Effective mechanochemical synthesis of sulfide solid
The ball mill is a rotating cylindrical vessel with grinding media inside, which is responsible for breaking the ore particles. Grinding media play an important role in the comminution of mineral ...
اقرأ أكثر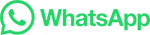
Ball Mill | SpringerLink
Ball Mill. Ball mill is a type of grinding equipment that uses the rotary cylinder to bring the grinding medium and materials to a certain height and make them squeeze, impact, and grind and peel each other to grind materials. Ball mill is the key equipment for crushing materials after they are crushed. It is widely used in cement, …
اقرأ أكثر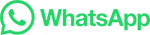
Ball milling process variables optimization for high-entropy …
For milling time, the ball milling process was interrupted at a regular interval of 10 h for powder extraction and characterization, up to a total milling time of 60 h. It is worth noting that a small ball (which weighs ~1 g) is removed at every 0.1 g of powder extraction to maintain the ball-to-powder ratio. 2.3. Materials characterization
اقرأ أكثر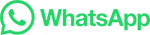
Planetary Ball Mill Process in Aspect of Milling Energy
Energy dissipated per hit versus the rotation speed of the planetary ball mill (Fritsch " Pulverisette 5 " [11] (a) and AGO-2 (b)). (a) The energy map for the Pd-Si system, letter a = Pd 86.5 Si ...
اقرأ أكثر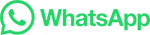
How Ball Mills Contribute to Battery Technology
A third and essential characteristic of a ball mill, which greatly influences the outcome of the milling process, is the mill's power. This is usually determined by the application. For example, gentle material processing requires gentle and slow movements of the jar, whereas to achieve grinding effects, agitating jars at high speeds is the ...
اقرأ أكثر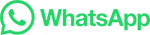
Enhancing the capacity of large-scale ball mill through process …
The main aim of this study is to improve the processing capacity of the large-scale ball mill. Taking a Φ5.49 × 8.83 m ball mill as the research object, the reason for the low processing capacity of the ball mill was explored via process mineralogy, physicochemical analysis, workshop process investigation, and the power consumption …
اقرأ أكثر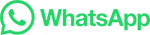
Ball Mills & Agitated Media Mills
Ball Mills and Agitated Media Mills. Grinding wet and dry. Ball mills and agitated media mills can grind extremely fine powders. Hosokawa Alpine mills can achieve a fineness of approx. d97 < 1 μm for both dry grinding and wet grinding. Mills in different designs facilitate either dry or wet grinding. In wet grinding, the powder is mixed into a ...
اقرأ أكثر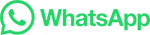
Wet Milling vs Dry Milling: The Differences, Advantages
When the material is pumped through the mill, the mill's components act on the solids in the mixture to tear them apart or crush them, further reducing them in size. The industrial milling process helps to maximize the yield of the mix's ingredients and can improve the resulting product's functionality as well.
اقرأ أكثر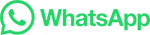
(PDF) Effects of ball-to-powder diameter ratio and powder …
The effects of the ball-to-powder diameter ratio (BPDR) and the shape of the powder particles on EDEM simulation results and time in the planetary ball mill was investigated.
اقرأ أكثر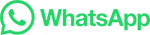
Ball Mills
Ball Mills, Pebble Mills, Material Processing Mills: For more than a century, Patterson has been the industry leading manufacturer of wet and dry grinding mills for size reduction or dispersal. Patterson's ball, pebble and rod mills are built to last. We are still filling parts requests for mills sold over 60 years ago. Patterson mills are available in a wide variety …
اقرأ أكثر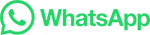
Modelling of the High-Energy Ball Milling Process
High-energy ball milling is a complicated process employed in solid reactions for obtaining nanostructured materials, in powder form, with an average particle size of less than 100 …
اقرأ أكثر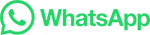
Producing Metal Powder from Machining Chips …
The process of ball milling involves the grinding and mixing of metal particles within a ball mill, which is a type of equipment used for grinding, with the aim of producing a fine powder . This …
اقرأ أكثر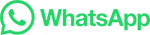
Why the ball to powder ratio (BPR) is insufficient for …
Magnesium hydride powder (ABCR Germany, 98%) was milled in a Fritsh P7 premiumline planetary ball mill. The milling process was performed with different parameters, including the ball and powder mass, total milling time and number of cycles, but the ball to powder ratio (BPR) was kept constant in all cases. The resulting BPR was …
اقرأ أكثر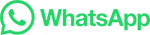
Ball milling: a green technology for the preparation and
See more on pubs.rsc
Ball milling process variables optimization for high-entropy …
WebThe increase in lattice strain and decrease in grain size with milling time can be associated with the increasing total energy transfer during ball milling. In a …
اقرأ أكثر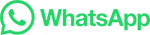
Parametric study on four station ball mill for synthesis of …
The size of the grinding balls used in the ball mill can impact the milling process and the resulting particle size distribution. Changing the ball size can help optimize the milling process. The ratio of balls to powder affects both how the milling works and how good the powder is that comes out of it. By changing the ratio of balls to powder ...
