Electric arc furnaces: the technology poised to make British
The purpose of the blast furnace is to separate iron ore extracted from the ground into its component parts: iron and oxygen. A form of carbon, normally coal, combines with the oxygen in the iron ore.
اقرأ أكثر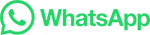
Blast Furnace Process
Molten iron is produced in a blast furnace by the following steps: 1. Charge (solid iron ore, coke, and limestone) is constantly dumped into the top of the furnace. 2. A blast of hot air is blown into the furnace …
اقرأ أكثر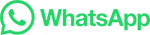
Blast Furnace Ironmaking | ScienceDirect
In 2016, over 1 billion tonnes of molten iron were produced from 700 to 900 blast furnaces operating on every continent, except Antarctica. Using iron ore-based sinter and pellets and fuels that include metallurgical coke and injected hydrocarbons, the blast furnace produces a carbon-saturated iron alloy known as hot metal—an important raw ...
اقرأ أكثر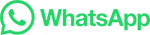
Blast Furnace Ironmaking
The blast furnace (BF) ironmaking process is currently the dominant process for providing steelmaking raw materials worldwide. However, the BF process …
اقرأ أكثر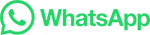
New iron production process could cut carbon emissions …
EUGENE, Ore. - A process that University of Oregon researchers say is cleaner and cheaper could be employed by steel mills to replace carbon-spewing blast furnaces. Researchers published their ...
اقرأ أكثر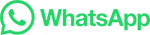
blast furnace summary | Britannica
Blast furnaces are used to produce pig iron from iron ore for subsequent processing into steel; they are also employed in processing lead, copper, and other metals. The current of pressurized air maintains rapid combustion. Blast furnaces were used in China as early as 200 bc, and appeared in Europe in the 13th century, replacing the bloomery ...
اقرأ أكثر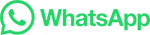
Blast Furnace Slag
10.2.2 Blast furnace slag. Blast furnace slag (BFS) is a by-product from iron production in blast furnaces, which are fed by a mixture of iron-ore, coke and limestone. In the process, the iron ore is reduced to iron while all remaining materials form the slag, which is tapped off as a molten liquid and cooled.
اقرأ أكثر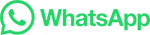
Iron Making
Since 4,000 years ago, when humans learned how to free iron from ore, the basic process has not changed. Iron oxide is heated in an intense flame fed by carbon fuel. Oxygen in the ore combines with carbon monoxide released from the fuel and is expelled as CO 2. What is left is iron. The blast furnace's height lets the rising gases preheat the ...
اقرأ أكثر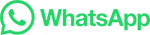
MAXIMIZING LOW FE HYGROSCOPIC IRON ORE …
Keywords:- Low Grade Goan Iron Ore, Process Optimization, Cost of production. Iron Ore Iron ores are rocks and minerals from which metallic iron can be economically extracted. Iron ore is the raw material used to make pig iron, which is one of the main raw materials to make steel. 98% of the mined iron ore is used to make steel.
اقرأ أكثر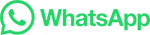
Improved iron-ore pellets for blast furnaces | Steel in …
A production technology for iron-ore materials with improved metallurgical characteristics is developed and tested. The following materials are considered: fluxed pellets containing residual carbon; fluxed local agglomerates from concentrates with a wide range of silica content; local agglomerates with an elevated iron content; local …
اقرأ أكثر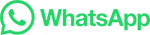
Blast furnace explained
Blast furnace explained. A blast furnace is a type of metallurgical furnace used for smelting to produce industrial metals, generally pig iron, but also others such as lead or copper. Blast refers to the combustion air being supplied above atmospheric pressure.. In a blast furnace, fuel (), ores, and flux are continuously supplied through the top of the furnace, …
اقرأ أكثر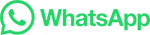
Iron Production
The production of iron from its ore involves an oxidation-reduction reaction carried out in a blast furnace. Iron ore is usually a mixture of iron and vast quantities of …
اقرأ أكثر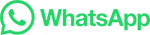
Extraction of Iron | Metallurgy | Blast Furnace and Reactions
The extraction of iron from its ore is a long and subdued process, that helps in separating the useful components from the waste materials such as slag. What happens in the Blast Furnace? The purpose of a Blast Furnace is to reduce the concentrated ore chemically …
اقرأ أكثر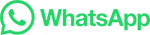
Blast Furnace
The Blast Furnace is located in Keldagrim.To enter Keldagrim, the player must have started the The Giant Dwarf quest by speaking to the Dwarven Boatman within the mines east of Rellekka. The map on the right shows a path the player can take walking from Seers' Village/Camelot to the mines east of Rellekka. Once the player has visited Keldagrim at …
اقرأ أكثر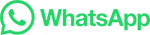
Electric Arc Furnace vs. Blast Furnace | Steel …
Melts iron ore and coke so it can produce pig iron high in carbon content and this is then is fed into a converter to remove impurities. Needs a high investment in facility development and takes up a large …
اقرأ أكثر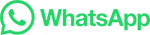
Iron processing | Definition, History, Steps, Uses, …
iron processing, use of a smelting process to turn the ore into a form from which products can be fashioned. Included in this article also is a discussion of the mining of iron and of its preparation for smelting. Iron (Fe) is a …
اقرأ أكثر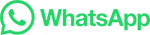
Iron Ore Reactions and Phenomena in a Blast Furnace
Blast furnaces (BF) are still the dominant process for making iron in the world. Blast furnaces are charged with iron ores in the form of pellets, sinter and/or …
اقرأ أكثر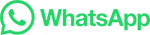
Production of Iron in the Blast Furnace | SpringerLink
The reduction of iron ore in the blast furnace mainly consists in the liberation of the oxygen associated with the metals and the combination of this oxygen …
اقرأ أكثر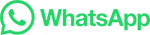
Steel 101
Source: Adapted from Hasanbeigi, A. and Springer, C. 2019. 5 Integrated Blast Furnace (BF) and Basic Oxygen Furnace (BOF) A blast furnace is the first process in manufacturing steel from iron ore, which is mined. Blast furnaces heat purified coal, or "coke," limestone, and iron ore, then inject it with oxygen to reduce the carbon content …
اقرأ أكثر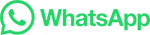
THE BLAST FURNACE
As the mixture of iron ore, coke and limestone heats, the hot waste gases are collected and cleansed. They are then used to help heat the air blast, required if blast furnace is to reach the high temperatures needed to produce molten iron. The stock level is constantly 'topped up'. Molten iron ore is 'tapped' at the bottom of the blast ...
