Copper Ore Crushing, Grinding & Flotation
Grinding and Flotation. Fine ore at minus 19mm (¾") sizing is fed at a controlled rate into the open-circuit 2600mm x 3960mm (8'-6 x 13'-0) Hardinge rod mill at an average feed rate of 2,106 STPD or 87.75 STRH. Rod mill discharge at a nominal size of minus 16 mesh and a pulp density of 75 percent solids combines with ball mill discharge ...
اقرأ أكثر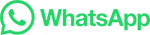
Simple Ore Crusher
This mod add three new blocks which double, triple and quintuple your ores respectively. Ore Crusher MK1: will double your iron and gold by crushing it into dust from which you smelt. Ore Crusher MK2: will triple your ores of iron and gold. unlocks the ability to crush ancient debris into 2 Netherite dust which smelts into 2 ingots of Netherite.
اقرأ أكثر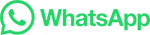
Common Iron Ore Crushing and Screening Process – …
When dealing with argillaceous iron ore with high water content, or when restricted by terrain conditions, a three-stage open-circuit crushing and rod mill …
اقرأ أكثر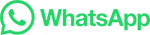
The application of high voltage pulses in the mineral …
This study magnetization roasts hematite ore after mechanical crushing and HVPD, analyzing the difference in the roasting effect between the two crushing methods by establishing a new system of HVPD-magnetization roasting. For a roasting temperature of 500 °C, roasting time of 30 min and number of pulses of 100 times, the grade and …
اقرأ أكثر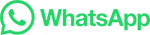
The six main steps of iron ore processing
Six steps to process iron ore. 1. Screening. We recommend that you begin by screening the iron ore to separate fine particles below the crusher's CSS before the crushing stage. A static screen is used to divert the fine particles for crushing. This step prevents overloading the crusher and increases its efficiency.
اقرأ أكثر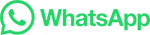
8.2: Mining and Ore Processing
Figure 8.2.1 Simplified Schematic of an Underground Mine. A shaft is a vertical mine opening, a level is horizontal and a decline is sloped so as to allow passage …
اقرأ أكثر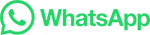
Crushing in Mineral Processing
In mineral processing or metallurgy, the first stage of comminution is crushing. Depending of the type of rock ( geometallurgy) to be crushed, there are 2 largely different techniques at your disposition for crushing rocks. In principle, compression …
اقرأ أكثر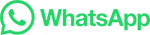
Gyratory Crusher (Gyratory Crushers Explained)
The process of reducing mined ore for processing is known as 'comminution', which is defined as 'the action of reducing a material, especially a mineral ore, to minute particles or fragments'; this is normally achieved at mining operations through one or more stages of crushing and milling.. Early mining activities were labour intensive. Ore breakdown …
اقرأ أكثر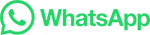
Study on Impact Crushing Characteristics of Minerals Based …
The crushing operation of ores is widely used in solid mineral resource processing fields such as mining, the chemical industry, metallurgy, building materials, thermal power, etc. [1,2,3].The crushing process of ore plays a very important role in mineral processing production, with its infrastructure costs accounting for about 60% of …
اقرأ أكثر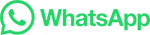
What Type of Crusher Is Best for Primary Crushing?
The right one for a primary crushing application depends on the material to be crushed, the feed size, the desired product size and the capacity required. Primary …
اقرأ أكثر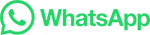
Crushing Plant Design and Layout Considerations
Good geotechnical information is essential to crushing plant siting and design. Installing a primary crushing plant on solid rock reduces the cost of concrete and structural steel. Life of Mine/Expansion Plans The life of the mine is a key element in the design of any crushing plant. Short-term mine lives
اقرأ أكثر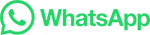
AMIT 135: Lesson 5 Crushing – Mining Mill Operator Training
The purpose of the primary crusher is to reduce the ROM ore to a size amenable for feeding the secondary crusher or the SAG mill grinding circuit. The ratio of reduction through a primary crusher can be up to about 8:1. Feed: ROM up to 1.5 m. Product: -300mm (for transport) to -200mm (for SAG mill) Feed Rate:
اقرأ أكثر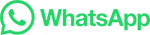
Reduction of Fragment Size from Mining to Mineral …
2.1 Energy. Rock drilling, blasting, and comminution (crushing and grinding) consume a vast amount of energy in hard rock mines. As mentioned in Sect. 1, statistics from hard rock mines indicates that drilling and blasting consumes 2% and comminution does 53% of the total energy input in the whole production chain from mining to mineral …
اقرأ أكثر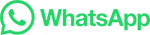
What Type of Crusher Is Best for Primary Crushing?
The right one for a primary crushing application depends on the material to be crushed, the feed size, the desired product size and the capacity required. Primary crushers reduce large run-of-mine material, such as rocks and ore lumps, into smaller sizes for further processing downstream, whether that be transport to additional crushers or to …
اقرأ أكثر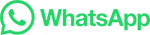
Coal Crusher
Mining Ore Crushing Equipment Expert. Henan Province, China Zhengzhou West Industrial Zone,451200 +86 1830843555 sales@moledive Mon - Fri: 9:00 - 17:30 ... Jaw Crusher: Known for its ease of use and high reduction ratios, jaw crushers are perfect for first crushing coal. They work well at reducing the size of big coal lumps into smaller ones.
