A Review of the Grinding Media in Ball Mills for Mineral …
The ball mill is a rotating cylindrical vessel with grinding media inside, which is responsible for breaking the ore particles. Grinding media play an important role in the comminution of mineral ores in these mills. This work reviews the application of balls in mineral processing as a function of the materials used to manufacture them and the …
اقرأ أكثر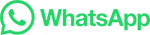
Ball Milling
Ball milling is a mechanical technique that is broadly used to grind powders into fine particles [134–141]. The reactants are generally broken apart using solvent molecules in the traditional method; but in ball milling, reactants are broken by using mechanical forces. The term mechanochemistry has been introduced very recently [142].
اقرأ أكثر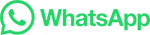
Dry ball milling and wet ball milling for fabricating copper–yttria
Yttria-reinforced copper matrix composites were prepared by dry ball milling (DBM) and wet ball milling (WBM), respectively, followed by spark plasma sintering (SPS). It is to determine which milling process is better for fabricating Cu–Y2O3 composites. It is found that Cu–Y2O3 composites synthesized by DBM exhibit better densification, …
اقرأ أكثر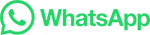
Wet Ball Mill for Metal Ores and Non-ferrous Metals Wet Milling
Wet Ball Mill. Feeding size: ≤25mm. Capacity: 0.65-615t/h. Motor power: 18.5-4500kW. Applications: It can deal with metal and non-metal ores, including gold, silver, copper, phosphate, iron, etc. The ore that needs to be separated and the material that will not affect the quality of the final product when encountering water.
اقرأ أكثر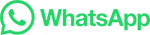
CERAMIC BALL MILL
3200×4600. 15. 13.5. 75. ceramic, silica, rubber, metal. Ceramic ball mill is also called ceramic ball mill machine. It is a kind of industrial ball mill that the liner plate is made of wear-resistant ceramics. AGICO manufactures automatic ceramic ball mills with low energy consumption.
اقرأ أكثر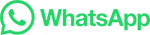
Ball milling
A ball mill is simply a container that is filled with pebbles (either of porcelain or stones e.g. Flint) into which a charge (powder or slurry) is put and that is then mechanically rotated to cause the tumbling pebbles to crush particles that happen between them. Ball mills can be continuous or periodic, they can be small or gigantic, low-speed ...
اقرأ أكثر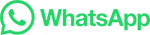
Orbis Machinery Ball Mills | Ball Mill Drive
Particle size reduction of materials in a ball mill with the presence of metallic balls or other media dates back to the late 1800's. The basic construction of a ball mill is a cylindrical container with journals at its axis. The cylinder is filled with grinding media (ceramic or metallic balls or rods), the product to be ground is added and ...
اقرأ أكثر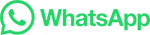
How to Choose the Right Types of Ball Mill for Your …
The horizontal design makes it easy to operate and maintain, and it is suitable for both wet and dry grinding. 2. Vertical Ball Mill. A vertical ball mill is a type of ball mill where the barrel is vertical instead of horizontal. It is designed for fine grinding of materials, and it is usually used in laboratory or small-scale production.
اقرأ أكثر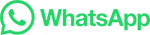
SPECIAL SECTION/MATERIALS HANDLING/POWDER …
Continuous ball mills are in use around the world, but they tend to be very large units suitable only for high-volume slurries and non-critical milling applications. …
اقرأ أكثر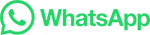
Ball Mills
Ball Mills. In ceramics, ball mills are used to grind down materials into very fine particles. Materials such as clay and glaze components can be broken down in a ball mill by getting placed into rotating or rolling jars …
اقرأ أكثر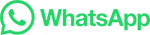
Ball Mills & Agitated Media Mills
Overview of our ball mills and agitated media mills. The classic ball mill Super Orion S.O. is suitable for dry hard crushing and achieves finenesses of under 10 µm. For superfine dry grinding: The energy-efficient Pulvis combines a vertical agitator bead mill with a high-performance classifier and is also suitable for grinding hard materials ...
اقرأ أكثر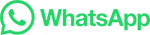
Modeling ball impact on the wet mill liners and its …
In China, metal magnetic mill liners have been widely used in wet ball mills to replace the traditional hard metal mill liners (Guo, 1996, Wu, 2002, Wang and Xiang, 2006, Su et al., 2006). The metal magnetic mill liners are made of ceramic magnets embedded in non-magnetic hard metal moldings.
اقرأ أكثر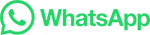
Minerals | Free Full-Text | A Comparison of the Fine-Grinding …
This study investigated the effect of grinding media on the fine-grinding performance in the wet tumbling mill. Comparative experiments between cylpebs and ceramic balls were conducted in a laboratory wet ball mill under various conditions, such as different total masses, total surface areas, and total numbers. The results indicated …
اقرأ أكثر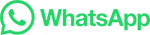
BALL MILL
Ball mill. Planetary ball mill is used for fine grinding of hard, soft, brittle and tough metallic, ceramic and composite materials. It can also be used for mixing and homogenization of powder mixtures. Milling can be performed in dry and wet conditions. Specifications. Disc speed 100 - 800 rpm; Final particle size < 1 µm
اقرأ أكثر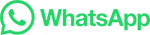
A Review of the Grinding Media in Ball Mills for Mineral …
The ball mill is a rotating cylindrical vessel with grinding media inside, which is responsible for breaking the ore particles. Grinding media play an important role in the …
اقرأ أكثر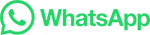
Which is better to use zirconium ball, steel ball, alumina …
At present, ceramic balls and alumina balls are mainly used for grinding in the market because of its low price. At least use zirconium balls, steel balls, and alumina grinding balls.This should be considered based on the properties of the materials, electricity costs, and grinding efficiency.
