Ball Mill Design/Power Calculation
The work index will also have a considerable variation across one ore body or deposit. ... A wet grinding ball mill in closed circuit is to be fed 100 TPH of a material with a work index of 15 and a size …
اقرأ أكثر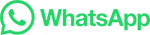
Fine grinding in a horizontal ball mill
The main reason ball mills are not utilised for fine grinding is the perceived poor energy efficiency generally experienced when grinding to fine sizes. However there …
اقرأ أكثر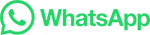
Copper Ore Crushing, Grinding & Flotation
Grinding and Flotation. Fine ore at minus 19mm (¾") sizing is fed at a controlled rate into the open-circuit 2600mm x 3960mm (8'-6 x 13'-0) Hardinge rod mill at an average feed rate of 2,106 STPD or 87.75 STRH. Rod mill discharge at a nominal size of minus 16 mesh and a pulp density of 75 percent solids combines with ball mill …
اقرأ أكثر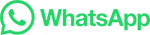
Optimization of Ball Mill Grinding of a Limestone-Type …
The effect of ball size and interstitial filling on the performance of dry ball mill grinding was investigated for a limestone-type brecciated uranium ore. The optimum grinding was obtained with the combination of different balls (12.7–37.5 mm) and interstitial filling of 50% (20% ball filling ratio at fixed material filling ratio = 4%). The net …
اقرأ أكثر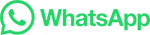
Ore Crushing, Sand Making, Grinding Machinery
200+ Ore Milling Ball Mill & Raymond Mill. Horizontal ball mill and vertical Raymond mill can be used for milling of 200+ ores, with a fineness of 100-2500 mesh. ... We have designed 300+ ore crushing and grinding projects for users in more than 40 countries and regions around the world.
اقرأ أكثر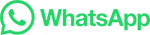
Ball Mill Is The Key To Grinding Lithium Ore
The grinding equipment of the first stage can be wet grid ball mills, rod mills, etc. When secondary grinding is required, a wet overflow ball mill can be selected as the grinding equipment at this stage. Grid type ball mill. Its advantage is that the ore discharge speed is fast, it can reduce the over-crushing of ore, and at the same time it ...
اقرأ أكثر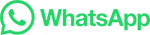
Ball Mill (Ball Mills Explained)
Ball mills are the most common grinding machine employed in the mining industry. Grinding occurs in a single stage, or multiple stages. Multiple stages may include a rod mill followed by a ball mill (two stage circuit), …
اقرأ أكثر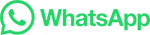
Population balance model approach to ball mill optimization in iron ore
The data analysis showed that the ratio of grinding net powers between ball and vertical mills is approximately 1.35 for all samples tested. View full-text Article
اقرأ أكثر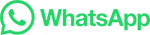
Grinding Ball Design
Grinding Ball Design. Table of Contents. Grinding balls are essential mechanical components in ball and semiautogenous (SAG) mills. Their function is crushing and grinding ore rocks weighing up to 45 kg (100 lb) preparatory to recovery of valuable minerals, from lead through rare earth elements, which are essential to the approaching …
اقرأ أكثر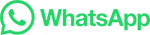
Population balance model approach to ball mill optimization in iron ore
An analysis of the kinetics of dolomite grinding in a dry ball mill reveals that the following approximations apply for the parameters of the batch grinding model: the size discretized selection ...
اقرأ أكثر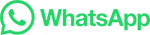
Microwave Pretreatment on Copper Sulfide Ore: Comparison of Ball Mill
Ball mill grinding tests were performed in a 20 cm × 20 cm stainless steel laboratory rotary mill. It was operated at a constant speed of 85 rpm (84% of the critical speed). The diameter of stainless-steel balls is 16–42 mm with a total weight of 8.79 kg and ball voids of 43.33%, which is 25% of the total volume of the mill.
اقرأ أكثر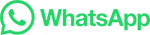
(PDF) The effects of iron ore concentrate grinding
An iron ore concentrate sample was ground separately in a pilot-scale HPGR mill in multiple passes and a dry open-circuit ball mill to increase the specific surface area of particles.
اقرأ أكثر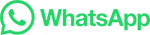
(PDF) Grinding Media in Ball Mills-A Review
One of the most used tumbling mills is the ball mill. This paper reviews different types of grinding media that have been developed and improved over the years …
اقرأ أكثر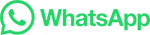
Grinding in Ball Mills: Modeling and Process …
The paper presents an overview of the current methodology and practice in modeling and control of the grinding process in industrial …
اقرأ أكثر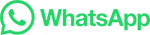
AMIT 135: Lesson 7 Ball Mills & Circuits – Mining …
Mill Type Overview. Three types of mill design are common. The Overflow Discharge mill is best suited for fine grinding to 75 – 106 microns.; The Diaphram or Grate Discharge mill keeps coarse particles within the mill …
اقرأ أكثر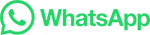
Experimental investigation of the impact breakage …
In the grinding process of the ball mill, the grinding media rotates with the cylinder and impacts the particles at different drop heights. The particles exist in a random and unrestricted state. ... The results indicated that the breakage of iron ore particles in the ball mill is the cumulative impact breakage with different impact energy and ...