اقرأ أكثر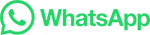
Use of Ore-Coal Briquettes in Blast Furnaces | Metallurgist
The current state of briquetting technology in iron smelting processes is assessed. For the first time, the importance of using ore-coal briquettes for the charge in blast furnace processes as a means of reducing the total carbon consumption and emissions of CO2 is shown. The role of solid-state reduction in blast-furnace ore-coal briquettes in improving …
اقرأ أكثر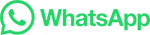
From Ore to Iron with Smelting and Direct Iron Reduction
Smelting Reduction. Figure 2: The smelt reduction vessel (SRV) is the core technology component of the Hismelt process. Source: RioTinto While years of ironmaking technology innovations have optimized blast furnace productivity, two alternative processes—smelting reduction and direct iron reduction— are growing in adoption. The …
اقرأ أكثر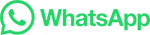
The Blast Furnace: A Vital Tool in Climate Neutral Ore-Based
Globally, almost 90% of CO 2 emissions of 'primary steelmaking' come from use of coal/coke in the blast furnaces. More than half of the energy from this carbon is used to provide energy for heating and generation of electricity. ... The process of transformation of iron ore to steel involves a number of steps—irrespective of the exact ...
اقرأ أكثر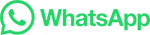
Blast Furnace
The blast furnace process has auxiliary equipment associated with it. ... BFG is a by-product of the chemical reduction of iron ore in blast furnaces. It typically contains about 20–30% carbon monoxide (CO) and about 2–6% hydrogen (H 2) as combustible components, ...
اقرأ أكثر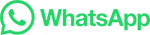
Tata Steel: What is the difference between a blast furnace …
How does a blast furnace work? In order to make steel using a blast furnace, first iron needs to be produced. Steelworkers do this by adding iron ore, coke and limestone into the furnace.
اقرأ أكثر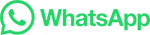
Improvements in Iron Processing and the Development of the Blast
Better iron, the product of blast furnaces, changed the world more dramatically. Iron—and steel—would become the most important manufacturing materials of the modern world. Improvements in iron meant improvements in weapons, often to devastating effect. Iron plows offered an agricultural advance equaled only by the earliest cultivation of ...
اقرأ أكثر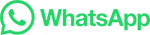
Iron ore pelletization
15.1. Introduction. Iron ore lump, sinter, and pellets comprise the main burden of modern blast furnaces. However, sinter and pellets are now the dominant blast furnace burden, because the natural lump supply has declined dramatically due to depletion of the world's high-grade competent iron ore resources.
اقرأ أكثر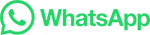
Blast furnace | Definition, Temperature, Diagrams, …
Blast furnaces produce pig iron from iron ore by the reducing action of carbon (supplied as coke) at a high temperature in the presence of a …
اقرأ أكثر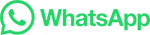
Blast Furnace Process | SpringerLink
Temperature profile in a blast furnace (iron ore starts melting at 1100–1150 ℃ and slag become fully liquid at 1350–1400 ℃) ... In the blast furnace process, iron-bearing materials (e.g. lumps iron ore, sinter/pellets, mill scale and steelmaking slag), coke (fuel as well as reducer) and flux (limestone and/or dolomite) are charged by ...
اقرأ أكثر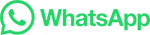
What is steel and how is steel made?
Blast Furnace Route . Large European blast furnaces can produce around four million tonnes of iron per year. They rely on a chemical process called reduction: Iron ore is an iron oxide and to separate iron from oxygen carbon is needed as a so-called reducing agent. In the process it combines with the oxygen and forms carbon dioxide.
اقرأ أكثر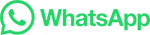