Everything you need to know about cement Materials Preparation and Raw
Although the mill was originally designated for cement production, the flex-ible layout allowed the grinding tests to be carried out for raw materials and coal as well. In an industrially operating Horomill, grinding takes place in a rotating shell (say, 3800 mm diam-eter in a given instance) at a rotation speed of 38 rpm actuated by a 2500 kW ...
اقرأ أكثر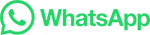
How it Works: Crushers, Grinding Mills and Pulverizers
Crushers, grinding mills and pulverizers are types of grinding equipment used to transform or reduce a coarse material such as stone, coal, or slag into a smaller, finer material. Grinding equipment can be classified into to two basic types, crushers and grinders. Industrial crushers are the first level of size reducer; further granularization ...
اقرأ أكثر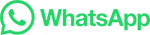
Raw mills for all requirements | Gebr. Pfeiffer
Pfeiffer. Applications. Cement raw material. Pfeiffer products for cement raw material preparation. Grinding, drying, and classifying in one machine. Depending on its deposit and composition, the cement raw material may …
اقرأ أكثر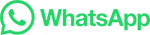
Reducing energy consumption of a raw mill in cement industry
Several grinding methods are available in cement industry depending upon the material to be ground. In cement production process, about 26% of the total electrical power is used in grinding the raw materials. During grinding process, the energy obtained from the rotary burner is consumed. In this study, the first and second law analysis of a …
اقرأ أكثر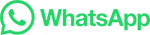
Raw Material Drying-Grinding
GRINDING MILLS. Mills will be selected according to type most suitable for required capacity and duty and for overall power consumption. From Process point of view …
اقرأ أكثر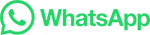
Raw Material Ball Mill
This ball mill is mainly used for grinding raw materials and final products in cement plant. It can be replaced by vertical raw mill. It is also suitable for grinding various ores and other materials in the metallurgy, mine, chemical, construction and other industries. Besides, the raw mill has two forms of milling, one is an open form, and the ...
اقرأ أكثر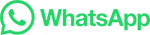
Vertical Raw Mill | Cement Raw Mill | Raw Mill In Cement …
Vertical raw mill is one kind of raw mill, generally used to grind bulk, granular, and powder raw materials into required cement raw meal in the cement manufacturing plant.Vertical raw mill is an ideal grinding mill that crushing, drying, grinding, grading transfer set in one. It can be widely used in cement, electric power, metallurgy, chemical industry, non …
اقرأ أكثر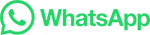
Vertical Roller Mill Operation in Cement Plant
The vertical roller mill (VRM) is a type of grinding machine for raw material processing and cement grinding in the cement manufacturing process.In recent years, the VRM cement mill has been equipped in more and more cement plants around the world because of its features like high energy efficiency, low pollutant generation, small floor area, etc.. …
اقرأ أكثر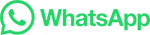
Raw material mill
Raw material ball mill, also called raw meal ball mill, is important grinding equipment in cement production process After being crushed, the raw meal enters the raw material mill The raw meal is grinded into fine powder by the motion and squeezing of steel balls The raw material mill manufactured by Great Wall Machinery can meet the raw material supply …
اقرأ أكثر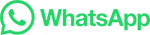
(PDF) DESIGN AND FABRICATION OF MINI BALL MILL
Ball mill is a cylindrical device that used to grind and blend raw materials and it rotates around a horizontal axis, partially filled with the material to be ground plus the grinding medium.
اقرأ أكثر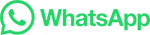
Solids | Choose the Right Grinding Mill
Attrition mills can operate in either batch or continuous mode and suit harder-to-grind material such as metal powders, metal carbides and glass frits. Their shaft speed runs from 75–500 rpm and media generally range in size from 5–13 mm. Feed material can be as coarse as 1/2 in., while end product size can be as fine as 2–3 …
اقرأ أكثر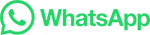
ThyssenKrupp Industrial Solutions
The DOROL® roller mill is equipped with two roller pair units. Designed to suit the specific requirements of each respective application it ensures the economical, reliable and energy-efficient grinding of: hard coal, lignite, coke and sewage slurry. raw materials for the cement manufacturing process. clay, limestone, burnt lime, raw phosphate.
اقرأ أكثر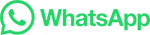
Raw Material Preparation in Cement …
At present, the most commonly used raw material preparation technologies are tube mill grinding system, vertical mill grinding system and roller mill grinding system. The energy consumption of tube mill system is …
اقرأ أكثر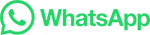
Shrimp feeds depend on proper ingredient grinding
Typically, the point where additional grind size attention becomes critical is when making 1.5mm or smaller diameter feeds and down to 0.8 mm. At this point, most feed manufacturers will have to use an Air Swept Pulverizer or double grind the mix. A 0.8 mm shrimp feed would require the raw materials to pass through 60 mesh (250 microns) but …
اقرأ أكثر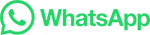
Understanding the Difference Between Raw Mill and Cement Mill
A: Cement mill is generally more energy-efficient than raw mill because the clinker particles in the cement mill are already in a fine powder form, and less grinding is required. The main difference between raw mill and cement mill lies in the raw materials and equipment used to grind them into a fine powder. Understanding these differences is ...
