(PDF) Cement grinding optimisation
There is potential to optimise conventional cement clinker grinding circuits and in the last decade significant progress has been achieved. The increasing demand for "finer cement" products ...
اقرأ أكثر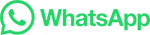
(PDF) Mining Activities, Cement Production Process and
The re are four stages in the manufacture of Portland cement: (1) crushing and grinding the raw . materials, (2) blending the materials in the correct proportions, (3) burning the prepared mix in.
اقرأ أكثر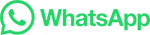
Energy-Efficient Technologies in Cement Grinding
1. Introduction. Cement is an energy-intensive industry in which the grinding circuits use more than 60 % of the total electrical energy consumed and account for most of the manufacturing cost [].The requirements for the cement industry in the future are to reduce the use of energy in grinding and the emission of CO 2 from the kilns. In recent …
اقرأ أكثر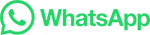
Overview of cement grinding: fundamentals, additives, technologies
Abstract. Grinding is an essential operation in cement production given that it permits to obtain fine powder which reacts quickly with water, sets in few hours and hardens over a period of weeks ...
اقرأ أكثر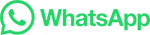
Everything you need to know about Crushers in Cement …
SUMMARY. The compression type crushers like jaw and gyratory crushers are used for hard and abrasive raw materials. Because of their limited reduction ratio of 3 …
اقرأ أكثر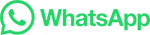
Grinding process is a critical stage in cement production
Pfeiffer (MVR 6000C6) technology for raw material and cement grinding respectively. The VRM is a type of grinding mill that combines crushing, grinding, drying, and classification functions into a single compact unit. It operates by rotating a grinding table, equipped with rollers, while the raw materials are fed into the mill from the top.
اقرأ أكثر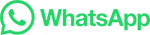
Effects of Crushing and Grinding on the Porosity of …
The objective of this paper is to study the effect of multiple crushing (producing particles 20/0.15 mm) and grinding (producing powder < 0.15 mm) steps on the properties of hard cement pastes used as model RCA. Hard cement paste represents a major part of the porosity of RCA.
اقرأ أكثر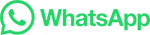
Fives | Mineral crushing with FCB VIF™ & FCB Rhodax® 4D
The FCB VIF™ impact crusher is designed for primary and secondary applications for crushing of: In primary applications, the crusher accepts blocks over 1 m 3 (35 ft 3) to obtain a 40 mm (1 1 / 2 in) product. In secondary application, the 300 mm (12 in) feed size produces a 20 mm (about 3 / 4 in) product. The FCB Rhodax® 4D offers advanced ...
اقرأ أكثر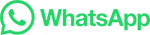
Difference Between Crushing and Grinding Operation
Crushing and grinding are two processes used in manufacturing and natural sciences. These processes are used to produce many different products, such as concrete, sand, and crushed stone. Additionally, both processes are used to extract natural resources like gold, copper, and iron. Essentially, crushing and grinding have many uses in daily life.
اقرأ أكثر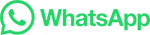
Breakthrough in Clinker Grinding
The cement industry is particularly reliant upon particle size reduction. Raw materials crushing and grinding seeks to reduce materials from roughly one meter cubes of blasted stone to a size where at least 80 percent of the raw material is less than 75 microns. Finish grinding of clinker and other cement
اقرأ أكثر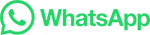
Know All About Cement Manufacturing Process in India | mycem cement
After crushing, the crushed limestone is piled longitudinally by an equipment called stacker / reclaimer. The stacker deposits limestone longitudinally in the form of a pile. The pile is normally 250 to 300 m long and 8-10 m height. ... Clinker and gypsum are pre crushed in a Roller press and subsequently fed into Cement mill for fine grinding ...
اقرأ أكثر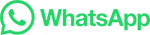
Environmental Guidelines for Cement Manufacturing
The preparation of cement includes mining; crushing and grinding of raw materials (principally limestone and clay); calcining the materials in a rotary kiln; cooling the …
اقرأ أكثر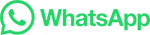
Recycled cement production energy consumption …
The process starts by submitting the concrete to mechanical crushing and grinding to obtain a mixture of unbounded particles of hydrated cement paste and aggregates. Since the efficiency of the separation between the cement paste and the aggregates is not the same for the particles of all sizes, the mixture is divided into 4 …
اقرأ أكثر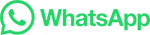
Cement grinding optimisation
To optimise cement grinding, standard Bond grinding calculations can be used as well as modelling and simulation techniques based on population balance model (PBM). ... Due to the "autogenous grinding action" it is especially efficient for high abrasive materials such as cement clinker. The crushing action is schematically presented in Fig. 3.
اقرأ أكثر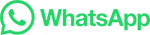
(PDF) Environmental Pollution by Cement …
The initial step in cement production involves crushing, grinding, blending, proportioning, and homogenizing the raw materials [10]. The resulting blended materials are then prepared for feeding ...
