High efficiency grinding of blast furnace slag (vertical mill
Improvements in the grinding process for fine granulated slag was achieved with cement manufacturing technology such as the following: The installation of vertical mill. In a vertical mill, drying, grinding, and separating/classifying of ground material are done simultaneously. The hot air used for drying is supplied with a hot wind generator.
اقرأ أكثر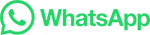
Optimal tracking control for slag grinding process based on …
However, the slag powder grinding process is hard to identify by a mechanism model. In this paper, a data-driven based recurrent neural network model is constructed utilizing the information ...
اقرأ أكثر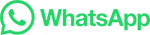
What is Slag Grinding? — Carlson Fabrication …
After a grinder deburrs sheet metal, the parts that chip off are known as slag. Slag grinding removes all heavy slag quickly and effectively, using rotating brushes that work in the opposite direction of …
اقرأ أكثر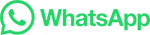
Utilization of lithium slag by wet-grinding process to …
Wet grinding for 30 min can reduce the D(0.5) of lithium slag (LS) from 30.38 μm to 3.04 μm, showing high grinding efficiency. In Wet-grinding process, the dissolution of aluminum, lithium, and silicon in LS were significantly facilitated, which is one of the reasons for the expedited early hydration of SAC-LS system. (2)
اقرأ أكثر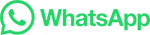
Enhance hydration properties of steel slag using grinding …
Grinding aids have been universally applying to cement production but hardly to grinding steel slag. Grinding aids can save mechanical energy during grinding process, and they also influence on the variations of fineness characteristics [6], [7]. In the grinding process, a variety of grinding aids have been used.
اقرأ أكثر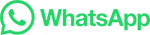
Preparation for micro-lithium slag via wet grinding and its …
DOI: 10.1016/j.jclepro.2019.119528 Corpus ID: 214117536; Preparation for micro-lithium slag via wet grinding and its application as accelerator in Portland cement @article{Tan2020PreparationFM, title={Preparation for micro-lithium slag via wet grinding and its application as accelerator in Portland cement}, author={Hongbo Tan and Li …
اقرأ أكثر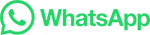
Slag Vertical Roller Mill
Its grinding efficiency and grinding quality directly affect the cost and quality of slag grinding production. As the core equipment in the production process of slag grinding, the LM slag vertical roller mill of SBM integrates fine crushing, grinding, drying, powder selection and transportation, ensuring the continuity and stability of slag ...
اقرأ أكثر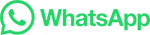
Utilization of lithium slag by wet-grinding process to …
The results show that lithium slag with D(0.5) of 3.04 μm, which is extremely difficult to be prepared in dry-grinding system, can be easily obtained with wet-grinding process; the ions ...
اقرأ أكثر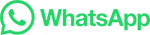
Global Slag Knowledge Base
The Global Slag Knowledge Base is an archive of presentations and papers from the Global Slag Conference since 2007. Global Slag Conference has become the world's foremost gathering for producers and users of iron and steel slag around the world. The conference presentations cover advances in slag modification and optimisation, as well as slag ...
اقرأ أكثر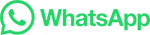
Dust Control for Steel & Slag Processing | BossTek
Systems can also be automated to provide seamless, hands-free operation of DustBoss equipment when dust suppression is needed. Atomized mist has also been proven to lower the ambient air temperature which provides the added benefit of assisting with the cooling process. At BossTek®, we value the efforts being taken across the steel & slag ...
اقرأ أكثر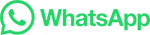
Effect of wet grinded lithium slag on compressive strength …
Raw lithium slag (RLS) was one by-product from carbonate lithium industry. The chemical composition of the SAC and RLS were evaluated by X-ray fluorescence (XRF, Axios advanced), and the results are listed in Table 1. Preparation of nano-LS via wet grinding. Wet-milling technology was employed in the process of handle LS [29], [30], [31].
اقرأ أكثر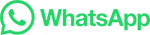
Steel slag in China: Treatment, recycling, and management
Many restrictions exist, however, on the utilization of steel slag. When steel slag is used internally, in steel plants, the most obvious problem is that of the enrichment of P and S (Drissen et al., 2009).The Bhilai Steel Plant in India was shut down because of its high S and P content (Das et al., 2007).The amounts of free lime and free MgO are …
اقرأ أكثر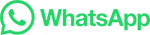
Simultaneously enhanced mechanical and electromagnetic …
The wet-grinding process was performed in a vertical stirred mill, as can be seen in Figure S2. The spherical zirconia (ZrO 2) balls with diameters between 1.2 mm and 1.4 mm were adopted as grinding media.The weight ratio of raw steel slag, water and ZrO 2 balls was 1:1:2. The grinding time was set as 60 min at the speed of 400 rpm.
اقرأ أكثر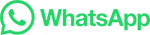
New slag-grinding plant proposed for southwest Detroit …
The slag would be sorted and dried, then sent to a grinding mill. From there, it would be stored in silos. The finished product would be trucked offsite for use, according to EGLE's project ...
اقرأ أكثر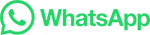
Loesche Mills for Cement and Granulated Blast Furnace …
Grinding of cement clinker and granulated blast furnace slag in roller grinding mills (vertical airswept grinding mills) is a technology introduced by Loesche. The first use of a …
اقرأ أكثر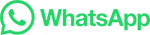
How to Recover Copper from Slag by Flotation
Possibilities for minimizing copper losses in converter slags include: (1) settling the molten slag to recover entrained matte and copper, (2) smelting the slag with a suitable reductant to recover a copper-iron alloy or a low-grade matte. (3) beneficiation of slags by magnetic separation, and. (4) treatment of the slag by flotation.
