Simulation of wet ball milling of iron ore at Carajas, Brazil
The analysis by Cho and Austin of a series of tests on open circuit wet ball milling of phosphate ore led to an equivalent classification of (21) s i = 1 1 + (x 50 x i) 3.5. The controlling parameter is the particle sieve size x 50 at which 50% is returned to the mill feed and 50% exits the mill.
اقرأ أكثر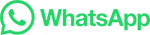
Closed and Open Circuits Ball Mill for Cement, Limestone, Iron ore
We bring forth a highly advanced Ball Mill, specifically engineered for both wet as well as dry cement grinding applications. Classified depending on the circuit design, bearing, grinding type and drive, the selection is made on the basis of the product fineness, quality, and nature of raw material, site conditions and specific requirements.
اقرأ أكثر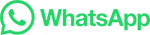
Ball Mills
CERAMIC LINED BALL MILL. Ball Mills can be supplied with either ceramic or rubber linings for wet or dry grinding, for continuous or batch type operation, in sizes from 15″ x 21″ to 8′ x 12′. High density ceramic linings of uniform hardness male possible thinner linings and greater and more effective grinding volume.
اقرأ أكثر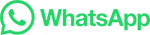
Ball Mill Design/Power Calculation
The work index will also have a considerable variation across one ore body or deposit. ... A wet grinding ball mill in closed circuit is to be fed 100 TPH of a material with a work index of 15 and a size distribution of 80% passing ¼ inch (6350 microns). The required product size distribution is to be 80% passing 100 mesh (149 microns).
اقرأ أكثر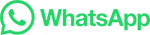
Unlock the Power of Mineral Wet Ball Mill: Enhancing Iron Ore
The mineral wet ball mill offers several potential benefits that can significantly enhance iron ore processing efficiency. Firstly, the controlled grinding process provided by wet ball mills ensures a more uniform and fine-grained product, which is crucial for downstream magnetic separation and flotation processes.
اقرأ أكثر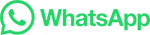
The Ultimate Guide to Ball Mills
• Edge driving ball mill: the motor drives the gear on the edge of the cylinder through the reducer to drive the cylinder movement. 6. According to the operation characteristics of ball mill: • Wet ball mill: Adding water when feeding, the discharging material is discharged when it is in a certain concentration of slurry. The wet ball mill ...
اقرأ أكثر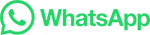
Grinding kinetics of quartz and chlorite in wet ball milling
For each grinding test, the mill was first loaded with a 1.86 kg mass of ball mix and a 150 g mass of feed sample material.A volume of 64.0 ml tap water was then added to the mill charge in order to make a 70 wt.% pulp density.Four mono-sized fractions of quartz and chlorite(− 2 + 1.19 mm, − 1.19 + 0.5 mm, − 0.5 + 0.25 mm, − 0.25 + 0.15 mm)were …
اقرأ أكثر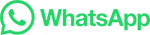
Wet Milling vs Dry Milling: The Differences, Advantages, and Challenges
Wet milling, also known as wet grinding, is a process through which particles that are suspended in a liquid slurry are dispersed in that liquid by shearing or crushing. Once the milling process is complete, these particles are ready for use or can be dried and separated for incorporation into additional products. Wet milling is more complex ...
اقرأ أكثر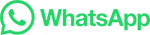
Copper Ore Crushing, Grinding & Flotation
Grinding and Flotation. Fine ore at minus 19mm (¾") sizing is fed at a controlled rate into the open-circuit 2600mm x 3960mm (8'-6 x 13'-0) Hardinge rod mill at an average feed rate of 2,106 STPD or 87.75 STRH. Rod mill discharge at a nominal size of minus 16 mesh and a pulp density of 75 percent solids combines with ball mill discharge ...
اقرأ أكثر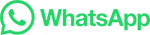
What Are the Differences Between Dry and Wet Ball Mills?