اقرأ أكثر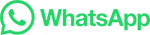
Advanced grinding in the cement industry | Request PDF
Comminution is a crucial part of cement manufacture, which includes crushing and grinding of raw materials and clinker grinding. Comminution, however, is extremely energy intensive and consumes ...
اقرأ أكثر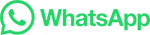
Breakthrough in Clinker Grinding
Raw materials crushing and grinding seeks to reduce materials from roughly one meter cubes of blasted stone to a size where at least 80 percent of the raw material …
اقرأ أكثر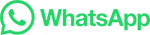
(PDF) Cement grinding optimisation | Alex Jankovic
This chemical reaction occurs at high temperature in a rotary kiln, grinding the cement clinker nodules to passing 90 microns in a dry circuit. fGrinding occurs at the beginning and the end of the cement making process. Approximately 1.5 tonnes of raw materials are required to produce 1 tonne of finished cement.
اقرأ أكثر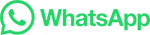
How Cement is Made
Stage 2: Grinding, Proportioning, and Blending The crushed raw ingredients are made ready for the cement-making process in the kiln by combining them with additives and grinding them to ensure a fine homogenous mixture. The composition of cement is proportioned here depending on the desired properties of the cement. Generally, …
اقرأ أكثر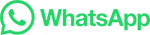
CRUSHING AND GRINDING SEMINAR
The purpose of the training is to Identify and understands necessary known and unknown information towards the completed cycle of the crushing and grinding system. Throughout the course the lectures are supplemented with exercises and case studies, allowing the participants to relate the course material to their cement crushing and grinding facility …
اقرأ أكثر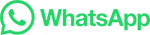
Fives | Selective crushing & grinding with FCB Rhodax® 4D
The FCB Rhodax® 4D is an inertial crusher featuring 3-6 alternate grinding phases, and gravity drop through the crushing chamber in a single pass.Interparticle compressive grinding enables full control of the grinding force.The FCB Rhodax® eliminates 2-3 stages of crushing and/or grinding, thus offering significant energy savings compared to …
اقرأ أكثر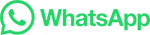
Effects of Crushing and Grinding on the Porosity of …
The objective of this paper is to study the effect of multiple crushing (producing particles 20/0.15 mm) and grinding (producing powder < 0.15 mm) steps on …
اقرأ أكثر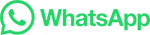
Cement Manufacturing
275. Cement Manufacturing. Industry Description and Practices. The preparation of cement involves mining; crushing, and grinding of raw materials (princi- pally limestone and clay); calcining the materi- als in a rotary kiln; cooling the resulting clinker; mixing the clinker with gypsum; and milling, storing, and bagging the finished cement.
اقرأ أكثر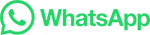
Effect of the Bionic Transverse Stripe on Wear Resistance and Crushing …
The results showed that the wear resistance and crushing performance of the grinding roller with striped grooves were better than those of the smooth grinding roller for quartz sand. For example, the wear of the 3# bionic grinding roller was reduced by 53.58% compared with the average wear amount of a normal grinding roller, and the crushing ...
اقرأ أكثر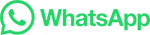
(PDF) Effects of Crushing and Grinding on the Porosity of …
The objective of this paper was to study the impact of crushing and grinding on the porosity of hardened cement paste, which is responsible for the high values of recycled concrete aggregate (RCA ...
اقرأ أكثر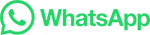
Crushing | industry | Britannica
In cement: Crushing and grinding. All except soft materials are first crushed, often in two stages, and then ground, usually in a rotating, cylindrical ball, or tube mills containing a charge of steel grinding balls. This grinding is done wet or dry, depending on the process in… Read More; mining
اقرأ أكثر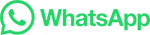
Cement Kilns: Size Reduction and Grinding
The cement industry processes requiring fine grinding are rawmix preparation, fuel preparation and grinding of clinker to make cement. All three may require a preliminary crushing stage. In the case of raw materials, attempts have always been made to minimise the amount of crushing needed by extracting the rock in the finest possible state.
اقرأ أكثر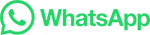
A review of the effectiveness of Life Cycle Assessment for …
The preparation of cement consists of grinding cement, blending and cement storage in silos (GHG, 2008). In this stage, ... and the handling and shipping of the cement), crushing grinding and mixings, and energy consumption in each production process. However, the cradle-to-gate method is predominantly used in cement LCA …
اقرأ أكثر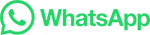
Air Pollution Associated with Total Suspended Particulate …
The study shows that the cement grinding plant has various dust sources that cement workers potentially expose daily. The TSP concentration in this study was in the range of 0.15 and 25.62 mg m −3. The results of the TSP measurement reveal that four out of six processes in the cement grinding plant exceeded the PEL for an 8-h working shift.
اقرأ أكثر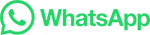