How to Get the Most Out of the Wet Milling Process
Wet milling, also known as wet grinding, involves the use of mechanical energy to break down materials by suspending particles in a liquid slurry and then dispersing those particles through shearing or …
اقرأ أكثر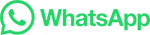
Ball milling as a mechanochemical technology for …
A comparative study on wet and dry mechanical ball milling of sawdust biochar showed that ball milling of biochar with water resulted in smaller and more dispersed particles as well as more diverse functional groups than dry ball milling for the same treatment time (12 h) (Yuan et al., 2019). Wet ball milling is a green and labor …
اقرأ أكثر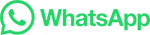
Preparation of graphene via wet ball milling and in situ …
Functionalized graphene (G-MA) was prepared by a facile wet ball milling strategy, which achieved exfoliation and functionalization of graphite simultaneously. The G-MA showed excellent dispersion in water and polar solvents. Thus, a G-MA coating was prepared from G-MA in mixed solvents (H 2 O–ethanol) without binder or surfactant. The ...
اقرأ أكثر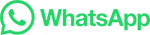
Everything You Need to Know About Wet Media …
Wet milling machines can include horizontal media mills, attritor mills, cascading type ball and/or bead mills, and basket or batch mills. Unlike dry mechanical and jet milling processes, wet milling requires multiple, …
اقرأ أكثر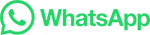
Ultrafine aramid nanofibers prepared by high-efficiency wet ball
The strong shear and collision forces from ball-milling induced stripping and splitting effects on the macroscopic fibers, which promoted the penetration and expanded the contact interfaces between reactants, thus accelerating the …
اقرأ أكثر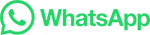
The Scalability of Wet Ball Milling for The Production of
Results: Comparable particle sizes of about 151 nm to 190 nm were obtained for both active pharmaceutical ingredients at the same milling time and milling speed when the drugs were processed at 10 g using low energy wet ball milling or 120 g using high energy wet ball milling in batch mode, respectively. However, an adjustment of the milling ...
اقرأ أكثر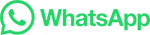
Modeling of Bauxite Ore Wet Milling for the Improvement …
Size reduction is a necessary operation in mineral processing plants and provides the desired size for separation operations and the liberation of the valuable minerals present in ores. Estimations on energy consumption indicate that milling consumes more than 50 % of the total energy used in mining operations. Despite the fact …
اقرأ أكثر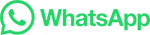
Modelling of mill load for wet ball mill via GA and SVM …
The load of wet ball mill is a key parameter for grinding process, which affects the productivity, quality and energy consumption. A new soft sensor approach based on the mill shell vibration ...
اقرأ أكثر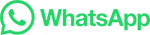
Chapter 1 – Soils Tex-116-E, Ball Mill Method for …
The result of this test is known as the Wet Ball Mill (WBM) value. Apparatus The following apparatus is required: ♦ wet ball mill machine, consisting of a watertight steel cylinder, closed at one end, with inside dimensions of 258.8 ± 3 mm (10.188 ± 1/8 in.) in diameter and 273.1 ± 3 mm (10.75 ± 1/8 in.) in length.
اقرأ أكثر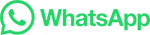
Ball Mill Loading
The starting point for ball mill media and liquid charging is generally as follows: 50% media charge. Assuming 26% void space between spherical balls (non-spherical, irregularly shaped and mixed-size media will …
اقرأ أكثر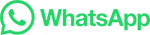
_Taurus
NETZSCH Ecutec's Taurus has the most advanced technology in Mills using Grinding Media for micronizing. A rotating robust steel drum with liners is supplying kinetic energy to grinding media inside the mill. These grinding media are crushing and grinding fresh product due to impact and friction. The lining as well as the grinding media can be ...
اقرأ أكثر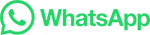
Laboratory Ball Mills | Bench and Floor Jar Mills
Jar Mills are available in bench or floor models and have one to six jar capacities in 1, 2 or 3 tiers. They are used for wet or dry grinding, mixing and blending of ores, chemicals, ceramics, glass, and more. Benchtop Labmill is lightweight and compact and easily adjusts to four sizes of milling jars, 16-320oz (0.5–10L).
اقرأ أكثر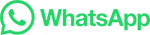
Solved The feed size to a single stage wet ball mill was 9.5
The mill was expected to produce a product of 80% passing 150 microns. The feed rate to the mill was 300 t / h. The ball mill grindability test at 65 mesh showed 12 kWh / t. The internal diameter of the ball mill was 5.03 m and the length to diameter ratio 0.77 . The steel balls occupied 18% of the mill. The total load occupied 45% of the mill
اقرأ أكثر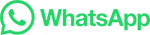
Ball Mill Adalah? Prinsip Kerja, Bagian, Komponen Dan …
Ball Mill adalah suatu mesin yang berbentuk silinder (tabung) dan berfungsi untuk menggiling material kasar menjadi material yang halus. Mesin ini memanfaatkan bola-bola keras untuk menumbuk dan menggesek material kasar sehingga bisa menjadi halus. Ball Mill menjadi salah satu mesin yang sangat penting dalam proses produksi di suatu …
اقرأ أكثر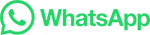
Modern Wet Milling and Material Processing
The SMP-45 Supermill 8 PLUS. The SMP-200 Duplex Supermill 8 PLUS. The SMP-15L Recirculation Process System. …
اقرأ أكثر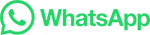
What is Wet Grinding Process | Wet Ball Milling Method and …
The wet ball milling process, a popular choice in many sectors, employs a ball mill to achieve a fine grind. This method is particularly effective for materials that are too hard for standard milling. Steps in Wet Ball Milling Process.
