Converting a ball mill from overflow to grate discharge
Therefore, the need to make full use of these machines and their installed power is critical, so that this energy is effectively utilised. Converting a ball mill from overflow to grate discharge involves installing a grate inside the mill at the discharge end. The grate holds the balls inside the mill but allows the slurry to pass through, and ...
اقرأ أكثر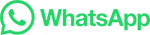
Ball Mill Design-Optimization Of Feeding Device
The feeding steps of this ball mill design feed are as follows. The. ballmillssupplier. info@ballmillssupplier. Tel: +86 327 5081 703. material enters the ball mill through …
اقرأ أكثر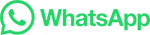
Ball Mill Design-Optimization Of Feeding Device
The feeding steps of this ball mill design feed are as follows. The. ballmillssupplier. info@ballmillssupplier. Tel: +86 327 5081 703. material enters the ball mill through the cast iron feeding slide, and. the slide is made on the support. The material enters the conical. funnel from the slider, and the funnel is embedded in the inner.
اقرأ أكثر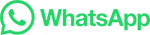
A CRITICAL REVIEW OF GRINDING DESIGN …
• Transfer size (T80) is the term used to describe the SAG mill product that is sent to the ball mill. For peak performance and balancing the power available in the SAG mill and ball mill, the transfer size must be measured and controlled. • The transfer size will be 500 microns using a 12mm opening trommel. This can be true under special
اقرأ أكثر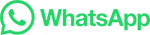
Ball Mills
Steel-Head Ball-Rod Mills are available in any one of five different types of discharge: 1. Overflow, 2. perforated overflow, 3. return spiral, 4. grate, and 5. peripheral. To best serve your needs, the Trunnion can be furnished with small (standard), medium, or large diameter opening for each … See more
اقرأ أكثر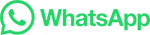
How Ball Mills Contribute to Battery Technology
In this article, the four main application areas of Retsch laboratory ball mills in battery technology will be outlined. Each area can be categorized under specific application examples: Section 1: Reduction of the material particle size in batteries. Section 2: Mixing and coating of particles.
اقرأ أكثر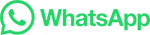
Design of Three-chamber Ball Mill
In this paper, the design method of three chamber ball mill is introduced. Comchambered with the design of Φ 3.5 × 13m three-chamber ball mill, the design …
اقرأ أكثر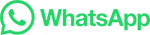
(PDF) Design of Three-chamber Ball Mill
In this paper, the design method of three chamber ball mill is introduced. Comchambered with the design of Φ 3.5 × 13m three-chamber ball mill, the design process of ball mill is...
اقرأ أكثر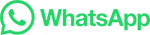
Ball Mill | SpringerLink
Peripheral discharge ball mill, and the products are discharged through the discharge port around the cylinder. According to the ratio of cylinder length (L) to diameter (D), the ball mill can be divided into short cylinder ball mill, L/D ≤ 1; long barrel ball mill, L/D ≥ 1–1.5 or even 2–3; and tube mill, L/D ≥ 3–5. According to the ...
اقرأ أكثر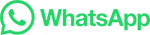
Ball Mill Maintenance & Installation Procedure
Ball Mill Sole Plate. This crown should be between .002″ and . 003″, per foot of length of sole plate. For example, if the sole plate is about 8′ long, the crown should be between .016″ and .024″. Ball Mill Sole …
اقرأ أكثر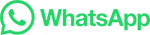
Pellet mill design
lifetime use. A pellet mill is considered to be the type of machine that can be subjected to "shock loads", so there is typically at least a 2:1 safety factor built into the design of the main driving members and at least a 10-year life expectancy on the design of the bearings used to prevent premature part failure.
اقرأ أكثر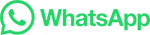
Optimization Of Ball Mill Feeding Device Design
The feeding steps of this ball mill design feed are as follows. The. ballmillssupplier. info@ballmillssupplier. Tel: +86 327 5081 703. material enters the ball mill through the cast iron feeding slide, and. the slide is made on the support. The material enters the conical. funnel from the slider, and the funnel is embedded in the inner.
اقرأ أكثر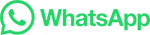
(PDF) DESIGN AND FABRICATION OF MINI BALL …
The ultimate crystalline size of graphite, estimated by the Raman intensity ratio, of 2.5 nm for the agate ball-mill is smaller than that of 3.5 nm for the stainless ball-mill, while the milling ...
اقرأ أكثر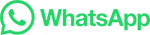
Using modelling and simulation for the design of full scale …
Abstract. Computer simulation of ball mill cicuits has been found to be very valuable for optimisation where existing plant data can be used to calibrate the …
اقرأ أكثر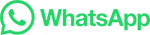
Design, fabrication and performance analysis of mini ball …
These forces are generated due to particle movement in the mill jar, the motion of balls and contact zones. The ball milling design significantly depends on the size of mill jar, required particle size distribution of powder and grinding media (balls) [13], [14], [15]. The main purpose of milling process is to obtain required particle size of the powder …
اقرأ أكثر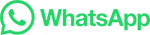
Stirred mills
advantages over traditional ball milling in various applications. It is capable of handling a wide range of feed sizes typically from 400 to 90 microns. Support from Outotec experts Outotec draws from more than 100 years of mill design and manufacturing expertise, and over four decades of successful Vertimill® applications.
