A Guide to Grinding Ceramics With Diamond Grinding Wheels
These wheels are composed of three fundamental components: Abrasive Grains: The heart of a diamond grinding wheel lies in its abrasive grains. These grains consist of synthetic diamonds that are precisely bonded to the wheel's surface. The abrasive grains are responsible for the material removal process. Bond Material: Surrounding the …
اقرأ أكثر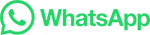
Material removal mechanism and corresponding models in the grinding …
Grinding is a key technology for difficult-to-machine materials, e.g., super alloys, ceramics, and composites. ... During the grinding process of long fiber-reinforced ceramic matrix woven composites, the ceramic matrix is readily fractured and removed by the fiber extrusion generated by the grinding force, which lowers the surface quality ...
اقرأ أكثر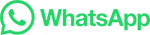
Study on grinding force of Si3N4 ceramics in random rotation grinding …
Grinding force is the most important characteristic parameter in the study of grinding machining mechanism, and it has an important influence on the quality of the machined surface and the service life of the grinding wheel. Accurate prediction of grinding force is significant to process improvement, machine tool design, and condition …
اقرأ أكثر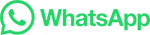
Fine Grinding of Ceramics with Attritors
for dry grinding, the batch Attritor can be operated in either a batch or continuous-feed mode. Table 1. Batch wet grinding process data A1 Material: ZTA (Al2O3/ZrO2) -50 mesh Attritor: 1-S, Al 2O 3 lined tank (5.7L) ZrO 2 sleeved agitator arms Media: 4.8mm ZrO 2 balls Formulation: ZrSiO 4/water (68.8% solids) Process Time: 3 hours Particle ...
اقرأ أكثر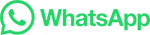
Vibratory Finishing Process Guide for Beginner
The process of vibratory finishing is carried on in a vibratory bowl or a vibratory tub for parts surface deburring, polishing, smoothing, cleaning, descaling, rust removal, radiusing, etc. The first vibratory finishing machine is tub-type, which was introduced in 1957. Five years later, in 1962, the bowl-type vibratory finishing machine is ...
اقرأ أكثر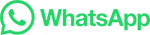
Ceramic CNC Machining: Enhancing Performance and …
CNC Milling. CNC milling for ceramics is a process in which a computer-controlled machine uses a rotating cutting tool to remove material from a ceramic workpiece to create a desired shape or form. One of the key advantages of CNC milling for ceramics is the ability to produce complex shapes with high precision.
اقرأ أكثر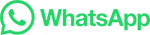
Precision Machining and Polishing Services
Leads in precision machining and polishing of hard materials like ceramics, quartz, and sapphire for critical applications. Experience unparalleled precision.
اقرأ أكثر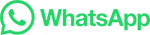
A Step-by-Step Guide on How to Grind Ceramic Tile
Follow these instructions to achieve the desired results. Step 1, Step 2, Step 3, Step 4, and Step 5 will guide you through the process of grinding porcelain tile effectively and safely. Step 1. Before you begin grinding porcelain tile, make sure to thoroughly clean the tile by washing it in clean water and light soap and drying it with a towel.
اقرأ أكثر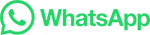
How to Grind Quartz Crystals: The Ultimate Guide
Step-by-Step Quartz Grinding Process. Grinding quartz typically involves multiple grinding steps utilizing different equipment: 1. Jaw Crusher. Feed raw quartz chunks into the jaw crusher either by hand or using a feeder belt conveyor. The movable jaw compresses the quartz against the fixed jaw crushing surfaces to fracture the material.
اقرأ أكثر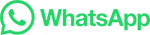
Grinding Machine: Definition, Uses, Types, and Applications
By Team Xometry. October 18, 2023. 17 min read. Grinding machines are versatile tools used in various industries for material removal, shaping, and finishing. This article explores the definition, uses, types, and practical applications of grinding machines in …
اقرأ أكثر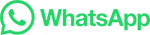
Ceramic Grinding Machines | Total Grinding Solutions (TGS)
Phone: 586-541-5300 EMAIL: sales@totalgrindingsolutions. Total Grinding Solutions Inc. 13265 East 8 Mile Road Warren, Michigan, USA 48089
اقرأ أكثر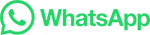
Ceramic Grinding & Machining Pillar Page
Ceramic grinding is an essential process in achieving tight tolerances in otherwise impossible-to-cut materials. Machining them requires superior tooling—such as special diamond tooling—that can create unique properties and high accuracy in the final components, which must meet complex and heavy-duty demands. ... Wafer Dicing …
اقرأ أكثر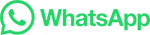
Machines and systems for the production of kitchenware | SACMI
Body and Glaze preparation. Our solutions consist of automated lines for dispensing the raw materials, Drum mills from 200 to 38,000 litres capacity suitable for grinding slip and glaze, blungers and turbo-dissolvers for perfect homogenisation, and spray-drying or extrusion systems. The range is complemented by quick and slow stirrers ...
اقرأ أكثر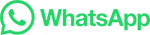
Grinding Processes | SpringerLink
Grinding is an essential process in the manufacture of virtually all types of mechanical equipment and cutting tools. For example, the production of rolling element bearings, automotive components, power generation equipment, and computer and electronic components is critically dependent on grinding processes.
اقرأ أكثر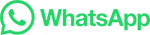
Grinding of composite materials
In a grinding process, an abrasive grain can be regarded as a cutting tool with a negative rake angle, and the undeformed chip thickness is close to the nano/micro-meter scale. ... The surface waviness of a traditional metallic material is highly related to the vibration of the machine tool, whereas for braided ceramic matrix composites, the ...
