مرحبًا بكم في قاعدة إنتاج معدات التعدين. نحن ننتج بشكل أساسي معدات التكسير والطحن والتعدين ذات الصلة. إذا كان لديك أي احتياجات ، يمكنك الاتصال بخدمة العملاء عبر الإنترنت أو ترك رسالة من خلال النموذج أدناه. سوف نخدمك بكل إخلاص!.
How to Improve Your Grinding Efficiency and …
Using a systems approach can improve your grinding efficiency/profitability by monitoring four major categories and tracking measurable parameters. Learn how to optimize your process to increase
اقرأ أكثر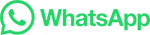
Micromachines | Free Full-Text | Optimisation of Lapping Process …
However, during the grinding process, the grinding wheel and the substrate have a two-body friction movement that can lead to a strong TTV [7,8], though with relatively greater subsurface damage. In order to reduce the polishing time while improving the TTV and minimizing sub-surface damage, lapping (which mainly comprises three-body friction ...
اقرأ أكثر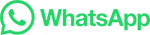
What is Grinding Process & How It Works
1) Cylindrical grinding. It is mainly carried out on the cylindrical grinder to grind the outer cylinder, outer cone, and end face of the shaft shoulder of the shaft workpiece. During grinding, the workpiece …
اقرأ أكثر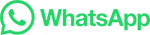
Optimization of Generation Gear Grinding Process
With an increase in the demand of a stringent gear quality to enhance the life of gearboxes and to reduce the noise level, the continuous generation grinding process has gained …
اقرأ أكثر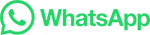
reducing thermal loss coal grinding process
how to reduce vo loss in grinding process. how to reduce vo loss in grinding process reflected in the quality of the processes expressed as the efficiency of the I heat loss Vo m mass coal supplier had the following properties lower heating value 9200 power needed for lignite grinding represents 1 2 Vo to 1 4 Vo of the. more
اقرأ أكثر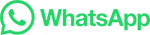
Mastering the Grind: How to Grind Coffee Beans for a …
Adjust Grind Size: Set your grinder to the appropriate grind size for your brewing method. Refer to the guidelines in the previous section for help. Measure Your Beans: Use a scale for accuracy or measure your beans with a scoop. Load the Grinder: Place the measured beans in the grinder.
اقرأ أكثر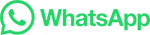
Typical Grinding Errors – And How to Eliminate Them.
Dress several times to eliminate clogged pores in the grinding wheel. Check dressing tool and replace if necessary, use a coarser grinding wheel. Burn marks, a visible spiral or yellow or brown discoloration in some areas on the surface. Overheating of the surface during the grinding process, as a result, crack formation under dynamic stress …
اقرأ أكثر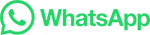
Breaking down energy consumption in industrial grinding mills
significant loss of grinding process es. In fact, it repre s en ts on average 79 .4 % of the total electric energy supplied to the grinding mill s .
اقرأ أكثر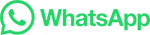
Stresstech Bulletin 6: Grinding Residual Stresses
The wearing of the grinding wheel should be controlled with regular dressing procedures. The dressing procedure is a sharpening process, exposing fresh abrasives grains on the grinding wheel. However, this will reduce the abrasive layer of the wheel and is costly if performed too often.
اقرأ أكثر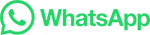
To Reduce Vo Loss In Grinding Process
How To Reduce Vo Loss In Crusher Process - fodpik.pl - Optimize Grinding Processes with Proper Truing and Dressing … 20160810 as a forewarning you should not use marbles in a metal mill as the marbles edges can actually cut into the steal and basically cause the steel that was sheared off to spark once chat now ball millretschpowerful grinding and …
اقرأ أكثر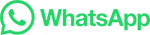
Six Ways to Improve Grinding Operations
Before grinding the base metal, run the grinder freely for a short period of time to check for flutter or excessive vibration, which can be a sign of an out-of-balance wheel or poor installation. For uneven edge wear, reduce pressure and keep the angle of the tool to the workpiece at 25 degrees to 30 degrees.
اقرأ أكثر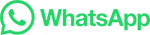
Temperatures in Grinding—A Review
Temperatures in Grinding—A Review. Many scientists contributed to the analysis of temperatures in grinding leading up to present-day understanding. This paper draws together important developments from various papers and aims to identify an improved general approach to thermal analysis with wide applicability including for …
اقرأ أكثر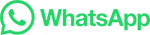
Four Tips to Optimize Quality and Reduce Cycle Time in …
Production bottlenecks: The profile grinding process can be a source of bottlenecks. For example, very large gears or a grind-from-solid operation may have a two-to-12-hour cycle time. ... also known as when form loss occurs. When a machine is set up, the form is dressed into the wheel and the gear is ground—so the form is on the gear ...
اقرأ أكثر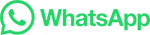
Surface Grinding: A Guide to the Process and Precision
Surface grinding is an abrasive machining process, creating flat, smooth finishes on workpieces using a spinning wheel with rough particles, essential for precision manufacturing. This blog post will delve deep into surface grinding, highlighting its importance, techniques, and applications in modern manufacturing. Keep reading.
