Understanding the Aluminium Scrap Melting …
Udo Boin et al.: Measuring – Modelling: Understanding the Al Scrap Melting Processes Inside a Rotary Furnace. 1 Introduction. A rotary furnace is the preferred melting device at alumin-. ium ...
اقرأ أكثر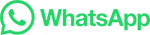
Reduction Smelting of the Waelz Slag from …
Waelz slag is an iron-containing waste generated during electric arc furnace (EAF) dust processing in a rotary kiln named the Waelz process. This study focuses on the reduction smelting of the …
اقرأ أكثر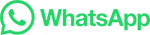
Application of CSC Technology in Nonferrous Metallurgy
291 kgce/t of leach residue, 32% more fuel-efficient than that of the rotary kiln. Waste slag. Zinc ≤ 2.5%, Pb ≤ 0.5%, Ag ≤ 20 g/t (5) Main features. ... At present, the antimony pyrometallurgy process is the dominant process for antimony smelting, with the most important representative being the "antimony concentrate volatilization and ...
اقرأ أكثر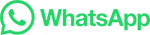
Nickel Laterite Smelting Processes and Some Examples …
2. Alternative Nickel Laterite Smelting Processes to the Rotary Kiln-Electric Furnace (RKEF) Process 2.1. The Vaniukov Process The Vaniukov process is a well-established technology for pyrometallurgical treatments, especially for the smelting of copper ores [11,12]. Its use in laterite smelting was studied in the last decade. The process for ...
اقرأ أكثر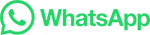
Efficient Bath-Smelting Reduction of Antimony Oxide in
A process for the recovery of lead from lead by-product materials, including lead-containing slag and other lead-containing waste materials, in a rotary smelting furnace using an active alkali ...
اقرأ أكثر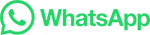
Enhancing Rotary Kiln-Electric Furnace Process of Saprolitic …
How to reduce the energy consumption of the rotary kiln-electric furnace (RKEF) process has become an important issue for the stainless steel industry. The aim of this study is to reduce the energy consumption of ferronickel production from saprolite nickel laterite in the RKEF process. The effects of the slag binary basicity, FeO content, and …
اقرأ أكثر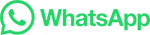
Thermal Science and Engineering Progress
The rotary kiln furnace shows energy and exergy ef- ficiencies of 66.4% and 32.3%, respectively, leaving room for waste heat recovery. Particles with surface-to-
اقرأ أكثر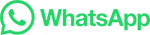
CN1339612A
Two kiln methods have countries and regions such as North America, West Europe and Bolivia in industrial this method of widespread use.This method adopts two rotary kiln evaporation roastings, first rotary kiln is handled and to be contained the antimony amount and be not less than 60% stibnite concentrate, the powder concentrate sprayed into ...
اقرأ أكثر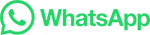
Green and Effective Purification of Antimony and Recovery …
Noble antimony is the carrier of precious metals in the antimony smelting system and has a very high added value. This study proposes a novel, green, and effective vacuum gasification process for purifying antimony and recovering precious metals from noble antimony. Saturated vapor pressure and separation coefficients (β) were used to …
اقرأ أكثر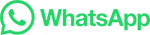
Fixing sulfur dioxide by feeding calcine oxide into the …
-xation agent is demonstrated to be an ecient in-furnace desulfurization strategy for zinc smelting plant. The sulfur distribution within the entire smelting process is systematically analyzed, determining that the critical procedure for pressuring the desulfurization system is the rotary volatilization kiln.
اقرأ أكثر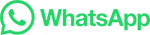
smelting process for antimony
Lead processing BritannicaArsenical bronze Wikipedia. However some primary refineries also refine secondary lead this has led to a growing use of rotary furnaces which are batch kilns that are rotated during the smelting process The bulk of secondary lead alloy recovered from reclaimed batteries and cable sheathing contains small percentages of …
اقرأ أكثر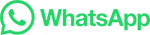
A Review on Pyrometallurgical Extraction of …
Abstract. Antimony is classified as a critical/strategic metal. Its primary production is predominated by China via pyrometallurgical …
اقرأ أكثر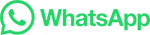
BACKGROUND REPORT AP-42 SECTION 12-11
2.2 PROCESS DESCRIPTION Secondary lead smelting includes three major operations: scrap pretreatment, smelting, and refining. These are shown schematically in Figures 2.2-1A, 2.2-1B, and 2.2-1C, respectively. ... three to four percent antimony; however, rotary kiln furnaces are rarely used in the U.S. and will not be discussed in detail.
