Coke Crusher
Coke Crusher (Rating: ... . Bituminous coal in isolation of air, heated to 950-1050 ℃, after drying, pyrolysis, melting, bonding, solidification and shrink made the final coke, this process is called high-temperature coke (high-temperature dry distillation). ... casting and gasification. The recycled purified coke oven gas is good ...
اقرأ أكثر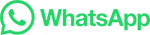
Coking plant | ArcelorMittal
Coke's role in steelmaking is to provide the heat needed to melt the ore, whose natural state is iron oxide, the rust you see on iron after it has been exposed to the atmosphere. Coke …
اقرأ أكثر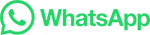
Study of Coal Cake Bulk Density and Its Shear Strength for …
2.4 Bulk Density and Stamping Energy Measurement (Plant Scale). 30 days bulk density measurement trial was carried out at coke plant unit (Battery 11) of Tata Steel (Jamshedpur) in order to report the fluctuation of charging coal cake bulk density under different combination of moisture, crushing fineness (–3.15 mm size fractions) and …
اقرأ أكثر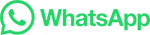
Coke making in Byproduct Coke Oven Batteries – IspatGuru
A byproduct coke oven plant has three main sections namely coal handling plant and coal preparation section, byproduct coke oven batteries with facilities of coke quenching, and coke crushing and sorting plant. Typical process flow and emission streams of a byproduct coke oven plant are shown in Fig 1.
اقرأ أكثر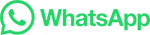
Study of Coal Cake Bulk Density and Its Shear Strength …
of crushing fineness on coal cake bulk density is pre-sented in Fig. 8. The investigation was carried out for coal blend of composition and properties indicated earlier in Tables 1, 2, 3A, B. The experiment was per-formed at constant stamping energy of 450 J/kg based on the hypothesis that coke plant operates at 10% mois-
اقرأ أكثر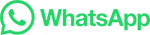
Design, development and installation of a system for …
This causes deterioration of coal crushing and in turn coke quality. Addition of an oil-water emulsion to the coal blend reduces the angle of repose and improves the …
اقرأ أكثر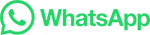
Coke Ovens: Pushing, Quenching and Battery Stacks: …
Coke is used in blast furnaces in the conversion of iron ore to iron, which can be further refined to produce steel. Coke plants produce coke from coal, using coke oven batteries. A battery consists of a group of ovens connected by common walls. The requirements of this rule are based on the equipment and procedures in place at well …
اقرأ أكثر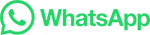
What is the Best Coal for Coke Making
Probably the most satisfactory method of determining the suitability of a coal for making coke of required quality is to make a full-scale oven test in which are maintained the carbonizing conditions under which it is proposed to use the coal. The coke-plant operator ordinarily will use this method as a final check on results of small-oven ...
اقرأ أكثر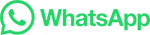
Coke Oven By-Product Plant – IspatGuru
On a typical coke oven and by-product plant, the liquor production rate is around 120 litres/ton (l/t) to 130 l/t of coal carbonized. The flushing liquor supply to the battery is around 4,000 l/t of coal carbonized, depending upon the battery and collecting main arrangement.
اقرأ أكثر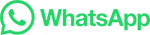
COKE CRUSHING CHARACTERISTICS
influence the production of fines when crushing coke to as low as 3/4-inch top size and that a high hardness value is advantageous. Commercial Oven Cokes Coke crushing characteristics were checked also on 7 samples of chemical and metallurgical cokes produced in commercial plants in both beehive and slot-type ovens.
اقرأ أكثر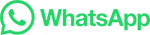
What is a Coke Oven? (with pictures)
A coke oven is a device used to produce coke, a product that is derived from coal. The mixing and heating of bituminous coal at temperatures ranging from around 1832° to 3632°F (1000° to 2,000°C) within the airless oven yields the coke byproduct. This device is a crucial part of the coke-making process. Coke is a solid remainder of ...
اقرأ أكثر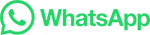
Enhancement of coking potential of coals with improvised …
When compared to hammer mill, CSC processed coal showed improvement in plastic layer thickness (PLT), crucible swelling number (CSN), rank and coke strength …
اقرأ أكثر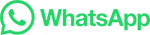
Effect of Coal Size on Coking Pressure and Coke Strength
permeability in the plastic coal layer due to the fine crushing. 2.1.2 Fine crushing of high-coking pressure coal at commercial coke-making plant Based on the findings in the laboratory test, we decreased push-ing loads in testing the fine crushing of high-coking pressure coal at the Kimitsu coke-making plant using a few oven chambers. The ra-
اقرأ أكثر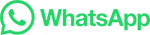
crushing of coal in coke oven plant
Coal crushing plant,Coal crushing production line,Coal crushing ... Coking coal and use of coke: ... volatile constituents are driven off by baking in an oven without oxygen at temperatures ... manufacturer of Coal crushing plant.
اقرأ أكثر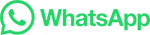
Solved 5. Consider the average daily yields of coke from
Math. Statistics and Probability. Statistics and Probability questions and answers. 5. Consider the average daily yields of coke from coal in a coke oven plant summa- rized by the grouped frequency distribution shown below. Lower Bound Upper Bound Class Midpoint Frequency 67.95 68.95 68.45 1 68.95 69.95 69.45 8 69.95 70.95 70.45 22 70.95 71.95 ...
