Pharmaceutical nanocrystals: production by wet milling …
Wet milling using planetary ball mills has been successfully used to produce nanosuspensions for drugs such as indometacin and brinzolamide 45, 58. Based on the principle of planetary ball milling, Juhnke et al. [59] developed a screening media mill equipped with up to 24 milling beakers of 0.05–1.0-ml individual milling chamber volumes.
اقرأ أكثر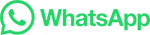
(PDF) Controlling the Ground Particle Size and Ball Mill Load …
The proposed method has been practically implemented on the ball mill of the Lakan lead-zinc processing plant. Also, a prototype of the device was built. The test results show that the optimal ...
اقرأ أكثر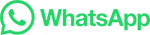
Wet ball milling of niobium by using ethanol, determination …
Abstract. This study investigates the effect of using ethanol as the process control agent during the wet ball milling of niobium (Nb). Dried nanocrystal Nb powders, …
اقرأ أكثر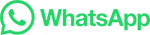
The effectiveness of wet milling materials in ball mills
Inthis study, forexplaining the ffectiveness of wet milling, wehave calculated the kinetic energy of the impact of a ball during the"cascade" condition ofoperating aball mill bythe …
اقرأ أكثر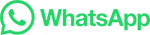
The Advantages of Wet Mill Micronization in Pharmaceutical
Wet-milling is a method of reducing the particle size of an API in suspension. It can readily achieve particle sizes (10-15 microns of mean volume) near to those of jet-mill micronization – without many of the disadvantages. Some of the advantages of wet-milling are: Protects Temperature Sensitive Compounds. Wet …
اقرأ أكثر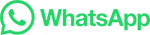
Wet Pan Mill | Ore Grinding Equipment
Wet Pan Mill. 【Capacity】0.5-3 TPH. 【Feeding Size】 <30mm. 【Discharge Size】 0.074-0.6mm. 【Procesible Material】 Gold, iron, molybdenum, lead, zinc, antimony, etc. 【Advantages】Pan Mill is now …
اقرأ أكثر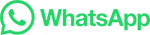
Inventory Of Common Faults And Solutions Of Mining Ball Mill
Fault 2: Mining ball mill reducer bearing heats up. Reason: One of the possible reasons for the ball mill reducer bearing heating is insufficient lubrication. Insufficient lubrication can cause bearings to operate at high temperatures, resulting in overheating. Another cause could be excessive load or improper installation.
اقرأ أكثر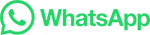
17 Signs of Problems with Ball Mills: Quickly …
High temperature of the ball mill will affact the efficiency 3 For every 1% increase in moisture, the output of the ball mill will be reduced by 8% -10%. 4 when the moisture is greater than 5%, the ball …
اقرأ أكثر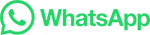
Ball Mill
Mechanical Crushing and Grinding. Oleg D. Neikov, in Handbook of Non-Ferrous Metal Powders, 2009 Tumbling Ball Mills. Tumbling ball mills or ball mills are most widely used in both wet and dry systems, in batch and continuous operations, and on a small and large scale.. Grinding elements in ball mills travel at different velocities. Therefore, collision …
اقرأ أكثر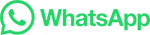
Modern Wet Milling and Material Processing
The traditional high-speed dissolver, ball mill, vertical mill and standard horizontal mill have been the primary methods used to …
اقرأ أكثر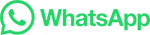
Ball Mills, Pebble Mills, Material Processing Mills | Hatboro …
Ball Mills, Pebble Mills, Material Processing Mills: For more than a century, Patterson has been the industry leading manufacturer of wet and dry grinding mills for size reduction or dispersal. Patterson's ball, pebble and rod mills are built to last. We are still filling parts requests for mills sold over 60 years ago. Patterson mills are available in a wide variety …
اقرأ أكثر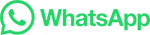
wet dry milling zinc oxide
Process for dry milling zinc powder to produce zinc flake – US …. The milling technique may be wet or dry. … of a surfactant and a metal oxide. … particles which comprises drymilling technique may be wet or dry. … of a surfactant and a metal oxide. … particles which comprises dry
اقرأ أكثر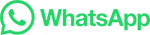
Modeling of Bauxite Ore Wet Milling for the Improvement …
Size reduction is a necessary operation in mineral processing plants and provides the desired size for separation operations and the liberation of the valuable minerals present in ores. Estimations on energy consumption indicate that milling consumes more than 50 % of the total energy used in mining operations. Despite the …
اقرأ أكثر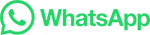
How to Get the Most Out of the Wet Milling Process
Wet milling, also known as wet grinding, involves the use of mechanical energy to break down materials by suspending particles in a liquid slurry and then dispersing those particles through shearing or …
اقرأ أكثر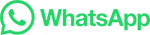
Effect of ball size and powder loading on the milling efficiency …
The effect of ball size on the particle size reduction has been investigated first for varying rotation speed of the container. Percent passing and size distributions of the milled Al 2 O 3 powder are shown in Fig. 1, Fig. 2, respectively, as a function of particle size for varying ball size.The average particle sizes (d 50) of the milled Al 2 O 3 powder are …
اقرأ أكثر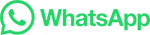
Ball mill-induced piezocatalysis assessment for dye …
The utilisation of piezocatalysis in the operation of a ball mill for the assessment of 0.6 g BiVO 4, utilising 15 yttria-stabilized zirconia balls, has resulted in a remarkable degradation constant (k) value of 0.0476 min −1. The scavenger test results indicate that the ball mill-assisted piezocatalysis mechanism for dye degradation is ...
