Coal for cement: Present and future trends
ResultThe top 10 coal consuming countries consumed 4.81Bnt of coal during the year, or 86.8% of global consumption volumes. Eight of the top 10 coal consuming countries reported declining year-on-year coal consumption in 2014. However, India's coal consumption grew by 12.1% to 551Mt and South Korea's …
اقرأ أكثر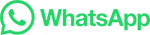
Investigation of co-milling Utah bituminous coal with …
ResultThe grinding energy in each case was calculated based on the mass flow rates of the fuel introduced into the mill and the mill power consumption. Table 3 contains the results, where the R ratio of the grinding energies is also listed for better comparison. If the value of R = 1, the mill is expected to utilize the same …
اقرأ أكثر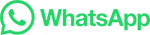
Study on micro-energy consumption model of ultrafine grinding coal
ResultFuel. Volume 329, 1 December 2022, 125542. ... By extending its energy consumption law and mechanical behavior to particle groups, a grinding model of the whole particle system can be established [7]. ... A stirring ball mill (QM-5, FOCUCY, China) was used to treat the coal samples by controlling the grinding …
اقرأ أكثر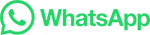
Benchmarking energy use in the paper industry: a
ResultThe production of paper and board is an energy intensive process. With an energy use of 6.4 EJ in 2005, the pulp and paper industry was responsible for about 6 % of the world's total industrial energy consumption (International Energy Agency (IEA) 2008), being the fourth largest industrial energy user …
اقرأ أكثر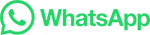
Energy efficiency challenges in pulp and paper …
ResultAbstract. The pulp and paper industry is highly energy-intensive. In mills that use chemical pulping, roughly half of the higher heating value of the cellulosic material used to manufacture the product typically is incinerated to generate steam and electricity that is needed to run the processes. Additional energy, much of it non …
اقرأ أكثر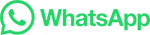
Reducing energy consumption of a raw mill in cement industry
ResultIn this study, the first and second law analysis of a raw mill is performed and certain measures are implemented in an existing raw mill in a cement factory in order to reduce the amount of energy consumption in grinding process. The first and second law efficiencies of the raw mill are determined to be 61.5% …
اقرأ أكثر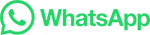
Modeling of energy consumption factors for an industrial
ResultAs one of the most energy-intensive industries, cement plants consume around 100 kWh of electrical energy for each ton of their production. This can be counted yearly as over 6% of global energy ...
اقرأ أكثر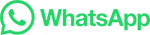
MINING ENERGY CONSUMPTION 2021
ResultComminution, consuming close to 40% of total energy contains a single piece of equipment—the grinding mill—that is typically the largest single consumer in a mining operation. ... From the breakdown of energy consumption, it was found that comminution accounts for 25% of final energy consumption of an "average" mine …
اقرأ أكثر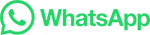
Mill Inerting Systems Presentation to the ASBCUG
ResultMost utility boiler coal mills do and should operate at primary air to coal ratios of 2:1 or less. Coal Mill Air to fuel ratios are higher during: Start-up. Shutdown. Interruptions in raw coal feed. Lower feeder speeds. This occurs because a minimum airflow through the coal mill must be maintained to insure that burner line …
اقرأ أكثر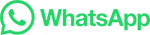
Energy use in paper mills affects carbon footprint
ResultEnergy is a factor behind our low carbon footprint. Electricity consumption, energy-efficiency, and energy production - these topics are top of mind in every paper mill today. And we are better off than most. Paper production is energy intensive. Saving energy is a challenge that we share with all the world's industries, as energy is …
اقرأ أكثر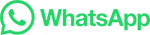
A unified thermo-mechanical model for coal mill operation
ResultCoal mills are bottleneck in coal–fired power generation process due to difficulty in developing efficient controls and faults occurring inside the mills. In …
اقرأ أكثر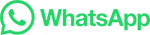
Milling energy consumption of hammer mill for different …
ResultTable 2 is a summary of the milling energy consumptions of hammer mill for four biomasses with different moisture contents [31]. Considering the energy consumption and fuel size together, milling ...
اقرأ أكثر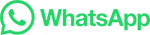
Investigation of co-milling Utah bituminous coal with …
ResultSteam explosion. Bituminous coal. 1. Introduction. Co-firing beetle kill wood, or any dead woody biomass in coal-fired boilers is an attractive method for …
اقرأ أكثر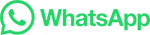
2018 Manufacturing Energy Consumption Survey
ResultManufacturers have two types of energy consumption—fuel and nonfuel. Fuel consumption is the use of any substance that can be burned to produce heat and power or to generate electricity. ... production in the pulping process to make paper and the subs equent use of the produced black liquor as a fuel at pulp and paper …
اقرأ أكثر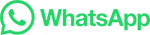
Wood and wood waste
ResultIn 2022, wood energy accounted for about 4.0% of residential sector end-use energy consumption and 2.5% of total residential energy consumption. In 2020, 8.9% of all U.S s (about 11 million) used wood for energy (mostly for space heating). About 2.2 million s used wood as the main space-heating fuel. 3
اقرأ أكثر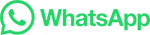
Consumption – Coal Information: Overview – Analysis
ResultGlobal coal consumption decreased by 3.1% in 2020. The US experienced the largest year-on-year change, -72 Mtce, followed by the EU and India, -45 and -30 …
اقرأ أكثر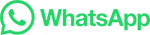
Optimisation of coal fineness in pulverised-fuel boilers
ResultOn-line measurement of pulverized coal fineness on a 300 MWe power plant with pulsed digital inline holography. ... Biomass is pulverized to fineness of less than 250 μm and coal to 90% passing ...