اقرأ أكثر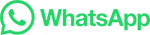
Wet milling
Wet milling is successfully used for many applications in the pharmaceutical industry because it works well with API (active pharmaceutical ingredients). IKA dispersing …
اقرأ أكثر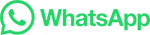
What are the Advantages of Wet Ball Milling?
1. Better Grinding Efficiency. The liquid in wet ball milling acts as a lubricant, reducing friction and improving the grinding efficiency. The particles are more effectively ground …
اقرأ أكثر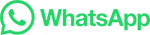
(PDF) Modeling of operating parameters for wet ball mill …
Heng Yue. Load of the ball mill affects the productivity, quality and energy consumption of the grinding process. But sensors are not available for the direct measurement of the key parameters for ...
اقرأ أكثر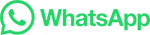
Ball milling: a green technology for the preparation and
The effect of ball mill on the morphological and structural features of cellulose has been described by Okajima and co-workers. 20 They treated microcrystalline cellulose derived from cotton linters in a planetary ball mill at 200 rpm for 4–8 hours in dry and wet conditions with three solvents (water, toluene, 1-butanol). They observed that ...
اقرأ أكثر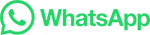
Ball Mill Loading
Abbe Jars are available in a wide range of sizes and materials. Milling jars are small scale version of the ball mills and are typically used in the laboratory or small scale producti. More. Talk with the Experts at Paul O. …
اقرأ أكثر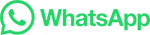
Properties of cellulose nanofibril produced from wet ball milling …
Ball Milling. Cellulose materials were wet ball-milled with a PQ-N2 planetary ball mill (Livingston, NJ, USA). The enzymatically treated fibers were diluted to 1.0 wt% and then agitated by a mechanical blender for 10 min. Then 150 g of the diluted fibril slurry were put into an agate jar of 500 mL capacity.
اقرأ أكثر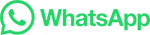
Ball Mill Loading
The starting point for ball mill media and liquid charging is generally as follows: 50% media charge. Assuming 26% void space between spherical balls (non-spherical, irregularly shaped and mixed-size media will increase or decrease the free space) 50% x 26% = 13% free space. Add to this another 45% to 50% above the ball charge for total of 58% ...
اقرأ أكثر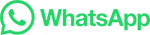
How Ball Mills Contribute to Battery Technology
In this article, the four main application areas of Retsch laboratory ball mills in battery technology will be outlined. Each area can be categorized under specific application examples: Section 1: Reduction of the material particle size in batteries. Section 2: Mixing and coating of particles.
اقرأ أكثر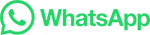
Continuous grinding in a small wet ball mill. Part V. A study …
DOI: 10.1016/0032-5910(73)80065-8 Corpus ID: 95763965; Continuous grinding in a small wet ball mill. Part V. A study of the influence of media shape @article{Kelsall1973ContinuousGI, title={Continuous grinding in a small wet ball mill.
اقرأ أكثر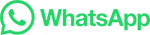
MILL OPERATOR
6) When operating continuous ball mills, regulates inflow of materials and observes outflow to ensure attainment of specified product. 7) May tend mill utilizing vacuum or other pressure. 8) May tend steam-jacketed mill that heats materials during processing. 9) May use mill to mix materials for wet or dry grinding. 10) May keep production records.
اقرأ أكثر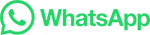
Wet Ball Mill for Metal Ores and Non-ferrous …
Wet ball mill is a kind of equipment which uses grinding medium and a certain amount of liquid (water or anhydrous ethanol) to grind materials. Unlike dry ball mill, wet ball mill adopts the wet grinding …
اقرأ أكثر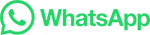
Wet Milling vs Dry Milling: The Differences, Advantages, and …
See more on hockmeyer
Explore further
The Differences between Dry Milling and Wet MillingWebWet Ball Mill Grinding. JSB Industrial Solutions • Sep 15, 2023. Dry grinding and wet grinding are two different methods of milling that have their own advantages …
اقرأ أكثر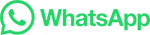
Preparation of graphene by exfoliation of graphite using wet ball milling
Wet ball milling was used to exfoliate graphite platelets into graphenes in a liquid medium. Multi-layered graphite nanosheets with a thickness of 30 to 80 nm were dispersed into N,N-dimethylformamide (DMF) and exfoliated by shear-force-dominated ball milling carried out in a planetary mill. After high-speed centrifugation, irregular shaped single- and few-layer …
اقرأ أكثر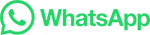
The Scalability of Wet Ball Milling for The Production of
However, an adjustment of the milling speed was needed for the 2 kg scale produced using high energy wet ball milling in recirculation mode to obtain particle sizes comparable to the small scale ...
اقرأ أكثر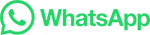