اقرأ أكثر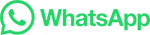
(PDF) DESIGN AND FABRICATION OF MINI BALL MILL- METHODOLOGY …
This project is to design and fabricate the mini ball mill that can grind the solid state of various type of materials into nano-powder. The cylindrical jar is used as a mill that would rotate the ...
اقرأ أكثر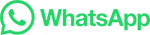
Operating Manual
Figure 1. Planetary Mill (front view) Figure 2. Planetary Mill (back view) Door Handle Emergency Stop Door Handle USB Control Panel On/Off Switch Electrical Inlet Door (closed) 4.0 Setting Up The 8200 Planetary Mill weighs 250 lb (113 kg). The door rotates to open and close from left to right with the handle atop the mill.
اقرأ أكثر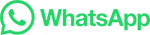
Ball Mill Application and Design
Ball Mill Application and Design. Ball mills are used the size reducing or milling of hard materials such as minerals, glass, advanced ceramics, metal oxides, solar cell and …
اقرأ أكثر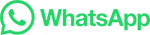
AMIT 135: Lesson 7 Ball Mills & Circuits – Mining Mill …
Ball Mill Design. A survey of Australian processing plants revealed a maximum ball mill diameter of 5.24 meters and length of 8.84 meters (Morrell, 1996). Autogenous mills range up to 12 meters in diameter. The length-to-diameter ratios in the previous table are for normal applications. For primary grinding, the ratio could vary between 1:1and ...
اقرأ أكثر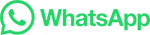
Ball Mill Liner Design
For 60 mm (2.5″) and smaller top size balls for cast metal liners use double wave liners with the number of lifters to the circle approximately 13.1 D in meters (for D in feet, divide 13.1 D by 3.3). Wave height above the liners from 1.5 to 2 times the liner thickness. Rubber liners of the integral molded design follow the cast metal design.
اقرأ أكثر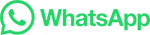
Grinding Mill Design & Ball Mill Manufacturer
Type CHRK is designed for primary autogenous grinding, where the large feed opening requires a hydrostatic trunnion shoe bearing. Small and batch grinding mills, with a diameter of 700 mm and more, are …
اقرأ أكثر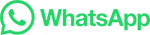
MD Series mill discharge pumps
Our extensive range of pumps cover flows of up to 13,500 m 3 /h. With inlet sizes ranging from 250 mm to 900 mm with either metal or rubber lining, we can ensure that you will always find the correct mill discharge pump for your process needs. The hydraulic design of MD Series pumps is consistent across the entire range and reduced impeller ...
اقرأ أكثر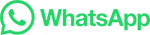
Grinding in Ball Mills: Modeling and Process Control
The design of a ball mill can vary significantly depending on the size, the . ... The simplest cases of open- and . closed-circuit systems are shown in Fig. 1. Fig. 1 .
اقرأ أكثر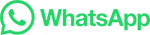
Orbis Machinery Ball Mills | Ball Mill Drive
Particle size reduction of materials in a ball mill with the presence of metallic balls or other media dates back to the late 1800's. The basic construction of a ball mill is a cylindrical container with journals at its axis. ... Our combined experience in ball mill design and process equipment development totals more than 60 years and allows ...
اقرأ أكثر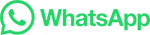
Material transport in ball mills: Effect of discharge-end design
In the case of the open-end mill in the absence of balls, the fractional volumetric material hold-up will be very small because there is no end constriction to hold material inside the mill and there is little BALL LOAD, PERCENT OF MILL VOLUME ZO 30 0 IO 14 Z w a a o o 12 I Q Q a CONSTRICTED-END MILL BO f OPEN-END z MILL a a ~ …
اقرأ أكثر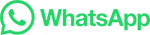
MODULE #5: FUNCTIONAL PERFOMANCE OF BALL …
The removal of the fine particles to make room for grind-ing more coarse particles in the ball mill. The overall efficiency of the ball mill circuit is therefore comprised of two efficiencies: that of the "ball mill grinding environment" and that of the "classification system". Note.
اقرأ أكثر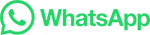
Grinding in Ball Mills: Modeling and Process …
PDF | The paper presents an overview of the current methodology and practice in modeling and control of the grinding process in industrial ball mills.... | Find, read and cite all the research...
اقرأ أكثر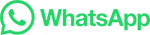
How to design a Ball Mill
You also need a rod mill work index to design a ball mill operating on a coarse feed, above about 4 mm. Q1: You design for a typical percentage of critical speed, usually 75% of …
اقرأ أكثر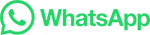