LECTURE NOTES ON Sponge Iron & Ferro Alloys
Methods of producing low carbon wrought iron directly from the ore are known as direct reduction process. After the development of the blast furnace, the DR processes were nearly abandoned. However after 1980s DR processes find wide acceptance because here the iron ore is reduced at lower temperature using low grade coal. Many
اقرأ أكثر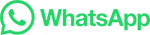
On the direct process of making wrought-iron and steel
Inst., 408 DuPuy--Iron and Steel. 53 pounds of iron in muck-bar from 100 pounds of ore charged', and whichit was expected would have been brought up to 60 pounds of iron from 100 pounds of ore, gradually became very much lessened, showing conclusively that reduced yield followed the softening of the bottom, and determined the necessity of a ...
اقرأ أكثر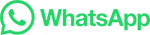
What is Wrought Iron? (Blacksmithing Guide)
The puddling process is the large-scale production process of wrought iron. Cast iron is typically made by melting iron ore and mixing it with scrap metals. ... It is a mixture of silicon dioxide and metal oxides made up of the waste removed from the raw ore material. Wrought iron typically has a visible fibrous structure due to the silicates ...
اقرأ أكثر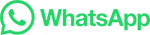
Iron Making | Boundless World History
Carburization is a heat treatment process, in which iron or steel absorbs carbon while the metal is heated in the presence of a carbon-bearing material, such as charcoal or carbon monoxide. The intent is to make the metal harder. Unlike modern steel making, the process increased the amount of carbon in the iron.
اقرأ أكثر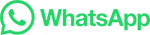
Manufacture of Iron— New Process for Making Wrought …
A new process for making wrought-iron direct from the ore, independently of the usual introductory melt-ins; into pigs, has been discovered by Mr. Jas. Renton, of Newark, N. J., who has taken ...
اقرأ أكثر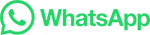
How Iron Was Made
Iron making evolved over a few thousand years. Using the ancient "bloomery" method, iron ore was converted directly into wrought iron by heating the …
اقرأ أكثر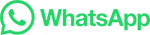
The Bloomary Process + pics
years ago a simple process – now called direct reduction – was in use in the Middle East for making wrought iron. It was based on a chemical reaction taking place in a simple furnace to remove the oxygen from the iron ore. Originally finds, of pure, usable iron were rare and of meteoritic origin. Artifacts such as simple cutting tools
اقرأ أكثر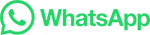
Pig Iron and Its Manufacturing
The pig iron is obtained from the iron ores in the following steps: 1. Concentration. It is the process of removing the impurities like clay, sand etc. from the iron ore by washing with water. 2. Calcination or roasting. It is the process of expelling moisture, carbon dioxide, sulphur and arsenic from the iron ore by heating in shallow kilns. 3 ...
اقرأ أكثر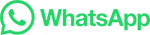
Pig Iron Manufacturing Process
Pig Iron Manufacturing Process. At the beginning of the use of the electric furnace, for the manufacture of calcium carbide and ferro-alloys, experimental work was conducted in it upon the production of steel from iron ore. For many years steel and wrought iron have been produced directly from ore on a small scale in the forge, …
اقرأ أكثر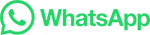
DISCUSSION. MR. CLAY'S NEW PROCESS FOR MAKING WROUGHT IRON DIRECT …
ICE Virtual Library essential engineering knowledge. Cart. Mobile
اقرأ أكثر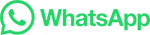
DESCRIPTION OF MR. CLAY'S NEW PROCESS FOR MAKING WROUGHT IRON DIRECT
ICE Virtual Library essential engineering knowledge. Cart. Mobile
اقرأ أكثر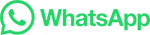
On the direct process of making wrought iron and steel
Dec, 1877.] Du _Puy--Iron and Steel. 377 ON THE DIRECT PROCESS OF MAKING WROUGHT IRON AND STEEL I. By Cm~s. M. Du PuY, C.E. I t is scarcely necessary, at this late day, and before this Institute, to explain the difference between the "direct" and the "indirect" methods of producing iron that can be forged.
اقرأ أكثر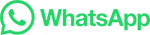
From Ore to Iron with Smelting and Direct Iron …
Ironmaking 101 – From Ore to Iron with Smelting and Direct Iron Reduction. Figure 1: Steelmaking byproducts for blast furnace (BF), …
اقرأ أكثر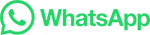
How Iron Was Made
Iron making evolved over a few thousand years. Using the ancient "bloomery" method, iron ore was converted directly into wrought iron by heating the ore while at the same time melting the ore's impurities and squeezing them out with hand hammers. This is also called the "direct process." By the 1100s water-powered …
اقرأ أكثر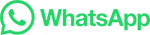
(PDF) iron-steel making From start to finish
The Iron Ore, Coke and Limes tone, (the ... • Iron from direct reduction process ... Presentation will help to provide basic principle and brief overview of iron making to steel making process ...