اقرأ أكثر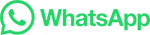
Wet Ball Mill 100 – 20000 litres | Baan Machines
Wet Ball Mill 100 – 20000 litres. Ball mills ( wet or dry processes) for intermittent grinding of hard materials and batches in different branches of the ceramic and chemical industry. To ensure iron-free grinding these mills are lined with steatite, Al2O3 or Polyurethane.
اقرأ أكثر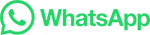
Effect of ball size and powder loading on the milling …
The ball mill process is very complicated process governed by many parameters, such as ball size, ball shape, ball filling, slurry loading (with respect to ball …
اقرأ أكثر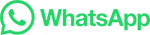
Effect of ball milling speed on the quality of Al2O3 stripped …
The combination of solid lubricant and hard ceramic materials makes the lubrication of soft particles and the strengthening of hard ... Haan, Germany). The powder after wet ball milling was dried in a vacuum drying oven (DZF-6050, Kebeter, Beijing, China). The surface morphology of the materials before and after ball milling was …
اقرأ أكثر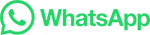
U. S. Stoneware: Ceramic Grinding Media
Grinding Media. High-density, ultra-high fired Burundum is the ideal medium for wet or dry milling. High specific gravity and cylindrical shape give it greater weight per volume, more contacts per mill revolution, greater area of attrition, with each contact. Result: faster, finer grinding or dispersion, often cutting milling time in half.
اقرأ أكثر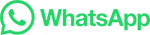
How can I determine the best RPM and balls to powder ratio for wet Ball
Suppose after weighing the solvent you get 100 gm (solvent), now you can divide by 3 i.e., 33.3 gm of powder, 33.3 gm of solvent and 33.3 gm of grinding media...If you feel the quantiy of grinding ...
اقرأ أكثر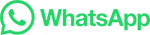
Wet ball milling of niobium by using ethanol, determination …
6 Citations. Metrics. Abstract. This study investigates the effect of using ethanol as the process control agent during the wet ball milling of niobium (Nb). Dried …
اقرأ أكثر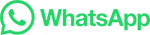
Ball Mill Grinding
Our ball mill grinding products apply the ancient principle of ball grinding to the industrial needs of the modern world. Many different industries can benefit from the grinding action that these mills offer: they are suitable for both dry and wet grinding as well as cryogenic grinding, and are commonly used for mixing or grinding chemicals, ores, paints and …
اقرأ أكثر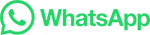
Modern Wet Milling and Material Processing | …
Traditional Wet Milling. The coatings industry is no different from others in its search for modern manufacturing techniques. The traditional high-speed dissolver, ball mill, vertical mill and standard horizontal mill have been the primary methods used to mill pigmented materials for more than 50 years, and are still considered to be the industry …
اقرأ أكثر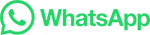
Choosing Your Ball Mill
NIDEC-SHIMPO's heavy-duty ball milling machines enable very precise milling in porcelain jars for relatively tough materials, wet or dry. Call us : 1-800-237-7079 . Mail us : info@shimpoceramics ... Ball mills have been used for decades to grind and mix materials used in the ceramic industry. NIDEC-SHIMPO's heavyduty ball milling ...
اقرأ أكثر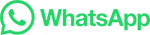
How to choose the size, filling amount and ratio of alumina ceramic …
The hardness of the high alumina ceramic ball is 9, and the density is 3.6. g/cm³, in the wet milling process, when the filling amount of the balls reaches 55% of the net volume of the ball mill, the best state can be achieved. The weight of the balls in the ball mill can be estimated with an empirical formula.
اقرأ أكثر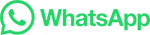
AMIT 135: Lesson 7 Ball Mills & Circuits – Mining Mill …
In ball mills, steel balls or hard pebbles to break particle based on impact and attrition. ... For soft ore, ceramic media (90 °/o A l 2 0 3) can be used (2200 kg/m 3). ... Wet Ball Mill = kg kWh = 0.16(A i-0.015) 0.33; Dry Ball Mill = kg / kWh = 0.023A i 0.5;
اقرأ أكثر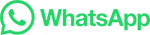
Effect of ball size and powder loading on the milling efficiency …
Shin et al. [25] investigated the effect of the ball size on the grinding efficiency in a laboratory-scale wet ball mill. Rhymer et al. [26] investigated the sliding friction coefficients and the ...
اقرأ أكثر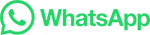
Ball mills and ceramic grinding balls // Umicore Ceramics
Ceramic ball mills are effective tools for attrition and crushing of fibrous or hard materials. They can be used to grind dry, wet and even cryogenically treated materials. They efficiently and quickly grind and homogenize volumes of products by impact and friction.
اقرأ أكثر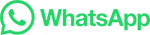