اقرأ أكثر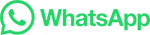
Crushing characteristics and performance evaluation of iron …
1. Introduction. Due to the decreasing reserves of high-grade iron ore and secondary resources used for steelmaking, it has become an important research and …
اقرأ أكثر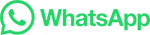
Solved Four years ago an ore-crushing unit was installed at
Economics questions and answers. Four years ago an ore-crushing unit was installed at a mine which cost P81,000. Annual operating costs for this unit are P3,540. This unit was estimated to have a life of 10 years. The quantity of ore to be handled is to be doubled and is expected to continue at this higher rate for at least 10 years.
اقرأ أكثر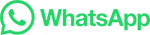
Crushing and Screening for Ore Sorting Success
When looking at overall crushing circuit design, having the correct number of crushing stages also helps minimize fines production. A typical crushing circuit will generate a reduction ration between 5:1 and 7:1 for maximum efficiency. For example, to generate a 10mm particle, you'll want to feed the crusher particles between 50 and 70mm.
اقرأ أكثر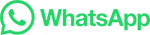
Crushing and Screening for Ore Sorting Success
When looking at overall crushing circuit design, having the correct number of crushing stages also helps minimize fines production. A typical crushing circuit will generate a reduction ration between 5:1 and 7:1 for maximum …
اقرأ أكثر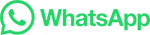
Study on Magnetite Ore Crushing Assisted by Microwave Irradiation …
High energy consumption in ore crushing brings great challenges to the mining industry. Microwave irradiation provides a promising solution for rock breaking. However, there is currently a lack of detailed understanding of the microwave parameters regarding magnetite ore. The purpose of this study is to fully understand the potential …
اقرأ أكثر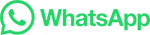
Measurement-Control for Crushing and Screening Process
It mainly includes crushing process control, crushing appliance fault diagnosis, and automatic distributing control. Crushing Process Control. To ensure the …
اقرأ أكثر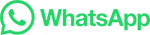
Aggregate Crushers, for Rock, Ore & Minerals
The portable units perform well in crushing aggregates, minerals, and ores, while the Holmes crushers are designed for crushing coal and coke. Marcy® Double Roll Crushers are used in intermediate size reduction of medium hard to hard materials such as rock or ore and can bridge the gap between laboratory and production outputs. Models with 3 ...
اقرأ أكثر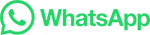
Forces in a Cone Crusher | Steel in Translation
The crushing of minerals and ore is of great industrial importance. With global population growth, urbanization, and continuing improvements in living conditions, the productivity and efficiency of existing crushers must be increased to meet the growing demand [].Cone crushers are characterized by a continuous operating cycle and may …
اقرأ أكثر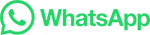
Crushing characteristics and performance evaluation of iron ore …
1. Introduction. Due to the decreasing reserves of high-grade iron ore and secondary resources used for steelmaking, it has become an important research and development area to improve the grade of iron ore through crushing (Gul et al., 2014).The quality of iron ore crushing directly affects the performance of pellets and sinter, so as to …
اقرأ أكثر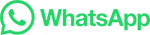
Study on Magnetite Ore Crushing Assisted by Microwave …
The purpose of this study is to fully understand the potential value of microwave irradiation applied in auxiliary crushing of magnetite ore. It is typically found that increasing power reduces ...
اقرأ أكثر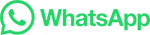
Hard Rock Mining Equipment | Crushing Plants
Ore feeding, Crushing (Coarse and Fine), Grinding (or milling), Sizing (screening and classification) and Concentration (separation and recovery) are the three most important steps that are involved in ore processing by …
اقرأ أكثر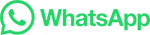
Crushing and Screening for Ore Sorting Success
2. Choke-feed the crusher for maximize uptime and operator safety. 3. Select a double deck vibrating screen with enough screen area to remove fine particles before they get to the sorter. For more advice and tips like these, feel free to reach out to our mineral processing equipment experts, and we'll be happy to help you and your sorting ...
اقرأ أكثر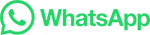
Solved In crushing a certain ore, the feed is such 80% is
Chemical Engineering questions and answers. In crushing a certain ore, the feed is such 80% is less than 50.8 mm in size and the product size is such that 80% is less than 6.35 mm. The power required is 89.5 kW. The power required using the same feed so that 80% is less than 3.18 mm is roughly around . Assume that Bond's Law applies.
اقرأ أكثر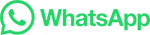
Crusher (Mekanism)
The Crusher is a machine added by Mekanism and grinds solid materials into dusts. However, it does not double ores. It is used primarily for two tasks: producing Bio Fuel and being an important part of the tier 2, 3 and 4 ore-processing system (see below). The Crusher is also used as a component in crafting the Basic Crushing Factory and its ...
اقرأ أكثر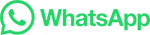
Winning the Metal: Ore Mills of the West
The earliest, and simplest method of crushing ore was the use of arrastras. When enough capital was available, stamp mills replaced arrastras at most mines. The following sections take a look at various types of stamp mills, the most common milling facilities at mines of the frontier West. The Trench mill at Silver City, Nevada 1877.
اقرأ أكثر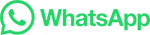