اقرأ أكثر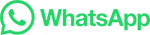
Article Hydrometallurgical Process for Zinc Recovery …
The Waelz process is widely used to dispose of furnace dusts when the zinc content is higher than approximately 15–20%. In the 21st century, the Waelz process is used more widely than ever before. In this process, zinc-bearing dust is reductively heated in a rotary kiln to approximately 1200 °C [6–8]. Zinc, lead, chloride, and fluoride
اقرأ أكثر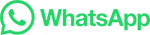
A hydrometallurgical process for the separation and recovery of antimony
A process for antimony recovery from stibnite concentrate is proposed. ... of low-concentration SO 2 and some other released heavy metals cause serious environmental pollution in areas surrounding antimony smelting plants. ... After liquid antimony was discharged from the bottom of a rotary kiln, the melt (mainly Na 2 CO 3 …
اقرأ أكثر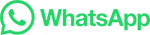
Thermodynamic analysis and process optimization of zinc …
Thermodynamic analysis and process optimization of zinc and lead recovery from copper smelting slag with chlorination roasting. Author links ... Pb, and Sb in antimony smelting slag could be recovered by the fuming furnace process, with metal recoveries of 88%, 95%, and 60%, respectively. PENG et al [9] presented a …
اقرأ أكثر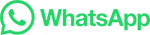
Novel method for temperature prediction in rotary kiln process …
Blast furnace high-proportion pellet smelting stands as a pivotal pathway towards achieving low-carbon and environmentally friendly ironmaking. However, challenges in pellet ore production, particularly through the rotary kiln method, have surfaced due to the scarcity of iron ore resources, leading to issues like "ringing" that …
اقرأ أكثر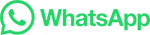
Rotary Kilns: Processes Defined
A rotary kiln is a thermal processing tool used in a variety of applications. It consists of a rotating drum with high temperature products of combustion flowing through or around it, creating a precisely controlled environment for material property change. Due to the substantially high internal temperatures of rotary kilns, observing a ...
اقرأ أكثر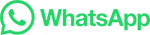
The metallurgy of antimony
1. Background. Antimony is a silvery, white, brittle, crystalline solid that exhibits poor conductivity of electricity and heat. It has an atomic number of 51, an atomic weight of 122 and a density of 6.697 kg/m 3 at 26 °C. Antimony metal, also known as 'regulus', melts at 630 °C and boils at 1380 °C.Antimony and the natural sulfide of …
اقرأ أكثر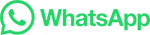
A hydrometallurgical process for the separation and …
Consequently, antimony metal and a melt mainly containing sodium carbonate and resultant sodium chloride were obtained. After liquid antimony was …
اقرأ أكثر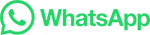
Pyrometallurgical recycling of electric arc furnace dust
The rotary kiln furnace is used to treat Waelz oxide to refine zinc with elimination of lead, cadmium and chlorides (Morcali et al., 2012). Download : Download high-res image (293KB) Download : Download full-size image; Fig. 5. Flow chart of Waelz kiln process (Mager et al., 2003).
اقرأ أكثر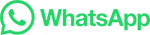
Antimony Smelting
Antimony Smelting. China now leads the world in antimony production, having contributed during recent years something …
اقرأ أكثر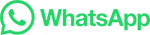
The Recovery of Pb and Zn in Antimony Smelting Slag
There are some smelting slag treatment technologies utilized in China at present, which are rotary kiln process and fuming furnace process. Rotary kiln …
اقرأ أكثر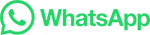
A Review on Pyrometallurgical Extraction of Antimony from …
Process selection for treatment of antimony ores (adapted from [54]). Flow diagram of volatilization smelting of stibnite in blast furnace-reverberatory furnace (adapted from [19]). +4
اقرأ أكثر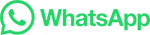
Clean antimony production from stibnite concentrate with …
In view of the issues of low efficiency and environmental pollution existing in current antimony production, this work proposes an innovative and cleaner process to …
اقرأ أكثر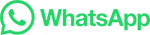
Vanadium-Titanium Magnetite Carbon-Containing …
requirement in the rotary kiln, the kiln tail gas produced by the rotary kiln is cooled, pu-rified, and removed of carbon dioxide, and then get into the top of the smelting reduction furnace, thereby reducing the temperature of the smelting reduction gas to 900. 1200 °C, finally directly into the rotary kiln for combustion [15].
اقرأ أكثر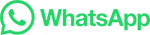
A New Pyrometallurgical Process for Producing Antimony …
Antimonial dust is a by-product of lead smelting and an important material for extracting antimony. A new pyrometallurgical process for producing antimony white from the antimonial dust is reported. The process mainly consists of three steps, which are reduction smelting, alkaline refining, and blowing oxidation. First, the reduction smelting …
اقرأ أكثر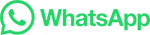
A Review on Pyrometallurgical Extraction of Antimony from …
Antimony. Article PDF Available. A Review on Pyrometallurgical Extraction of Antimony from Primary Resources: Current Practices and Evolving Processes. …
اقرأ أكثر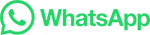
Unlocking the Process: How Lead Ingots are Produced
Our process lies on fixed rotary furnace technology engineered by our R&D and improved over the years on the field to reduce at minimum the NG consumption/cycle while improving the time to smelt. 4. Refining: The lead bullion obtained from the smelting process usually contains impurities such as copper, tin, antimony, arsenic, and other trace ...
اقرأ أكثر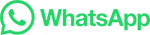
Thermodynamic modeling of antimony removal from
DOI: 10.1016/s1003-6326(22)66082-5 Corpus ID: 255924606; Thermodynamic modeling of antimony removal from complex resources in copper smelting process @article{Wang2022ThermodynamicMO, title={Thermodynamic modeling of antimony removal from complex resources in copper smelting process}, author={cSong-song …
اقرأ أكثر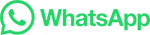