What Are the Differences between Dry and Wet Type Ball Mill?
The wet ball mill has a low noise, and low environmental pollution. The wet ball mill has a simple transportation device with less auxiliary equipment, so the investment is about 5%-10% lower than that of a dry ball mill. The grinding particle size is fine and uniform. The wet ball milling can not only grind agglomerate into fine particles, but ...
اقرأ أكثر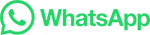
electrical connection for wet ball mill
water quenching system for mill rolling SKY mining. water quenching system for mill rolling sher Water Quenching System For Mill Rolling 393 Views. ... electrical connection for wet ball mill photo mesin raw mill .
اقرأ أكثر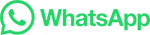
Ball Mill Trunnion Bearing Lube System
On a 11'-6" x 22'-0" Ball Mill, the trunnion bearing lubrication system provides continuous low pressure flood oil for cooling and lubrication of the bearings, and high pressure oil for hydrostatic lift of the feed and discharge trunnions during start-up of the mill. System monitors including pressure switches and flow monitors are provided, along with …
اقرأ أكثر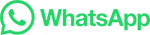
How to Prevent Common Problems and Safety Hazards
Follow the manufacturer's recommendations for ball size, charge, and mill speed. Ensure that adequate cooling is in place to prevent overheating and potential burns. Implement appropriate dust control measures, such as using a dust collection system or wet suppression. Use appropriate personal protective equipment, such as respirators and ...
اقرأ أكثر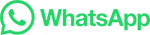
Planetary Ball Mill PM 300
Planetary Ball Mill PM 300 offers powerful grinding with dual stations handling up to 500 ml jars ideal for precise and fast tasks Learn more. ... Planetary Ball Mill PM 300 Wet and nano-scale grinding with the PM 300 . ... Electrical supply data: 200-240 V, 50/60 Hz: Power connection: 1-phase: Protection code: IP 20: Power consumption
اقرأ أكثر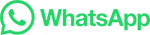
Effects of filling degree and viscosity of slurry on mill load
Wet milling. Load behaviour. Slurry filling. Slurry viscosity. Slurry pooling. 1. Introduction. Ball milling is ubiquitous in mineral processing but yet amongst the most …
اقرأ أكثر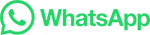
TECHNICAL SPECIFICATION OF WET BALL MILL EQUIPMENT (SUB ASSEMBLY OF FGD
- The bulk densities of the steel media typically used are: Balls 4650 kg/m3 Cylpebs 4700 kg/m3 Rods 6247 kg/m3 Cubes 5500 kg/m3
- For soft ore, ceramic media (90 °/o A l203) can be used (2200 kg/m3).
Explore further
(PDF) Grinding in Ball Mills: Modeling and Process …researchgateBall Mill Operation -Grinding Circuit Startup & Shutdown …911metallurgistRecommended to you based on what's popular • FeedbackBall Mill Design/Power Calculation
One-pot wet ball-milling for waste wire-harness recycling
The wet ball-milling tests were conducted at different rotating speeds (20, 25, 35, and 45 rpm) using the 20-mm balls. Figure 7a shows the wet ball-milling separation results in n-butyl acetate. Complete separations are achieved within 90, 70, 60, and 50 min of wet ball milling at rotating speeds of 20, 25, 35, and 45 rpm, respectively.
اقرأ أكثر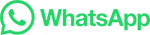
Wet Continuous Production Mills
C-60. Continuous Attritors are best suited for the continuous production and fast grinding of large quantities of material. They are designed to deliver hours of low-cost, maintenance-free operation. The basic model features a system that does not require an expensive shaft seal. Continuous Attritors come in two basic types, "C" and "H ...
اقرأ أكثر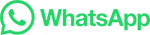
Wet ball milling of niobium by using ethanol, determination …
This study investigates the effect of using ethanol as the process control agent during the wet ball milling of niobium (Nb). Dried nanocrystal Nb powders, of high purity, with particle sizes ...
اقرأ أكثر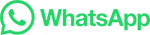
Ball-milling: A sustainable and green approach for starch …
Ball-milling is a low-cost and green technology that offers mechanical actions (shear, friction, collision, and impact) to modify and reduce starch to nanoscale size. It is one of the physical modification techniques used to reduce the relative crystallinity and improve the digestibility of starch to their better utility.
اقرأ أكثر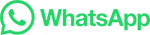
Wet ball milling of niobium by using ethanol, determination …
Fayyaz, A. et al. E ect of dry and wet ball milling process on critical powder loading and mixture properties of ne WC-10Co-0.8 VC powder . Jurnal Te knologi 59, 13 (2012).
