(PDF) Thermodynamic Analysis of Raw Mill in …
6. Conclusion This study focused on exergy utilization, exergy balance and irreversibility for a raw mill in the cement industry using the real plant data and literature data. Exergy efficiency of the raw mill studied using Aspen …
اقرأ أكثر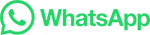
A critical review on energy use and savings in the cement industries
Being an energy intensive industry, typically this segment of industry accounts for 50–60% of the total production costs [17].Thermal energy accounts for about 20–25% of the cement production cost [18].The typical electrical energy consumption of a modern cement plant is about 110–120 kWh per tonne of cement [19].The main thermal …
اقرأ أكثر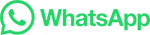
Rolling Bearings in Vertical Mills Built by Gebr. Pfeiffer …
WL 21 509/2 EA. MPS vertical roller mill built by Gebr. Pfeiffer AG, Germany. The cement industry uses MPS mills for grinding cement raw meal, coal, cement additives as well as cement clinker. Vertical roller mills for grinding cement raw meal and coal are the standard today in numerous cement plants. achieved in the past few years in the areas ...
اقرأ أكثر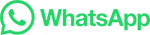
Cement Raw Material | Loesche
The end customer is the Egyptian Cement for Cement Projects Management S.A.E. The planned new plant is located nearly 500 km south of Cairo in Sohag. The LOESCHE scope of delivery includes a raw material mill with a capacity of 540 t/h of cement raw meal, a cement mill with an output of 350 t/h of clinker as well as a coal mill with an output ...
اقرأ أكثر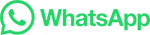
Cement mill fans
Raw mill fan in cement industry carries gas and raw meal. The pressure drop in raw mill fan is very high. ... In cement industry raw mill exhaust fans handle 2.2 ton of exhaust gases for the production of 1 ton of clinker. Raw mill exhaust fans are operated with very adverse situations because the fan handles mainly gases such as CO2, N2, NOx ...
اقرأ أكثر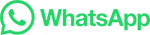
Evaluation of optimization techniques for predicting …
Abstract: In cement production, raw meal preparation and energy consumption are extremely important for cost reduction. However, few studies have examined the …
اقرأ أكثر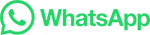
Optimizing Raw Mills Performance ; the Materials WAY
That is the reason that raw meal target moisture is normally maintained within 0.25---1.0 %; furthermore, max raw meal moisture i.e. < 1.0 % is kept to ensure flowability of raw meal.
اقرأ أكثر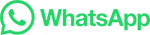
Automated sample preparation in a cement plant
MPC in a cement plant, a model of the raw meal production process has to be established. This model includes many variables like frequency of sampling, time of analysis or retention time of raw meal within the mill. The great advantage of MPC against classic PID controllers is the ability of the MPC to anticipate future events and to
اقرأ أكثر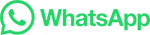
Cement Analysis & Production Solutions | Malvern Panalytical
To improve their cement's quality and consistency, while also supporting sustainability and reducing production costs, manufacturers need reliable material analysis solutions. Solutions like Malvern Panalytical's world-leading instruments: X-Ray Diffraction for mineralogical analysis, X-Ray Fluorescence and Activated Neutrons Cross Belt ...
اقرأ أكثر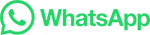
From raw materials Extracting raw materials Raw …
Raw meal silos All over the world, cement is one of the most important building materials. Whether for houses, bridges or tunnels, we cannot imagine our modern world without it. …
اقرأ أكثر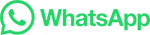
An overview of energy savings measures for cement industries
High efficiency classifiers have been shown to bring about a reduction of 2.8–3.7 kW h/t in raw materials, save fuel and yield a narrow particle size distribution, increase the grinding mill capacity by up to 15%, produce more uniform particles of raw meal and cement and thus enhance the quality of the product and the clinker [90].
اقرأ أكثر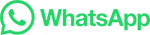
PROCESS TRAINING for operators of Vertical RAW Mills
During heat up there should be a sufficient air flow through the mill to force the heat transfer to the grinding part – forced convection. A sufficient air flow will result in a mill differential pressure of> 5mbar. The duration of heating should be at least until the temperatures after mill and after bag filter reach 85° C.
اقرأ أكثر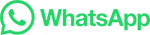
Raw milling and blending
Continuous blending involves simultaneous feeding of the silo, overflow to a second silo and final discharge to kiln feed. Modern equipment generally uses continuous CF silos, each having capacity of more than 24-hours' kiln feed and yielding a blending ratio (or 'blending factor') of 4-8, or around 2-3 for older silos.
اقرأ أكثر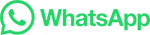
A comprehensive investigation of a grinding unit to reduce …
The exergoeconomic factor for raw meal and cement mills are 38.48% and 59.97% respectively. Total investment and destruction cost rates must be decreased in order to increase the exergoeconomic potential of the factory during pre-calcination of raw meal in pyro-processing tower and calcination processes in rotary burner.
اقرأ أكثر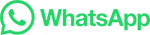
OK™ Raw and Cement Mill
The industry best in energy-efficient grinding, the OK Mill uses five to ten percent less power than other vertical roller mills and 30 to 50 percent less energy than conventional ball mills. ... The main difference between cement and raw OK™ Mills lies in the roller grinding profiles, with the raw mill rollers bearing a spherical shape that ...