اقرأ أكثر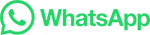
Mechanical compaction of coking coals for carbonization …
used in one of the Polish coking plants. The crushing fineness was 93% below . 3. ... Coke-making technology utilises two systems for charging the coke oven chambers with coal—a stamp-charged ...
اقرأ أكثر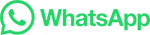
Industrial perspective of the cokemaking technologies
Worldwide, the cokemaking process has remained more or less unchanged for over 100 years, and metallurgical coke is produced in recovery and nonrecovery coke …
اقرأ أكثر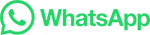
Selection of Coal for inclusion in Coal Blend in Coke Making
In some coke oven plants even a small percentage of non-coking or steam coals have also been used in the blend. Selection of a proper coal blend for use in by product coke ovens is always a big challenge for the coke producer since the blend has to meet the following requirements. It is to meet the requirement of crushing during coal …
اقرأ أكثر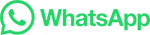
Effect of Coal Size on Coking Pressure and Coke Strength
permeability in the plastic coal layer due to the fine crushing. 2.1.2 Fine crushing of high-coking pressure coal at commercial coke-making plant Based on the findings in the …
اقرأ أكثر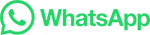
Coke Oven for Tests of Loose and Tamped Coal Batch
If research coke ovens are used at a coke plants, the best conditions of batch preparation (moisture content, degree of crushing, and packing density) may be determined, along with the optimal batch composition containing gas coal and poorly clinkering coal. ... This unit is responsible for crushing of the coal concentrates by …
اقرأ أكثر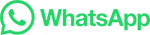
History of Coke
In the next few years, 24 coke ovens were built on the site and a tiny company town of six houses was established. Named "Oklahoma," the settlement housed cokeworkers from the Indiana Coal and Coke Company plant. The beehive ovens at Oklahoma were also destined to undergo several transfers of ownership.
اقرأ أكثر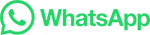
Coking Pressure Control by Selective Crushing of High Coking Pressure Coal
Coal crushing plant. Fig. 10. ... In the case of the wet coal charging process in coke oven chamber, it is known that the coking process is uneven and a local carbonization delay occurs. The ...
اقرأ أكثر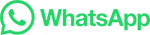
Coke oven gas: Availability, properties, purification, and utilization
Coke is a very strong macro-porous carbonaceous material produced by the carbonization of a specific coal grade or of different coal blends at temperatures ⩾1400 K. Approximately 90% of coke produced from blends of coking coals is used to maintain the iron production process in a blast furnace (BF) [9].
اقرأ أكثر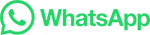
EXECUTIVE SUMMARY
sector, Otto India is offering coke oven plants on turnkey basis based on the design of its German Collaborator. More than 900 ovens have been built/rebuilt by Otto India so far. MECON on the other hand ... selective crushing of coal, partial briquetting of coal, SRC (Solvent refining of coal) with a view to conserve scarce coking
اقرأ أكثر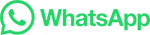
(PDF) A review on stamped charging of coals
Prior to operating a non-recovery coke pilot plant oven, it was essential to ascertain coal cake stability during the loading of a 1 m³ (1 m χ 1 m χ 1 m) coal cake into the cold pilot-plant ...
اقرأ أكثر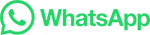
Assessment of thermal efficiency of heat recovery coke making
3.1 Measurement of temperature profile. The evolved gases during carbonization are partially combusted in oven crown and sole flue by introducing controlled amount of air [11, 13–15] in heat recovery coke making.Due to its different heating patterns, the heating rate is not uniform throughout the coal cake [12–14].Also, it is a challenging …
اقرأ أكثر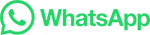
Understanding Coke Making in Byproduct Coke Oven …
A battery consists of 20 to 100 adjacent ovens with common side walls made of high quality silica and other types of refractory bricks. Typically, the individual coke ovens are 11 m to 18.74 m long, 0.35 m to 0.5 m wide, and 3.0 m to 7.4 m high. The wall separating adjacent ovens, as well as each end wall, is made up of a series of heating ...
اقرأ أكثر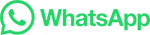
Chemical Technology Prof. Indra D. Mall Department of …
from the coke oven plant, coal tar distillation which is also very important part of the coke oven plant produces tar, benzol, cresotl, phenol and creosote. ... part of coal handling plant. Crushing reduces the overall size of the coal, so that it can be more easily processed and handled during the carbonation process. (Refer Slide Time: 06:40)
اقرأ أكثر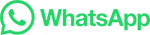
Walthers
The Coke Ovens & Quencher kit includes the crusher, smokestack and quench tower plus long conveyors. These facilities receive coal in hopper cars and bake it in batteries of ovens to yield hotter-burning coke for use in a blast furnace. In-plant hoppers carry the coke away from the ovens.
اقرأ أكثر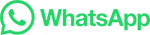
Coke Oven | SpringerLink
In the 1860s, Belgian E. Koppe et al. developed the down draft coke oven (Fig. 2) in which the coking chamber was separated with the combustion chamber.It is also known as the externally heated coke oven, in which the coal gas generated by coal in the coking chamber was introduced into the combustion chamber, and the air was inhaled …
اقرأ أكثر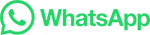