اقرأ أكثر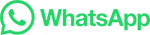
A Review of the Grinding Media in Ball Mills for Mineral …
The ball mill is a rotating cylindrical vessel with grinding media inside, which is responsible for breaking the ore particles. Grinding media play an important role in the comminution of mineral ores in these mills. This work reviews the application of balls in mineral processing as a function of the materials used to manufacture them and the …
اقرأ أكثر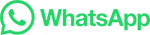
Small Ball Mill
0.5 to 15 TPH Small Scale Miner's Ball Mill. US$ 30,000. Our small-scale miner's Ball Mills use horizontal rotating cylinders that contain the grinding media and the particles to be broken. The mass moves up the wall of the cylinder as it rotates and falls back into the "toe" of the mill when the force of gravity exceeds friction and ...
اقرأ أكثر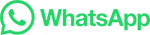
A Review of the Grinding Media in Ball Mills for Mineral …
The ball mill is a rotating cylindrical vessel with grinding media inside, which is responsible for breaking the ore particles. Grinding media play an important …
اقرأ أكثر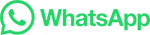
Ball Mills | Industry Grinder for Mineral Processing …
A ball mill, also known as a ball grinding machine, is a well-known ore grinding machine widely used in mining, construction, and aggregate applications. JXSC started the ball mill business in 1985, supplying …
اقرأ أكثر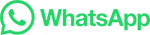
A Review of the Grinding Media in Ball Mills for Mineral …
The size of 30 mm was optimum for raw materials of −0.45 + 0.15 mm and −0.15 mm. The optimal ball size distribution was 12 mm (40%), 20 mm (40%), 32 mm (10%), and 40 mm (10%) for dry fine-grinding of calcite ore. Finer ball loads were unable to break coarser particles nipped in the feed.
اقرأ أكثر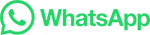
Demystifying The Sag Mill: What Is It And How Does It Work?
High throughput: SAG mills are capable of processing large amounts of ore, making them ideal for operations that require high production rates.They can handle both coarse and fine grinding, resulting in improved overall efficiency. Energy savings: Compared to traditional ball mills, SAG mills consume less energy, leading to …
اقرأ أكثر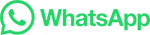
Batch Ball Mill Grinding
Batch Ball Mill Grinding. Chert, which is very hard, and dolomite, which is moderately hard, were selected for use in a study of the effect of different speeds and ore charges in batch tests. Mill, ball load, and pulp consistency always were the same. Results for chert are shown in the upper section of table 13, and for dolomite in the lower ...
اقرأ أكثر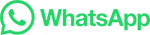
Ball And Mill, Grinding Steel Ball, Forged Balls
About Us. Jianlong Group ranked the 363rd on Forture Global 500, the 119th on China's Top 500 Companies and the 30th on China's Top 500 Private Enterprises in 2021. Main business involves steel, mining, shipbuilding, mechanical and electrical, forging, wear-resistant materials and other fields,with more than 50 larger subsidiary corporation ...
اقرأ أكثر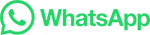
Grinding in Ball Mills: Modeling and Process …
Grinding in ball mills is an important technological process applied to reduce the. size of particles which may have different nature and a wide diversity of physical, mechanical and chemical ...
اقرأ أكثر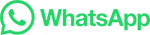
Grinding Mill Design & Ball Mill Manufacturer
When choosing primary autogenous grinding, run of mine ore up to 200-300 mm in size is fed to the mill. When using a crushing step before the grinding, the crusher setting should be 150-200 mm. The feed trunnion opening must be large enough to avoid plugging. ... Big dry grinding ball mills are often two-compartment mills, with big …
اقرأ أكثر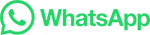
The Effect of Grinding Media on Mineral Breakage Properties
The breakage and liberation of minerals are the key to fluidized mining for minerals. In the ball milling process, steel balls function as not only a grinding action implementer but also energy carrier to determine the breakage behavior of ores and the production capacity of the mill. When ground products present a much coarse or much …
اقرأ أكثر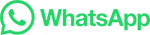
Fine grinding in a horizontal ball mill
The fine grinding of ores is increasing due to the depletion of coarse grained, easily processed ore bodies and the increased need to process disseminated, fine grained deposits. The main reason ball mills are not utilised for fine grinding is the perceived poor energy efficiency generally experienced when grinding to fine sizes.
اقرأ أكثر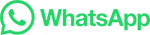
Ball Mill Is Indispensable For Lithium Ore Processing
The grinding and grading stage of lithium ore is to ensure that lithium minerals are fully dissociated from gangue mineral monomers. Therefore, lithium ore extraction is inseparable from ore grinding, and …
اقرأ أكثر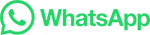
Ball mill grinding machine for gold ore processing in Tanzania
Ball mill is a commonly used machine for grinding and processing materials, including gold ore. In Tanzania, as in many other mining and mineral processing operations, ball mills are often used to grind and refine ore to extract valuable metals like gold.Ball mill grinding machines are commonly used in gold ore processing in …
اقرأ أكثر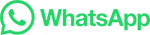