اقرأ أكثر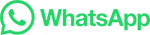
Precision grinding of ceramics and ceramic-matrix
After grinding process, the surface roughness R a of V-grooves on single crystal SiC, Al/SiCp, RB-SiC, and glass ceramic samples are 0.587 µm, 0.923 µm, 0.412 µm, 0.796 µm, respectively. The machining quality of microarray structures on RB-SiC sample is the best, and that on Al/SiCp sample is the worst.
اقرأ أكثر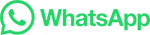
Modeling and prediction of surface roughness in ceramic grinding
The various parameters of the grinding process have been included in the model through chip thickness model. Therefore, this model can be used to predict surface roughness under different conditions of the parameters. The depth of cut and speed ratio are the two important parameters that can be varied on the grinding machine.
اقرأ أكثر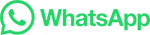
In-process detection of grinding burn using machine learning
The improvement of industrial grinding processes is driven by the objective to reduce process time and costs while maintaining required workpiece quality characteristics. One of several limiting factors is grinding burn. Usually applied techniques for workpiece burn are conducted often only for selected parts and can be time …
اقرأ أكثر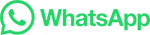
Massachusetts Ceramics Grinding, NH Alumina Oxide Ceramic Grinding …
We understand that attention to detail throughout the technical ceramic machining process and the application of advanced technical ceramics grinding techniques are the skills necessary to consistently meet the unique demands of our customers. At Ceramics Grinding we take pride in doing everything possible to keep work here in the USA.
اقرأ أكثر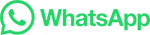
Automating the Grinding Process
Whether the process is cylindrical or profile grinding, automation, which can increase cycle time, throughput, consistency of part quality and taking real-time in-process measurements, is once again in demand. The reasons can be found in the benefits found in typical applications and the innovative and effective forms of automation available from …
اقرأ أكثر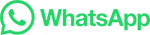
Energy conservation and consumption reduction in grinding …
The energy consumption of ceramic medium stirring grinding was calculated, and a feasibility evaluation was conducted on the ball mill, which provided a reference for optimizing the fine grinding process of similar mineral processing plants. Fig. 1 illustrates the test flows. Download : Download high-res image (380KB)
اقرأ أكثر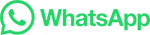
Ceramic Machining | Kadco Ceramics
Kadco Ceramics performs a variety of ceramic machining operations, such as: CNC Milling. Core drilling. Wafer dicing. ID slicing. Surface grinding. Piezoelectric machining. Our experienced machinists ensure that Kadco …
اقرأ أكثر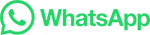
A Comprehensive Guide to Ceramic CNC Machining
Guided by the CNC program developed earlier, the CNC machine takes center stage. It skillfully converts the ceramic from its raw form into a component shaped with exactness. The hallmark of this process is its remarkable precision. The CNC machine operates with minimal margin for error, delivering uniform outcomes.
اقرأ أكثر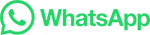
Grinding Media
Zirconium Oxide Balls. YTTRIA Stabilized, High purity 95% ZrO 2. Zirconium Oxide Balls (95% ZrO2) are the strongest, best wearing ceramic media for metal-free, pharmaceutical and food processing grinding. These balls have a white, shiny appearance. They are also available in 3⁄8″ and ½" cylinders. This 95% grade is high-cost. 95% Beads.
اقرأ أكثر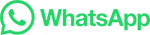
Understanding machinability improvements and removal …
LAAG procedures: (a) LAAG testing machine, (b) laser-induced ablation process, (c) belt grinding process, (d) C f /SiC composites samples before and after LAAG. Table 1. Experimental parameters. ... Investigations on grinding process of woven ceramic matrix composite based on reinforced fiber orientations. Compos. B Eng., 71 …
اقرأ أكثر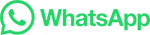
Development of a reliable grinding procedure for ceramic medical
For an economical manufacturing of ceramic scalpels, the total life cycle of medical instruments has to be considered. This includes reuse, reprocessing, cleaning and sterilization procedures (Fig. 3).Besides optimizing the raw materials, FCT Hartbearbeitungs adjusted the sintering process and the semi-finishing of the blanks for the further …
اقرأ أكثر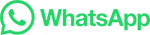
Material Processing Equipment for the Ceramic Industry
Material Processing Solutions for the Ceramic Industry. For many decades EIRICH has offered top technologies for the preparation of raw materials and bodies in the ceramic industry, centering on the basic operations of mixing and fine grinding. Many further developments in the field of ceramics and fine ceramics were made possible due to …
اقرأ أكثر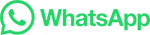
Handbook of Ceramics Grinding and Polishing
Grinding can produce very high shape accuracy and dimensional precision even with hard workpieces like ceramics, or permit a surface with a satisfactory roughness to be obtained, and is therefore an extremely important processing technique. Select Chapter 5 - Honing and Superfinishing. Book chapter Full text access.
اقرأ أكثر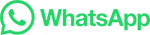
Ceramic Ball Mill For Grinding Materials
The grinding ceramic ball mill uses different ball mill ceramic liner types according to production needs to meet different needs. The finess of ceramic ball mills depend on the grinding time. The electro-hydraulic …
اقرأ أكثر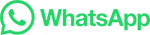
Technical Ceramics Manufacturers | Ferro-Ceramic Grinding
The Ferro-Ceramic Grinding Inc. staff are trained to operate multiple units Ferro-Ceramic Grinding Inc. is ISO 9001:2015 + AS9100D LEARN MORE Ferro-Ceramic Grinding Inc. machines over 15 different materials 55 Years of Excellence in Ceramic Machining LEARN MORE Ferro-Ceramic Grinding Inc. Our Quality is Built Into Our Process Manufacturing …
اقرأ أكثر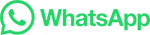