اقرأ أكثر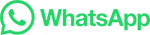
Enhance hydration properties of steel slag using grinding …
Basic oxygen furnace steel slag is a kind of cementitious material with low activity and hard for grinding. The objective of this work was to validate specious grinding aids F1 made in lab which ...
اقرأ أكثر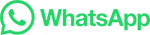
An Energy Efficient Advanced Comminution Process to …
the size reduction process to liberate the metals from slag. The objective of the present research work is to study the influence of operating variables on the performance of HPGR for grinding of ferrochrome slag. The present topic is relevant to the mineral processing field and it describes the energy consumption
اقرأ أكثر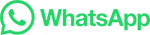
Research of the Effect of Different Dosage of Grinding Aids …
Because of the high hardness and poor wear resistance of steel slag, the potential cementing property of steel slag can not be effectively exerted, and the utilization rate of steel slag. Is low. In order to improve the performance and grinding efficiency of steel slag powder, different grinding aids were added in the process of steel slag …
اقرأ أكثر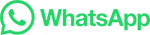
Comprehensive utilization of steel slag: A review
1. Introduction. Steel slag is the main solid waste generated in the steel-making process, accounting for 15 to 20% of crude steel output [1].China's crude steel output in 2021 was 1.035 billion tons [2], more than half of the global crude steel output (1.9505 billion tons) [3], and the steel slag output exceeded 120 million tons.In contrast, …
اقرأ أكثر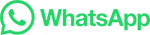
Slag grinding by roller press—major issues
Since the first discovery of cementitious properties of blast furnace slag (BFS) by Emil Langen in 1862 and particularly after the oil crisis in 1970s, manufacture of blast …
اقرأ أكثر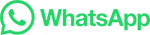
An Energy Efficient Advanced Comminution Process to Treat …
The present research aims to analyze the comminution behavior of ferrochrome slag using high-pressure grinding rolls. The laboratory bench scale high-pressure grinding rolls were used to study the three significant variables on the grinding efficiency of ferrochrome slag. The Central Composite Design was used to study the …
اقرأ أكثر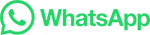
How to Process Slags (with detailed process)? | Fote …
Slag bricks Slag brick production process Slag brick is made by mixing, watering, grinding and pressing slag and limestone. In the production process of slag brick, the particle size of the slag is generally smaller than 8 mm, and the steam temperature injected into the kiln is about 80 ℃ to 100 ℃, the maintaining time is about …
اقرأ أكثر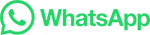
Slag Grinding Unit In Bhadravathi
During grinding, slag or oxides are broken easily into fines and steel pieces, those are difficult to crush, are flattened to chip form.Cement grinding unit process manufacturing process of stone crusher of 8 manufacturing plants out of which 3 are special steel plants and 5 are integrated steel plants that are located in Bhadravathi Durgapur Rourkela …
اقرأ أكثر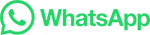
GRINDING Grinding options for slag and pozzolan
Grinding options for slag and pozzolan . While the use of supplementary cementitious materials is increasingly popular, the use of granulated blastfurnace slag and pozzolans …
اقرأ أكثر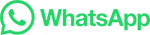
Compressive strength and hydration process of ground
Via wet grinding process, high reactivity of GGBS would be obtained and the strength of mortars could reach 27 MPa at the age of 28 d [48]. Furthermore, the dissolution of ions in waste gypsum could be also expedited by wet grinding. ... Preparation for micro-lithium slag via wet grinding and its application as accelerator in Portland …
اقرأ أكثر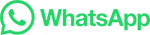
Structure characterization and grinding performance of …
A PG-2D grinding machine with a disk diameter of 230 mm and a rotation speed of 700 r min −1 was used for the grinding test, and the grinding time was 5, 10, and 20 min, respectively. During grinding, the gas-quenched steel slag abrasive and fluid were dispersed between the workpiece and the substrate, which exerted a certain pressure on …
اقرأ أكثر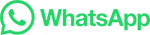
Steel Slag
In the primary process, crude steel is produced in two ways. In the first method, the iron is produced from ore in the BF, thus, generating BF slag (BFS). BBOF slag (BOFS) is produced in the steelmaking process by using the molten iron coming from the BF. In the second method, slags are generated in the scrap-based steel industry.
اقرأ أكثر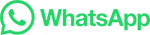
Wet extractive grinding process for efficient calcium …
This paper presents a process improvement of the pH-swing process (referred to as X2PCC) wherein a steelmaking slag is used as a source of calcium oxide for the mineral carbonation of CO 2.We first dissolve Ca from the slag, then separate the solid phase by filtering, and, finally, bubble CO 2 into the Ca-rich solution to precipitate it as …
اقرأ أكثر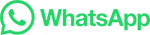
Slag Processing
Technological Process. Dry the wet slag first, and then feed it into the main grinding room for grinding. The fine powder after grinding is classified by the analyzer under the action of the air flow of the fan, and the qualified fine powder enters the collecting stage. The fine powder with qualified fineness enters the pulse dust collector.
اقرأ أكثر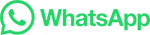