اقرأ أكثر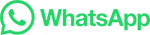
Analysis of material flow and consumption in cement production …
In the surveyed cement plant, three balances are established between input and output material in the raw mill, clinker production, and cement grinding system. 2.48 t, 4.69 t, and 3.41 t of materials are required to produce a ton of the product in raw material preparation, clinker production, and cement grinding stages; waste gases account for ...
اقرأ أكثر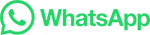
quadropol® vertical roller mill
For raw material grinding four QMR² 48/24 are contracted, while for cement grinding four polycom® high pressure grinding rolls as a combi grinding system are considered due …
اقرأ أكثر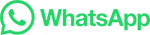
Energy and cement quality optimization of a cement grinding circuit …
Benzer [13] studied on optimizing the fully air-swept raw mill grinding circuit, Dundar et al. [14] reported the optimization opportunities of a cement grinding circuit. ... Modeling and simulation of a fully air swept ball mill in a raw material grinding circuit. Powder Technol., 150 (2005), pp. 145-154.
اقرأ أكثر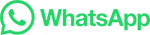
Grinding: benefits of particle size modification | Feed Strategy
Most raw materials used in feed mills must be ground. This process improves the performance of the animal and feed processing, especially mixing homogeneity and pellet quality. Grinding is a key step in the feed production process and offers numerous possibilities for modification and optimization.
اقرأ أكثر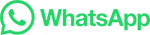
Grinding raw materials
The Hammer Mill lines are each time adapted to the needs of customers in terms of performance, required grinding, adapted to the raw material used, acceptable dimensions etc. Hammer Mills Hammer Mills RB-P and RB-H have been designed for grinding cereal grains, animal feeds, feed components and other similar materials.
اقرأ أكثر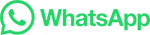
Hammer mills
Optimill hammer mill series. The Optimill series consists of hammer mills that can be applied for grinding of raw materials for normal to coarse structured products. Key features: Coarse-grained particles – optimum particle size range; Patented closed rotor design – saving up to 20% in energy consumption; Large screen area; 1,500-1,800 rpm
اقرأ أكثر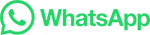
Raw Material Preparation in Cement Manufacturing Plant
The raw material preparation system of the 2 500 t/d cement production line can adopt the vertical mill with the disc diameter of 3 400 mm as the main grinding machine. When the grinding particle size is less than 60 mm, the fineness of the finished product is 16%, and the moisture content of the finished product is 0.5%.
اقرأ أكثر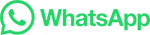
Computation of charging media for a double compartment cement ball mill
The charge of grinding media for two-compartment ball mill can be calculated for dry grinding of cement raw mix. The medium-hard raw material for the mill feed has a particle size range of 0.5 to 25 mm. The mill dimensions are: -. Inner diameter of mill = 4.2 m. Length of drum = 15.25–1.0 = 14.25 m.
اقرأ أكثر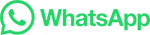
Raw Material Mill-FTM Machinery
The raw material mill adopts high-fine sieving and grinding technology, and has a special structure of double-layer compartment device, active lining plate and grinding tail discharging device to meet the customer's demand for grinding fineness. 02. Low Power Consumption. The performance of the equipment is stable, which can greatly reduce the ...
اقرأ أكثر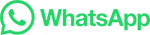
Optimization of a fully air-swept dry grinding cement raw …
1. Introduction. Air-swept raw meal ball mills introduced by the cement mill manufacturers F.L. ® (, 2002), Polysius ® (Polysius, 2002) and KHD Humboldt Wedag® are the most commonly used ones.KHD Humboldt Wedag® manufactured fully air-swept raw meal mills which have two compartments used for drying and grinding …
اقرأ أكثر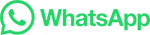
FL: ATOX® raw mill
FL: ATOX® raw mill. February 26, 2013. This film demonstrates all aspects of the FL ATOX® raw mill: how it saves space and energy and why it has been proven to deliver reliable operation for crushing and grinding all types of raw …
اقرأ أكثر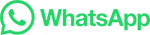
Power Calculation of Ball-Tube Mill Drives in the …
One of the directions of use of ball-tube mills is grinding raw materials, which are further required for obtaining materials such as air binders—gypsum binders, air lime, magnesia binders, Portland cement, mortars, dry construction mixtures, etc. The most common material in construction is Portland cement, a hydraulic binder with a ...
اقرأ أكثر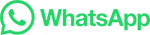
Ball Mill
Quantum Nanostructures (QDs): An Overview. D. Sumanth Kumar, ... H.M. Mahesh, in Synthesis of Inorganic Nanomaterials, 2018 3.6.1.1 Ball Milling. A ball mill is a type of grinder used to grind and blend bulk material into QDs/nanosize using different sized balls. The working principle is simple; impact and attrition size reduction take place as the ball …
اقرأ أكثر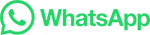
PROCESS OPTIMISATION FOR LOESCHE GRINDING …
For over 100 years the company Loesche has been building vertical roller grinding mills for grinding: Coal. Cement raw material. Clinker / granulated slag. Industrial minerals, and. …
اقرأ أكثر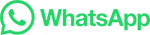
Vertical roller mills | FL Cement
Products. Milling and grinding. Vertical roller mills offer supreme grinding with high energy-efficiency. Whether grinding raw coal, clinker, cement and/or slag, we have a …
اقرأ أكثر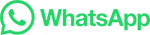