Advantages of wet ball mill: (1) The wet ball mill has better performance and higher grinding efficiency. It has low requirements for ore water content and can process ores with high water content and mud content. (2) The wet ball mill has less auxiliary equipment and simple material transportation device, so the investment is about …
اقرأ أكثر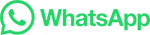
Wet Grinding Mill
Wet Grinding Mills is mainly used for separation of gold, silver, lead, zinc, molybdenum, iron, copper, antimony, tungsten, tin and other minerals selected. With less investment, fast results, small footprint saving power, sturdiness and durability, ease of maintenance and high return on investment. It is the preferred production for alternative ball mill, is ideal …
اقرأ أكثر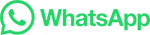
Ball Mill
Mechanical Crushing and Grinding. Oleg D. Neikov, in Handbook of Non-Ferrous Metal Powders (Second Edition), 2019 Tumbling Ball Mills. Tumbling ball mills or ball mills are most widely used in both wet and dry systems, in batch and continuous operations, and on small and large scales.. Grinding elements in ball mills travel at different velocities. …
اقرأ أكثر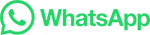
Rod Mill | SpringerLink
Ore discharge refers to the rod mill that the ore is discharged by the ore pulp itself. Unlike the overflow ball mill, which has no neck of hollow shaft at the discharge port, instead, it has a wide aperture trumpet overflow port in the center of discharge port (Fig. 1). In order to avoid pulp splashing and steel rod sliding out of the mill ...
اقرأ أكثر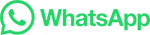
Mining Ore Wet Grinding Equipment Copper Ball Mill
Mining Ore Wet Grinding Equipment Copper Ball Mill. Production Capacity:0.65-615t/h Discharged Size:≤25mm Ball Loading Weight:1.5-338t Application: It can grind cement raw material and other materials in building material, metallurgical, electric and chemical industries. Send Inquiry
اقرأ أكثر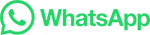
Population balance modeling approach to determining the mill …
It was found that the value of the mill diameter scale-up factor varied quite significantly with the breakage properties of the material, the size distribution of the particulate contents of the mill, the size of the desired product, and the mode of grinding (dry/wet). Therefore, ball mill scale-up models presently available need to be modified ...
اقرأ أكثر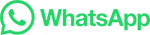
Wet Ball Mill for Metal Ores and Non-ferrous …
Buy wet ball mill from trusted wet grinding ball mill supplier. Energy saving wet ball mill, small energy consumption, large productivity, effectively improving grinding efficiency.
اقرأ أكثر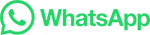
Simulation of wet ball milling of iron ore at Carajas, Brazil
The results of the analyses clearly shows that using a sieve of +180µm and its bottom -180µm, the best time for grinding 0.5kg of Itakpe iron ore with 3kg of grinding media and a mill speed of 92 rpm is 8 minutes, yielding 17.10% fines and 82.90% coarse., 0.8 mill critical speed measured 15.20% fines and 84.80% coarse.
اقرأ أكثر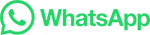
Ball Mill Price / Ore Ball Mill / Ball Mill Grinding Machine / Ball …
The same grinding a ton of ore, wet ball mill will saving 20%-30% energy than dry ball mill. 3. Investment in production costs. Nowadays, wet ball mill in the mining industry occupies a large proportion. Because it has the simple structure, and the price and costs lower than dry ball mill, it has the higher cost-effective. ...
اقرأ أكثر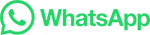
The Ultimate Guide to Ball Mills
• Edge driving ball mill: the motor drives the gear on the edge of the cylinder through the reducer to drive the cylinder movement. 6. According to the operation …
اقرأ أكثر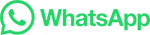
Ball Grinding Process | SpringerLink
Due to the difference of ore discharge modes between the two mills, the productivity of grate ball mill is 10%–25% higher than that of overflow ball mill. When two-stage grinding is required, the first stage uses grate ball mill and the second stage uses overflow ball mill. When regrinding of coarse concentrate is required, overflow ball mill ...