اقرأ أكثر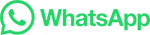
Wet Ball Mills
Wet Ball Mills are Ball Mills that are used widely in the ore beneficiation industry,as well as the building material industry such as glass. During the producing phase, the material and …
اقرأ أكثر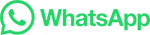
Wet ball milling of niobium by using ethanol, determination …
Abstract. This study investigates the effect of using ethanol as the process control agent during the wet ball milling of niobium (Nb). Dried nanocrystal Nb powders, …
اقرأ أكثر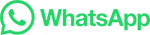
Planetary Ball Mill PM 400
Planetary Ball Mill PM 400 Wet and nano-scale grinding with the PM 400. ... Electrical supply data: different voltages: Power connection: 1-phase: Protection code: IP 30: Power consumption ~ 2100 W (VA) W x H x D closed: 836 x 1220 (1900) x …
اقرأ أكثر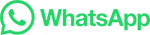
Load State Identification Method for Wet Ball Mills Based …
To overcome the difficulty of accurately judging the load state of a wet ball mill during the grinding process, a method of mill load identification based on the singular value entropy of the modified ensemble empirical mode decomposition (MEEMD) and a probabilistic neural network (PNN) classifier is proposed. First, the MEEMD algorithm is …
اقرأ أكثر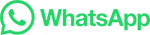
SFM-1 (QM
MTI Corporation. 860 South 19th Street, Richmond, CA 94804, USA Tel: 510-525-3070 Fax: 510-525-4705 E-mail:info@mtixtl Web site: 1. Purpose. QM series planetary ball mills could grind or mix solid particles of different granularities and materials, suspension and paste with dry and wet methods.
اقرأ أكثر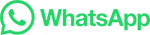
Effects of filling degree and viscosity of slurry on mill load
The conductivity probe, on the other hand, is made of an electrode which establishes an electric connection with the ground when in contact with water present in slurry. The voltage signal generated is translated into presence/absence of slurry. ... Definition of the load behaviour in a wet ball mill (after De Haas, 2008).
اقرأ أكثر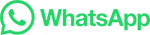
Operating Manual
Type of Mill Planetary ball mill, high-energy ball mill Grinding Containers Canister type jar with multiple balls Display Touch screen Grinding Mechanism Grinding balls of hardened …
اقرأ أكثر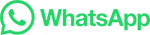
Operating Instructions for Oscillating Mill MM 200
Electrical connection ... fibrous, hard and brittle materials in the wet and dry state. The MM 200 is designed for very small quantities of approx. 0.5 to 8 ml. This corresponds to 25% of the ... The milling ball(s) may otherwise damage the milling cups. Do not make any alterations to the machine and use
اقرأ أكثر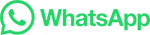
Wet ball milling of niobium by using ethanol, …
Milling was performed under the condition of a wet ball milling process. For the milling process, 40.12 g of the as-received Nb powder were loaded into two separate
اقرأ أكثر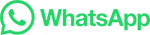
Wet ball mill_Ball mill_PRODUCT_Tongli Machinery
Mill Shell: The foundation of the wet ball mill, the mill shell, is a cylindrical structure made of premium-grade steel.Tongli heavy machinery is equipped with a large annealing furnace of 6.5x6.5x20m and a 6.5x6.5x20m large sandblasting room, which can conduct overall heat treatment and sandblasting on the ball mill to ensure the service life and appearance of …
اقرأ أكثر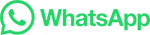
Circulation Mill System Zeta
The high-speed mill system Zeta ® with improved peg grinding system optimizes your production capacity, energy demand and quality. Designed for circulation operation and multi-pass operation, you achieve high throughput rates and high quality with a narrow particle size distribution for higher viscous products.. A minimal control expenditure is …
اقرأ أكثر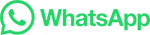
Materials Development Using High-Energy Ball Milling: A …
High-energy ball milling (HEBM) of powders is a complex process involving mixing, morphology changes, generation and evolution of defects of the crystalline lattice, and formation of new phases. This review is dedicated to the memory of our colleague, Prof. Michail A. Korchagin (1946–2021), and aims to highlight his works on the synthesis of …
اقرأ أكثر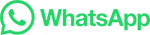
MM 500 Mixer Mill | Glen Mills, Inc.
The mixer mill MM 500 is a compact, versatile bench-top unit which has been developed specially for dry, wet and cryogenic grinding of up to 2 x 45 ml sample material within seconds. With a maximum frequency of 35 Hz, it generates enough energy to produce particles in the nanometer range. The robust high-performance drive makes the mill ...
اقرأ أكثر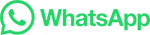
What is the Principle of Wet Ball Mill?
The principle of wet ball milling is based on the energy transfer between the grinding media and the material being ground. In the process of wet ball milling, the grinding media are typically made of steel or ceramics, and they are loaded into the mill in a specific proportion. As the cylinder rotates, the grinding media and the material being ...
اقرأ أكثر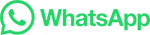
Dry ball milling and wet ball milling for fabricating copper–yttria
Yttria-reinforced copper matrix composites were prepared by dry ball milling (DBM) and wet ball milling (WBM), respectively, followed by spark plasma sintering (SPS). It is to determine which milling process is better for fabricating Cu–Y2O3 composites. It is found that Cu–Y2O3 composites synthesized by DBM exhibit better densification, …
اقرأ أكثر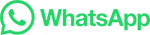
Physicochemical and structural characteristics of nano
Nano eggshell calcium (NEC) powder was prepared from biowaste chicken eggshells using wet ball milling. The characteristics of the NEC, including the zeta potential, micromorphology, elemental composition, particle size distribution, Ca 2+ concentration, and chemical structure, were investigated. According to the results, the …
اقرأ أكثر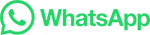
PM 100 Planetary Ball Mill | Glen Mills, Inc.
The PM 100 is a convenient bench top model with 1 grinding station. You may also be interested in the High Energy Ball Mill Emax, an entirely new type of mill for high energy input. The unique combination of high friction and impact results in extremely fine particles within the shortest amount of time. Add to Quote.
اقرأ أكثر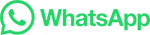