اقرأ أكثر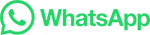
Ball Mill Loading
Abbe Jars are available in a wide range of sizes and materials. Milling jars are small scale version of the ball mills and are typically used in the laboratory or small scale producti. More. Talk with the Experts at Paul O. …
اقرأ أكثر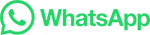
sbm/sbm mining and wet ball mill process for zinc.md at …
Contribute to sili2023/sbm development by creating an account on GitHub.
اقرأ أكثر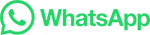
Everything You Need to Know About Wet Media …
Step 1: Wetting. The first step to wet grinding is eliminating air from the surface of the raw feed, so that each individual particle is fully in contact with the liquid slurry. Ensuring complete contact is vital for effective …
اقرأ أكثر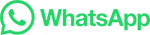
Ball Mill Is Indispensable For Lithium Ore Processing
The advantage of the grid type ball mill is that the ore discharge speed is fast, it can reduce the over-crushing of ore, and at the same time it can increase the output per unit volume. 1. Large row of ore …
اقرأ أكثر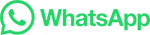
Wet Milling vs. Dry Milling in the Pharmaceutical Industry
Milling is used across a number of different industries and can be broadly divided into two types: wet milling and dry milling. When it comes to the manufacturing of pharmaceuticals, the particle size of ingredients is critical to a drug's performance and efficacy, so the stakes are much higher than when milling foods or other consumer …
اقرأ أكثر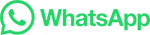
Ball milling as an important pretreatment technique in
The operation of a planetary ball mill under wet or dry state is another decisive factor that must be considered to make the grinding process successful. Pretreatment of lignocellulosic biomass in the wet or dry state produces different results. ... Wet ball milling and wet disk milling mainly resulted in defibrillation and reduction of …
اقرأ أكثر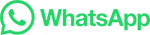
sbm/sbm zinc processing methods wet grid ball mill.md at …
Contribute to sili2023/sbm development by creating an account on GitHub.
اقرأ أكثر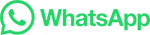
Planetary Ball Mill PM 100
The Planetary Ball Mill PM 100 is a powerful benchtop model with a single grinding station and an easy-to-use counterweight which compensates masses up to 8 kg. It allows for grinding up to 220 ml sample material …
اقرأ أكثر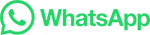
Working Volume in High-Energy Ball-Milling Process on
The purpose of this study was to investigate the effect of working volume in the high-energy ball-milling process on the breakage characteristics (i.e., particle size, morphology, and chemical composition) and adsorption performance of rice straw ash. This study was conducted to confirm working volume issue since this parameter has …
اقرأ أكثر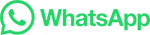
Ball Grinding Process | SpringerLink
Ball grinding can be carried out in either dry-operation or wet-operation. The former is widely used in coal-fired power plants and cement industry, and the latter is …
اقرأ أكثر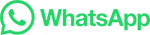
Ball milling: a green technology for the preparation and
The ball mill Ball milling is a mechanical technique widely used to grind ... groups depending on their operation mode: direct and indirect milling. In the rst case rollers or mechanical sha s directly act ... for 4–8 hours in dry and wet conditions with three solvents (water, toluene, 1-butanol). They observed that the different
اقرأ أكثر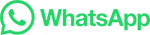
Impact of ball filling rate and stirrer tip speed on milling …
In terms of mill operation, it was also found that a higher stirrer tip speed and ball filling rate promoted particle size reduction. ... Stirred mill technology for regrinding McArthur River and Mount Isa zinc/lead ores. Proc. XX IMPC––Aachen. (1997), pp. 21-26. ... Grinding kinetics of quartz and chlorite in wet ball milling. Powder ...
اقرأ أكثر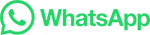
A Review of the Grinding Media in Ball Mills for Mineral …
The ball mills are either used in a dry-milling or wet-milling set-up depending on the needs of the industry in which they are utilised. The cement and …
اقرأ أكثر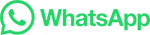
Energy-Mass-Size balance model for dynamic control of …
A dynamic model is developed for a wet overflow ball mill based on a set of mass and energy balances to simulate the mill. The energy balance relies on temperature and mass flow data. The key control parameters to be measured are mill temperature (feed and discharge streams), mill power draw and the mass flow rate in the feed stream.
اقرأ أكثر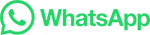