Key factors in setting up a cement plant
Setting up a cement plant is both time and capital intensive; it could take anywhere between five to seven years from concept to commissioning and an investment of around to Rs 1,800-2,000 crore for a typical integrated plant of 3 million tpa cement capacity. Size of a cement plant could vary from 0.2 million tpa to 5.0 million tpa.
اقرأ أكثر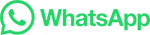
Work Procedure for Cement Concrete Works For Mixes …
2. Proportioning of Cement Concrete. The proportions selected for cement concrete are as per the design and strength requirements. The proportion can be 1:2:4 (M15 concrete) or 1:1.5:3 for M20 concrete. The proportion of 1:2:4 concrete denotes the ratio of cement: sand: coarse aggregates by volume unless specified.
اقرأ أكثر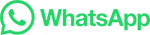
Cement Concrete Road Construction Procedure | Concrete Pavements
Batching plant: cc concrete; The batching plant is a mechanical equipment for measuring, either by weight or by volume, the quantities of different ingredients required to make up each complete charge of a concrete mixer. The types of batching plant in which the quantities of construction materials are measured by weight is called a weigh …
اقرأ أكثر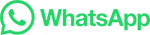
U.S. cement industry
Lehigh Hanson had 19 cement production plants in the U.S. as of 2021, making it the leading cement company in the U.S. based on the number of plants. This text provides general information.
اقرأ أكثر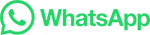
Cement: Applications, Manufacturing Process, Types and Tests
Coloured Cement. Manufacturers make this cement by combining 5- 10% mineral colours with conventional cement. It is commonly used for floor decoration. Air entraining Cement . Manufacturers make this cement by grinding clinker with indigenous air-entraining substances such as glues, resins, sodium salts of sulphates, and so on.
اقرأ أكثر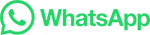
How Cement is Made
Stage of Cement Manufacture. There are six main stages of the cement manufacturing process. Stage 1: Raw Material Extraction/Quarry The raw cement ingredients needed for cement production are limestone (calcium), sand and clay (silicon, aluminum, iron), shale, fly ash, mill … See more
اقرأ أكثر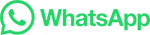
Standard Operating Procedure (SOP) 17--Concrete
This Standard Operating Procedure provides guidelines to establish Qualified Products for use with miscellaneous construction items and governs the following Qualified Products Lists which are included in this manual: QPL 13. Air Entraining Admixtures. QPL 14. Chemical Admixtures for Concrete. QPL 16. Membrane Curing Compounds. QPL 17.
اقرأ أكثر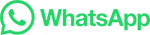
Concrete Batching Plant: Working & Components Explained …
A concrete batching plant is a facility that combines various ingredients to form concrete. These ingredients include aggregates, water, cement, and sometimes admixtures. The plant can be stationary or mobile, and it is used to produce concrete in large quantities. The batching plant has a high degree of automation, which allows for …
اقرأ أكثر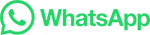
How Is Cement Produced in Cement Plants | Cement Making …
Cement plant laboratories check each step in the manufacture of portland cement by frequent chemical and physical tests. The labs also analyze and test the finished product to ensure that it complies with all industry …
اقرأ أكثر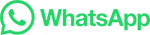
The Cement Plant Operations Handbook
addressing critial topics such as maintenance and plant reporting, alongside a detailed appendix with essential process calculations. Contents Section A – Process summaries 1. Introduction 10 1. The basics of cement manufacture – 2. History of cement manufacture – 3. Portland cement in today's world 2. Raw materials management system ...
اقرأ أكثر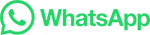
The Cement Manufacturing Process
How cement is made. Cement manufacturing is a complex process that begins with mining and then grinding raw materials that include limestone and clay, to a …
اقرأ أكثر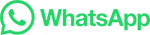
Cement Manufacturing and Process Control | SpringerLink
The energy requirement to produce cement in dry route is approximately half of the energy required to produce it through the wet process . The most common way to manufacture Portland cement is through a dry process . The first step is to quarry the principal raw materials, mainly limestone, clay, and other materials.
اقرأ أكثر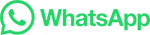
Concrete Plant
The concrete plants of the precast companies are fully automatic and can produce simultaneously between 1 and 5 m 3 of SCC in the same mixer machine. The facilities are huge, as can be seen in Fig. 15.7, unlike the concrete mixers traditionally used in construction sites, with a maximum capacity of 0.1–0.2 m 3 .
اقرأ أكثر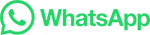
Types of Ready Mix Concrete Plants and their Mixing Actions
Concrete that are produced as per established procedures in batching plants and after that delivered to construction site by truck on which transit mixture is mounted is called ready mix concrete. In this article, various types of ready mix plant, which are categorized based on the type of mixer, is described.
اقرأ أكثر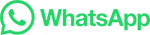
How Is Cement Made? Step-by-Step Guide
Keep reading for a step-by-step guide to how cement is made and a sneak peek at the future of cement. Table of Contents. Step 1: Extracting Raw Materials. Step 2: Creating Raw Meal. Step 3: Producing Clinker. Step 4: Grinding and Preparing the Cement. Step 5: Packaging, Storing and Transporting. The Future of the Cement Industry.