اقرأ أكثر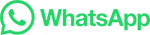
Chapter 1 Review of Sponge Iron Making Process …
Methods of producing low carbon wrought iron directly from the ore are known as direct reduction process. After the development of the blast furnace, the DR processes were nearly abandoned. However after 1980s DR processes find wide acceptance because here the iron ore is reduced at lower temperature using low grade coal.
اقرأ أكثر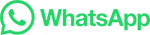
Wrought Iron Production
The production of wrought iron or steel is a process containing two main stages. The first stage is to produce pig iron from iron ore in a blast furnace. Alternatively, it may be directly reduced. The second is to make …
اقرأ أكثر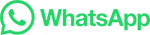
Iron Making | Boundless World History
Carburization is a heat treatment process, in which iron or steel absorbs carbon while the metal is heated in the presence of a carbon-bearing material, such as charcoal or carbon monoxide. The intent is to make the …
اقرأ أكثر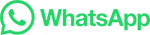
23.3: Metallurgy of Iron and Steel
Figure 23.3.1 23.3. 1: A Blast Furnace for Converting Iron Oxides to Iron Metal. (a) The furnace is charged with alternating layers of iron ore (largely Fe2O3) and a mixture of coke (C) and limestone (CaCO3). Blasting hot air into the mixture from the bottom causes it to ignite, producing CO and raising the temperature of the lower part of the ...
اقرأ أكثر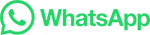
How to Manufacture Pig Iron: How Pig Iron is made?
Guide for manufacturing and making Pig Iron. Following three distinct operations are involved in the manufacturing process of pig-iron: (1) Dressing (2) Calcination and roasting (3) Smelting. (1) Dressing: The iron ores as obtained from mines are crushed into pieces of size of 25 mm diameter. This is achieved in the rock crushers of ordinary type. The …
اقرأ أكثر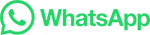
Iron Making
Hopewell Furnace made castings and pig iron from 1771-1883. An ancient alchemy sustained Hopewell Furnace: transforming mineral into metal. Since 4,000 years ago, when humans learned how to free iron from ore, the basic process has not changed. Iron oxide is heated in an intense flame fed by carbon fuel. Oxygen in the ore combines …
اقرأ أكثر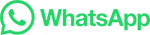
Extraction of Iron | Metallurgy | Blast Furnace and Reactions …
The extraction of iron from its ore is a long and subdued process, that helps in separating the useful components from the waste materials such as slag. ... Wrought Iron/ Malleable Iron. Wrought iron is the purest form of iron available commercially available and is prepared from cast iron by heating cast iron in a furnace lined with Haematite ...
اقرأ أكثر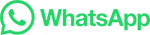
A Process For Making Wrought Iron Direct From …
A Process For Making Wrought Iron Direct From The Ore. Continued In the Siemens process pieces of ore of the size of beans or peas, mixed with lime or other fluxing material, form the charge, which is introduced into a …
اقرأ أكثر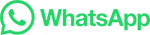
Wrought iron | Properties, Uses & History | Britannica
wrought iron, one of the two forms in which iron is obtained by smelting; the other is cast iron ( q.v. ). Wrought iron is a soft, ductile, fibrous variety that is produced from a semifused mass of relatively pure iron globules partially surrounded by slag. It usually contains less than 0.1 percent carbon and 1 or 2 percent slag.
اقرأ أكثر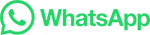
BELL & SETT, Making Iron Direct from Ore,
puddling-furnace, so that the hot ore could be easily dropped through a suitable opening directly on the required place in the furnace. Subsequently several apparatuses or devices have been made in this country for making wrought or malleable iron direct from the ore. In 1841 Mr. Quilliard obtained a patent for a process and apparatus very ...
اقرأ أكثر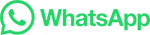
Ironmaking 101 – From Ore to Iron with Blast …
Iron is mainly extracted from hematite (Fe 2 O 3) and magnetite ores. Natural or direct shipping iron ores contain between 50-70% iron and can be fed directly into the blast furnace. Fe 3 O 4 …
اقرأ أكثر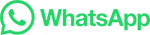
How iron is made
Iron ore is converted into various types of iron through several processes. The most common process is the use of a blast furnace to produce pig iron which is about 92-94% iron and 3-5% carbon with smaller amounts of other elements.
اقرأ أكثر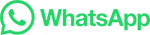
Industrial Revolution iron method 'was taken from Jamaica …
Wrought iron process that drove UK success was appropriated from black metallurgists, records suggest Hannah Devlin Science correspondent Wed 5 Jul 2023 02.00 EDT Last modified on Wed 5 Jul 2023 ...
اقرأ أكثر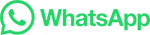
Guide to Historic Iron Making
Wrought iron produced from a finery forge or directly from a bloomery furnace is what we use to make our actual tools and weapons. Unlike bronze, you cannot cast wrought iron.
اقرأ أكثر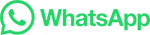
Iron Making
Hopewell Furnace made castings and pig iron from 1771-1883. An ancient alchemy sustained Hopewell Furnace: transforming mineral into metal. Since 4,000 years …
اقرأ أكثر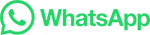