BAll mill circuit
classification efficiency has a major effect on the efficiency of closed circuit ball mills. ... high screen panel consumption and low capacity. These developments are discussed by ...
اقرأ أكثر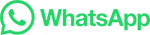
LIME SLAKING 101
Ball Mill Vertical Ball Mill Mixtank / Batch Slaker Max Size Slaker Control Grit Handling Ability to be Optimized Physical Size Lo w 26,000 kg/hr Temperature Screen / Screw High Moderate Moderate 3,600 kg/hr Torque Screen / Screw Low Small High 50,000 kg/hr Hydrocyclone Moderate Very Lar ge Temperature (delayed) 50,000 kg/hr …
اقرأ أكثر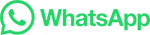
Closed Circuit Grinding VS Open Circuit Grinding
Closed Circuit Grinding VS Open Circuit Grinding. The simplest grinding circuit consists of a ball or rod mill in closed circuit with a classifier; the flow sheet is shown in Fig. 25 and the actual layout in Fig. 9. This single-stage circuit is chiefly employed for coarse grinding when a product finer than 65 mesh is not required, but it can be ...
اقرأ أكثر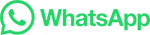
Factors Affecting Ball Mill Grinding Efficiency
Factors Affecting Ball Mill Grinding Efficiency. The following are factors that have been investigated and applied in conventional ball milling in order to maximize …
اقرأ أكثر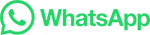
Investigating the benefits of replacing hydrocyclones with …
The ball mills are different in design. Therefore, simulation studies were carried out to eliminate the differences in factors affecting the performance of the circuits …
اقرأ أكثر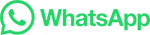
A Bond Work index mill ball charge and closing screen …
An alternative mill ball charge is proposed that closely approximates Bond's original total ball mass, number of balls and ball surface area. Results of 30 Bond Work index tests of six pure materials (calcite, magnesite, labradorite (feldspar), quartz, andalusite and glass) using closing screen apertures (P 1 ) values of 500, 250, 125, 90 and ...
اقرأ أكثر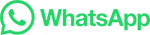
Ball Mill Discharge Spiral and Trommel Screen
Ball Mill Discharge Spiral Screen. The Ball Mill Discharge Spiral Screen is designed to make a sized product, particularly for "Sub-A" Unit Flotation Cells and concentrating tables. It is also used to screen out and return to the ball mill any oversize in a ball mill-classifier circuit when using a (Selective) Mineral Jig. This Ball Mill ...
اقرأ أكثر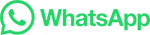