اقرأ أكثر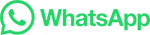
Concrete Mix Design Calculation
Estimated water content = 186+ (3/100) x 186 = 191.6 kg /m 3 Step 4 — Selection of Cement Content Water-cement ratio = 0.5 Corrected water content = 191.6 kg /m 3 Cement content = From Table 5 of IS 456, Minimum cement Content for mild exposure condition = 300 kg/m 3 383.2 kg/m 3 > 300 kg/m 3, hence, OK.This value is to be checked for …
اقرأ أكثر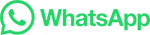
(Video) How Cement Is Made
How Cement is Made (Video) 1. Mining the raw material. Limestone and clay are blasted from rock quarries by boring the rock and setting off explosives with a negligible impact of …
اقرأ أكثر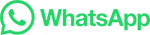
White cement manufacturing process
White cement manufacturing process. White cement is a type of special cement, belongs to decoration cement.In general, Portland cement is greyish-green, as the name suggested, white cement is white. In the cement manufacturing process, in order to avoid the mixing of colored impurities, calcination of white cement plant mostly use natural gas …
اقرأ أكثر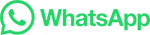
Functions of concrete batching plants and its different types
18651. Concrete batching plant. A concrete batching plant is used to mix various materials, such as cement, aggregates (sand, gravel, or crushed stone), and additives, to produce concrete. The mixing process occurs at the plant, where these components are combined in predetermined proportions to achieve the desired concrete …
اقرأ أكثر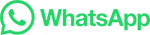
Concrete Construction
Concrete is the material of choice for driveways, sidewalks, patios, steps, and for garages, basements, and industrial floors. It is relatively inexpensive to install and provides an attractive, durable surface that is easy to maintain. Proper attention to the standard practices and procedures for constructing exterior or interior concrete can ...
اقرأ أكثر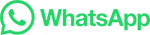
Masonry Cement Manufacturing | How To Make Masonry Cement?
Masonry cement is made by adding a large amount of active or inactive mixed materials and slaking lime into Portland cement. This cement has better workability and water retention but lower strength. It can also be made from an active mixture of materials such as fly ash and lime or gypsum. The grade of masonry cement includes 225, 275, 325, etc.
اقرأ أكثر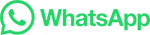
PERFORMING A CEMENT PLANT OPERATIONS AUDIT
A typical audit may include the following steps: Discuss purpose and objective of the operation audit with top management. Develop a work plan for the audit and create a project team, as required. Determine major data sources and list of key parameters. Review detailed plan and data sources with top management.
اقرأ أكثر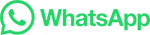
crusher/sbm procedure to produce cement in a cement plant…
You've already forked crusher 0 Code Issues Pull Requests Packages Projects Releases Wiki Activity
اقرأ أكثر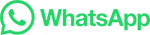
CO2 Capture in Cement Production and Re-use: First Step …
Carbon Capture and Utilization (CCU) is one of the most widely studied technology to reduce anthropogenic CO 2 emissions and particularly the ones coming from power plants and cement plants which are currently among the world's main industrial sources of carbon dioxide. As a result, this study focuses on the optimization of an overall …
اقرأ أكثر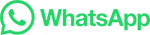
Plain Cement Concrete (PCC)- Work Procedure
Plain cement concrete (PCC) is a fundamental component of building construction, serving to prevent direct contact between reinforcement concrete and soil or water. This article delves into the intricacies of laying PCC, offering insights into the materials used, the procedure, dos and don'ts, and the advantages it brings to construction projects.
اقرأ أكثر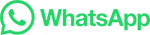
Cement Plant: The Manufacturing Process 4 5
Cement Plant: The Manufacturing Process worldcementassociation 1 Limestone (CaCO3) is taken from a quarry 2 4 3 The limestone is fed into a crusher and then stored …
اقرأ أكثر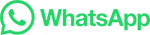
(Video) How Cement Is Made
How Cement is Made (Video) 1. Mining the raw material. Limestone and clay are blasted from rock quarries by boring the rock and setting off explosives with a negligible impact of the environment, due to the modern technology employed. 2. Transporting the raw material.
اقرأ أكثر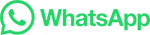
Raw mill
cement ball mill. Application: limestone, clay, coal, feldspar, calcite, talc, iron ore, copper, phosphate, graphite, quartz, slag. Capacity: 0.65-615T/H. The cement ball mill usually can be applied to raw meal grinding or cement grinding. Besides, the cement ball mill also can be used for metallurgical, chemical, electric power, other mining ...
اقرأ أكثر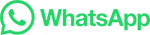
Cement Making Process
To produce one ton of cement clinker, it needs to consume 1.58 to 1.621 tons of raw materials, 0.10-0.12 tons of coal, and emit about 1 ton of carbon dioxide. Therefore, the energy saving and consumption reduction in the clinker calcination process is crucial for the whole cement production line. The above is the thermal performance test data ...
اقرأ أكثر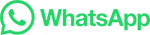
Soil-Cement
the minimum cement content required to produce the desired SC product in terms of UCS and durability requirements, ... subbase, or embankment. Compaction and curing procedures are the same for central-plant and mixed-in-place procedures. In SC construction the objective is to obtain a thoroughly mixed, adequately compacted, and …
اقرأ أكثر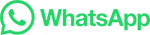