اقرأ أكثر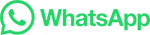
Milling and Mixing | Materials Research Institute
Ball mill is typically used to grind and/or blend materials and it can be done wet or dry. It can be used to mix ceramic powders, disperse particles in solvents, homogenize ceramic slurries, etc. Ball mills operate by rotating …
اقرأ أكثر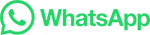
Ball Mill Machines: The Key to Efficient Grinding
A ball mill machine is used to grind and mix materials, producing a finely ground powder suitable for a wide range of applications. At Royal Duyvis Wiener we are specialized in manufacturing ball mill machines for the …
اقرأ أكثر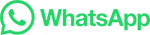
Talcum Powder Production Process
The production process of talcum powder involves several steps, including mining, crushing, drying, milling, and packaging. Here is a general overview of the process: 1. Mining: Talc deposits are typically found in underground or open-pit mines. The ore containing talc is extracted using various mining methods, such as blasting, drilling, or ...
اقرأ أكثر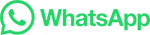
Ball Mill (Ball Mills Explained)
If a ball mill uses little or no water during grinding, it is a 'dry' mill. If a ball mill uses water during grinding, it is a 'wet' mill. A typical ball mill will have a drum length that is 1 or 1.5 times the drum diameter. Ball mills with a …
اقرأ أكثر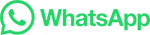
Ball Milling
Ball milling, a shear-force dominant process where the particle size goes on reducing by impact and attrition mainly consists of metallic balls (generally Zirconia (ZrO 2) or steel …
اقرأ أكثر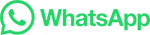
of Mg Powders Processed by High-Energy Ball Milling
Abstract: Commercial powders of pure magnesium were processed by high-energy ball milling. The microstructural and morphological evolution of the powders was …
اقرأ أكثر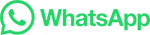
Ball Mill | SpringerLink
First Online: 30 April 2023. 19 Accesses. Download reference work entry PDF. Ball mill is a type of grinding equipment that uses the rotary cylinder to bring the grinding medium and …
اقرأ أكثر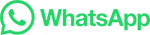
Effects of ball-to-powder diameter ratio and powder particle …
Pulverisette 4 high-energy planetary ball [35] mill produced by the German Fritsch Company was used in the simulation, and this planetary ball mill consists of a supporting disk and two vials, as shown in Fig. 1.Fig. 2 shows the operating principle of the planetary ball mill. 250 mL zirconia vials and 8 mm zirconia balls are used and the …
اقرأ أكثر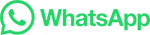
Comparative Study on Improving the Ball Mill Process …
Optimization results confirmed that the balls to powder weight ratio were the most influential process parameter. The optimum process parameters setting concluded …
اقرأ أكثر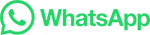
What Are the Parts of a Cement Mills?
A cement mill is a fundamental component of the cement manufacturing process, playing a vital role in breaking down and grinding cement clinker into fine powder. This finely ground powder, when mixed with other materials, produces the building material we commonly know as cement. To achieve this crucial transformation, a cement mill …
اقرأ أكثر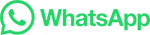
Parameter Optimization of Ball Milling Process for Silica
The results of signal-to-noise analysis obtained the optimum parameter values in a row are: 100 rpm for milling speed parameter, 15: 1 for BPR parameter and 120 minutes for time-miling parameter. The powder size experiment verification of the ball mill process optimization parameter is D50 : 14.99 µm. Export citation and abstract BibTeX RIS.
اقرأ أكثر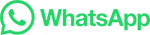
Producing Metal Powder from Machining Chips …
Nevertheless, parameter factors, such as the type of ball milling, ball-to-powder ratio (BPR), rotation speed, grinding period, size and shape of the milling media, and process control agent (PCA ...
اقرأ أكثر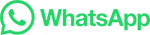
Using a Ball Mill for Black Powder Production: How It Works
Using a ball mill to make mixed black powder is a specific operation, but safety is crucial. Place the media and any other materials in a container. When the container is filled, it is linked to the rolling platform, and the milling process begins. Grinding Process. As the ball mill turns, the balls within it cascade and tumble, grinding the ...
اقرأ أكثر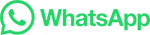
Comparative Study on Improving the Ball Mill Process …
The ball mill process parameters discussed in this study are ball to powder weight ratio, ball mill working capacity and ball mill speed. As Taguchi array, also known as orthogonal array design, adds a new dimension to conventional experimental design, therefore, Orthogonal array (L9) was carefully chosen for experimental design to …
اقرأ أكثر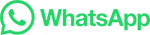
Ball Mills
Ball Mills. In all ore dressing and milling Operations, including flotation, cyanidation, gravity concentration, and amalgamation, the Working Principle is to crush and grind, often with rod mill or ball mill, the ore in order to liberate the minerals. In the chemical and process industries, grinding is an important step in preparing raw ...
اقرأ أكثر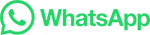