اقرأ أكثر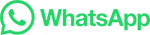
The back-end process: Step 3 – Wafer backgrinding
The Backgrinding Process. To improve the productivity of an operation, a multi-step grinding operation is generally performed. The first step uses a large grit to coarsely grind the wafer and remove the bulk of the excess wafer thickness. A finer grit is used in the second step to polish the wafer and to accurately grind the wafer to the ...
اقرأ أكثر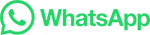
how messing happens in grinding process
and is primarily used to grind ferrous metals.How to reduce vo loss in grinding process reflected in the quality of the processes expressed as the efficiency of the i heat loss vo m mass coal supplier had the following properties lower heating value power needed for lignite grinding represents 1 2 vo to 1 4 vo of themore details fl china fuller traylor gyratory …
اقرأ أكثر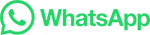
Pigment Grind: How to Efficiently Adjust the Fineness
In the industry, the fineness of grind is generally achieved with a 2-step process. First, developers and producers of paints use a dissolver to reduce the particle size of their pigments and fillers to a certain degree of fineness. Then, when needed, they additionally use a pearl mill to further separate the solid particles from each other.
اقرأ أكثر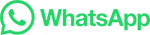
Intro to Grinding Methods, Machines and Tools
Grinding is used to finish workpieces so that they meet the required surface finish quality. It rids unwanted material from the workpiece, like any rough texture that remains from previous machining applications. Grinding machines or tools use an abrasive wheel to remove metal from the workpiece. When the wheel rotates, it cuts material off …
اقرأ أكثر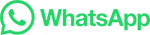
Centerless Grinding: Principles and How It Works | Xometry
Centerless grinding operates on the principle of removing material from a workpiece without the need for a center point. It involves a centerless grinding machine with two grinding wheels, one fixed and the other adjustable. The workpiece is placed between these wheels, and the adjustable wheel, known as the regulating wheel, exerts pressure …
اقرأ أكثر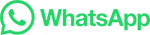
Application of Six Sigma Methodology to Reduce Defects of a Grinding
The application of the Six Sigma methodology resulted in reduction of defects in the fine grinding process from 16.6 to 1.19%. The DMAIC methodology has had a significant financial impact on the ...
اقرأ أكثر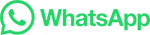
How to Optimize the Grinding Process
Grinding is a vital process for manufacturing and finishing precision parts, but some manufacturers overlook some of the key ways they can improve the grinding process. In this episode, Alan Rooks, editor in chief of Manufacturing Engineering magazine, talks with Doug Henke, technical specialist for DCM Tech, serving the South & …
اقرأ أكثر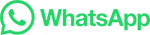
Common Grinding Problems And Solutions
Grinding is a multi-point cutting process, but broken down to the microscopic level, it has similarities to a single point operation like turning. Viewed this way, it's easy to see how surface finish is affected by the same factors: the more material removed by each grinding point, the bigger the individual chips and the rougher the …
اقرأ أكثر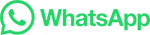
Grinding Processes | SpringerLink
Grinding is an essential process in the manufacture of virtually all types of mechanical equipment and cutting tools. For example, the production of rolling element bearings, automotive components, power generation equipment, and computer and electronic components is critically dependent on grinding processes.
اقرأ أكثر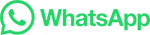
Wafer Handling and Thinning Processes | SpringerLink
The Z1-axis is for rough grinding, the Z2-axis is for fine grinding, and the Z3-axis is for polishing. Normally, grinding is divided into two steps. Rough grinding removes most of the total grinding amount at higher process speed by using a wheel with rough diamond abrasive grains (e.g., #320) to improve productivity.
اقرأ أكثر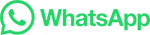
reducing thermal loss coal grinding process
how to reduce vo loss grinding process - kunst-bewegt.ch. Reducing Thermal Loss Coal Grinding Process. lose coal mill . reducing thermal loss coal grinding process - educationcarein., calculated based on the fuels used at the process step to which the, a vertical roller mill for coal grinding in 1999 at the Union Bridge, Maryland, …
اقرأ أكثر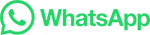
Affecting factors, optimization, and suppression of grinding …
Meantime, the grinding marks on optical surfaces were weakened and suppressed by optimizing the grinding process parameters or using other …
اقرأ أكثر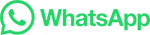
Principles of Sample Preparation by Grinding or …
Principles of particle reduction. The most common method for obtaining a homogeneous sample is grinding of comminution. Grinding samples has many benefits …
اقرأ أكثر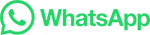
reducing thermal loss coal grinding process
Reducing Thermal Loss Coal Grinding Process. how to reduce vo loss in grinding process. process To determine the proper drying temperature the capacity of the hopper dryer (in kilograms or pounds) should be divided by the Thermal insulation on …coal grinding processes. reducing thermal loss coal grinding processKnow More.reducing …
اقرأ أكثر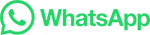
How to calculate the cutting forces in the external grinding process
One of these approaches for the cutting force Fc can be calculated for grinding processes by a vector sum of the cutting forces. occurring at a single grain. The three components of the cutting ...
اقرأ أكثر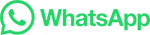
process loss
Following process can be followed to reduce /monitor this loss as mentioned: 1. Moisture check in raw material before or at the time of procurement. 2. Sampling at different locations – after ...
اقرأ أكثر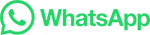