اقرأ أكثر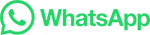
High Efficiency Mining Equipment Ore Wet Grinding Ball Mill
High Efficiency Mining Equipment Ore Wet Grinding Ball Mill HZE manufacture standard wet ball mills with high efficiency, low energy consumption, stability and reliability for grinding minerals of precious metals, base metals and non-metal. It can also be specially designed and customized according to the special requirements of the customers.
اقرأ أكثر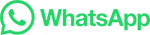
Wet Grinding VS Dry Ball Mill Grinding
The ore charge in the tests shown in table 18 would probably be small because the mill, which was 19 inches in diameter, had an 8-inch discharge. Wet grinding gave 39 percent, more capacity and 26 percent …
اقرأ أكثر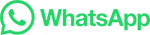
Wet Ball Mill for Metal Ores and Non-ferrous Metals Wet Milling
Wet Ball Mill. Feeding size: ≤25mm. Capacity: 0.65-615t/h. Motor power: 18.5-4500kW. Applications: It can deal with metal and non-metal ores, including gold, silver, copper, phosphate, iron, etc. The ore that needs to be separated and the material that will not affect the quality of the final product when encountering water.
اقرأ أكثر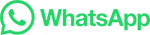
Wet Ball Mills
China Wet Ball Mills wholesale - Select 2024 high quality Wet Ball Mills products in best price from certified Chinese Ball Machine manufacturers, Metal Ball suppliers, wholesalers and factory on Made-in-China ... Gold Copper Ore Wet Ball Mill, Limestone Powder Rotary Dry Ball Mills Machine Price US$ 82000-98000 / Set. 1 Set (MOQ) Baichy ...
اقرأ أكثر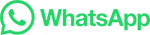
Wet ball mills
26 rowsProduct Details. Wet ball mills. Ball mill is widely used in mining, smelting,road,building material and chemical. It is the key equipment for grinding after the crush process.The mill consists of feeding device, …
اقرأ أكثر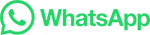
Replacement of Wet Ball Milling with High-Pressure Grinding …
As a result of this study, the many questions regarding the possible application of high-pressure grinding in the current role of wet ball milling have been …
اقرأ أكثر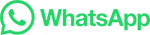
Small Ball Mill
In general, ball mills can be operated either wet or dry and are capable of producing products on the order of 100 um. This duty represents reduction ratios as great as 100. The ball mill, an intermediate and fine-grinding device, is …
اقرأ أكثر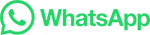
Dry ball milling and wet ball milling for fabricating copper–yttria
Yttria-reinforced copper matrix composites were prepared by dry ball milling (DBM) and wet ball milling (WBM), respectively, followed by spark plasma sintering (SPS). It is to determine which milling process is better for fabricating Cu–Y2O3 composites. It is found that Cu–Y2O3 composites synthesized by DBM exhibit better densification, …
اقرأ أكثر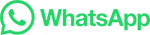
Wet grindability of an industrial ore and its breakage …
The wet grindability of a diasporic ore was studied in a laboratory ball mill. The medium particles fit the first-order breakage and the coarse ones do not. It is most likely due to the heterogeneity of the minerals in the ore, where silicate minerals break faster than the diaspore mineral and produce more fine particles with very low ratio of ...
اقرأ أكثر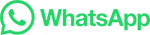
Friction and wear of liner and grinding ball in iron ore ball mill
Abstract. To understand the friction and wear of working mediums in iron ore ball mills, experiments were conducted using the ball cratering method under dry and wet milling conditions, which mimic the operating conditions in ball mills. The liner sample is made of Mn16 steel, the ball had a diameter of 25 mm and was made of GCr15 steel, …
اقرأ أكثر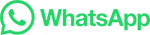