اقرأ أكثر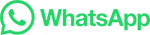
Reducing energy consumption of a raw mill in cement industry
About 2% of the electricity produced in the whole world is used during the grinding process of raw materials [1]. While total electrical energy consumption for cement production is about 100 kWh/ton of cement, roughly two thirds are used for particle size reduction [2]. About 65% of the total electrical energy used in a cement plant is utilized ...
اقرأ أكثر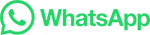
Select your Favorite Type of 7 Different types of Vertical Mill
Fuller-Traylor® Mills are the most robust design in the industry with installations through 27′ in diameter. These heavy-duty mills feature hydrostatic lubrication with either geared or gearless drive arrangements. ... LOESCHE's reference projects include various cement raw meal mills and coal mills in the works at Kaeng Khoi, Lampang and ...
اقرأ أكثر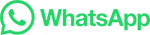
Raw Mill, Cement Raw Mill, Raw Mill In Cement Plant
The cement ball mill usually can be applied to raw meal grinding or cement grinding. Besides, the cement ball mill also can be used for metallurgical, chemical, electric …
اقرأ أكثر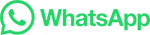
Application of Vertical Roller Mill in Cement Production
In conclusion, the application of vertical roller mill technology in the cement industry has revolutionized the way cement is produced. VRMs are more energy-efficient, eco-friendly, and produce a more consistent product compared to traditional grinding mills. They are also more suitable for use in urban areas due to their lower noise level.
اقرأ أكثر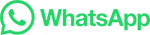
Vertical Raw Mill for Cement Raw Meal Grinding …
So the vertical raw mill particularly suitable for the grinding of cement raw meal in cement factory. The vertical raw mill in cement industry has been applied in the field of medicine and food because of its high …
اقرأ أكثر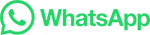
QCX® Automated Samplers
We are the supplier of choice for sampling solutions in the cement industry, providing a wide range of powder and granular material automated samplers. ... Raw materials Mixing bed Raw mill feed Raw meal Electrostatic precipitator or filter dust Kiln feed Hot meal Coal meal Kiln outlet Clinker Cement mill Cement silos and cement dispatch.
اقرأ أكثر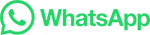
The 6 Main Process Fans in Cement factory
Raw mill fan in cement industry carries gas and raw meal. The pressure drop in raw mill fan is very high. ... In cement industry raw mill exhaust fans handle 2.2 ton of exhaust gases for the production of 1 ton of clinker. Raw mill exhaust fans are operated with very adverse situations because the fan handles mainly gases such as CO2, N2, NOx ...
اقرأ أكثر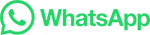
Raw materials for cement manufacturing
Additives are usually brought in small quantities. Limestone: Common forms of calcium carbonate used as raw material for cement manufacturing are limestone and chalk.Limestone is of predominantly fine grained crystalline structure, its hardness is between 1.8 to 3.0 of the Mohs scale of hardness and specific gravity 2.
اقرأ أكثر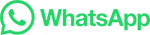
The cement kiln
Manufacturing - the cement kiln. Most Portland cement is made in a rotary kiln. Basically, this is a long cylinder rotating about its axis once every minute or two. The axis is inclined at a slight angle, the end with the burner being lower. The rotation causes the raw meal to gradually pass along from where it enters at the cool end, to the ...
اقرأ أكثر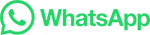
Evaluation of optimization techniques for predicting …
cement raw mill is the primary piece of equipment used in the modern cement industry for the raw meal production process. As a result, it is critical to investigate the exergy efficiency in a cement raw mill in order to satisfy the need for the design and optimization of the cement plant manufacturing process.
اقرأ أكثر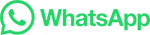
How Does a Raw Mill Work in a Cement Industry
The raw mill is a crucial piece of equipment in cement plants for grinding raw materials into fine powder. Its operation principle involves crushing and grinding …
اقرأ أكثر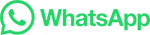
Energy and exergy analyses of a raw mill in a cement …
Utlu et al. [16] performed an energy and exergy analysis of a raw mill in a cement production plant. According to their study, the energy and exergy efficiencies are determined to be 84.3% and 25. ...
اقرأ أكثر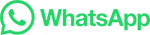
Operational parameters affecting the vertical roller mill …
Abstract. Vertical roller mills (VRM) have found applications mostly in cement grinding operations where they were used in raw meal and finish grinding stages and in power plants for coal grinding. The mill combines crushing, grinding, classification and if necessary drying operations in one unit and enables to decrease number of equipment in ...
اقرأ أكثر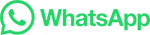
Cement Production Process | Regain Materials
Cement is produced by mixing and fine-grinding clinker, gypsum and mineral components (e.g. limestone, pozzolana, fly ash or granulated blast furnace slag, silica fume) in cement mills. Gypsum is added to control cement setting, i.e. the hardening process. Mineral components are added to reduce the clinker portion in cements and introduce ...
اقرأ أكثر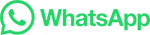
Raw Material Drying-Grinding
Ball mills for cement raw material and coal equipped with a drying compartment adequately air swept with hot gas (2.5-3.5M/sec above the ball charge), can handle moisture about 8%. Fully air- swept mills (5-6M/sec) can dry up to 12-14% moisture. Grinding Operation Objectives and KPIs: Highly energy intensive unit operation of size …
اقرأ أكثر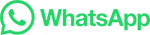