اقرأ أكثر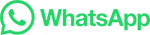
Fact sheet Energy use in the steel industry
Resultreductions of about 60% in energy required to produce a tonne of crude steel since 1960, as demonstrated in Figure 1.1 Figure 1: Indexed global energy consumption/tonne of crude steel production worldsteel, with the help of its members, has developed a comprehensive and process specific energy …
اقرأ أكثر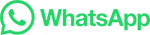
Energy Efficiency Intervention in the Rolling Mill Cluster …
ResultDistribution of rolling units between Bhavnagar and Sihor. Range of operation (production, TPM) 45 TPM – 1500 TPM Average production 534 TPM Average Coal Consumption 60 TPM Average Electricity Consumption 93 MWh / month 0.71 MkCal/ tonne Average Specific Energy Consumption 0.07 Mtoe / tonne. …
اقرأ أكثر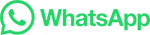
Power consumption of cement manufacturing plant
ResultAt present, the average level of unit energy consumption of Cement Manufacturing Plants is at 33 kWh, in some Cement Manufacturing Plants, it could be 40 kWh higher than the average number. Through technology improvement, equipment update, and new type abrasion materials, the Cement Manufacturing …
اقرأ أكثر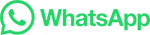
Milling Characteristics of Coal and Torrefied Biomass Blends …
ResultIntroduction. Replacing some of the coal by biomass is an effective way to reduce CO 2 emissions from pulverized-coal-fired power plants and integrated coal gasification-combined cycle power plants. However, compared with coal, biomass has lower grindability in the existing roller mills 1 and a lower …
اقرأ أكثر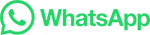
Use of coal
ResultBasics. +Menu. In 2022, about 513 million short tons (MMst) of coal were consumed in the United States. On an energy content basis, this was equal to about 9.8% of total U.S. energy consumption in 2022, or 9.85 quadrillion British thermal units, and the lowest percentage share since at least 1949. Although coal use was once …
اقرأ أكثر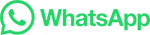
Derivation and validation of a coal mill model for control
ResultCoal fired power plants are heavily used due to large and long lasting coal resources compared with oil or natural gas. An important bottleneck in the operation of this particular kind of plants, however, is the coal pulverization process, which gives rise to slow take-up rates and frequent plant shut-downs (Rees & Fan, …
اقرأ أكثر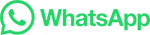
Milling Characteristics of Coal and Torrefied Biomass Blends …
ResultThe power consumption and differential pressure of the mill measured during milling the coal–TP blends were higher than when using coal …
اقرأ أكثر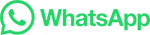
A Hallmark of Energy Efficient Operations
ResultEnergy efficiency in a cement plant is measured as a combination of two factors, viz., Thermal Energy Consumption and (2) Electrical Energy Consumption. The former specifically measures the kiln performance while the latter measures the overall performance of the plant. ... Coal Mill - Vertical Roller Mill: …
اقرأ أكثر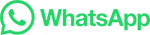
Top 4 Energy Consumers in the Paper Manufacturing Industry
ResultPower House boilers generally use coal, wood waste, black liquor, oil, natural gas, or a combination of fuels. The type of fuel used depends on the size of the mill and whether there's a pulping operation on site. Many mills have multiple different kinds of boilers on site and most include steam turbines to generate …
اقرأ أكثر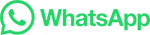
Energy consumption characteristics of turn-mill machining
ResultReducing the energy consumption of manufacturing processes and machine tools can considerably affect the environmental and economic impact of industrial activities. Since the 2008 global financial crisis, many scholars have focused on modeling the energy consumption of basic machining processes …
اقرأ أكثر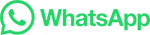
Performance of Coal Based Thermal Power Plant at Full …
ResultThe total moisture in the coal is 8% as against design value of 6.17% at full load and the total moisture in the coal is 12.5% as against design value of 7.5% at part load. Hydrogen content is slightly deviating from design value. This loss could be reduced by reducing moisture content in the coal as follows.
اقرأ أكثر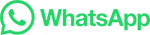
cement plant calculations kiln, mills, quality, combustion, …
ResultStandard coal factor SCF Specific Stoichiometric/minimum Combustion Air SSCA kg-air/kg-fuel ... Critical Speed (nc) & Mill Speed (n) Degree of Filling (%DF) Maximum ball size (MBS) Arm of gravity (a) Net Power Consumption (Pn) Gross Power Consumption (Pg) Go To Online Calculators.
اقرأ أكثر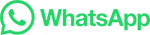