Determination of work index in a common laboratory mill
[Show full abstract] different characteristics of rod mill and ball mill, solving the grinding problem of difficult attrition bauxite. Compared with the traditional one-stage grinding, the power ...
اقرأ أكثر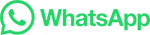
A Comprehensive Guide to Finding the Best Ball Mill for Sale
Cost: Ball mills can range in price from a few thousand dollars up to tens of thousands of dollars. Be sure to consider your budget when shopping for a machine. FAQs Q: What is a ball mill used for? A: Ball mills are used for grinding and mixing materials in a variety of industries, from mining and construction to pharmaceuticals and ceramics.
اقرأ أكثر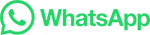
Ball Mill
8.3.2.2 Ball mills. The ball mill is a tumbling mill that uses steel balls as the grinding media. The length of the cylindrical shell is usually 1–1.5 times the shell diameter (Figure 8.11 ). The feed can be dry, with less than 3% moisture to minimize ball coating, or slurry containing 20–40% water by weight.
اقرأ أكثر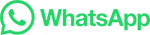
The Importance of Industrial Grinding Equipment in Mining
After mining for material, milling, or grinding, the next step is to make the material into a useable product. Even though industrial grinding equipment has only one purpose—to grind the material into small pieces—a mill can choose from several mill equipment options. Ball Mills. The most common milling machine is the ball mill.
اقرأ أكثر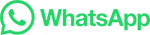
How an Overflow Ball Mill Works?
Ball mill is a common crushing equipment widely used in mining, metallurgy, chemical industry, and other fields. An overflow ball mill is a basic form of ball mill, its main feature is that the feeding port …
اقرأ أكثر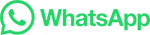
Scale-Up Problems With Large Ball Mills | Mining, …
Analysis of ball and pulp flow in ball mills indicates that three factors may become critical with increasing mill diameters: ball size, fraction critical speed, and average pulp flow velocities. Ball diameters may need to be decreased and fraction critical speeds increased with ores which show decreased breakage rate coefficients above 1.2 mm (14 mesh). …
اقرأ أكثر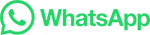
Stirred mills
A switch from ball mills to Vertimill® boosts Miaogou Iron Mine's transformation HIGmill™ fine grinding technology optimizes recovery at Cracow Gold, Australia In 2014, Miaogou Iron Mine launched a technological transformation project, which included replacing the original tertiary ball mills with 's Vertimill
اقرأ أكثر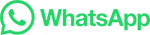
Studies on Scale-Up of Ball Mills | Mining, Metallurgy
Data from ball mills with a wide range of diameters are analyzed using detailed mathematical/numerical models. Analysis shows the relative power inefficiency of large ball mills is due to their inefficient breakage of coarse particles. The models developed can be used to scale-up mill behavior. The behavior of large mills at Bougainville and Pinto …
اقرأ أكثر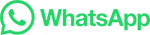
A comparison of wear rates of ball mill grinding media
High chromium white cast iron (HCWCI) is used in mining, crushing plants, as mill liners and in the manufacture of grinding balls. Grinding ball is the essential element in fine fragmentation.
اقرأ أكثر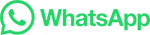
What's the Difference Between SAG Mill and Ball Mill
The biggest characteristic of the sag mill is that the crushing ratio is large. The particle size of the materials to be ground is 300 ~ 400mm, sometimes even larger, and the minimum particle size of the materials to be discharged can reach 0.1 mm. The calculation shows that the crushing ratio can reach 3000 ~ 4000, while the ball mill's ...
اقرأ أكثر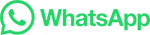
Energies | Free Full-Text | Energy-Efficient Advanced Ultrafine …
The present literature review explores the energy-efficient ultrafine grinding of particles using stirred mills. The review provides an overview of the different techniques for size reduction and the impact of energy requirements on the choice of stirred mills. It also discusses the factors, including the design, operating parameters, and feed material …
اقرأ أكثر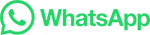
Christian Pfeiffer Ball Mill BAM for Industrial Minerals · …
The BAM ball mill for industrial minerals is designed to be particularly efficient thanks to our process know-how. This is because the efficiency of a mill depends on its internals. All parts of the mill, the diaphragm, the shell lining and the ball charge, have been continuously developed in-house for nearly a century, which is the basis of ...
اقرأ أكثر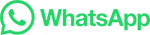
Ball Mill Grinding Machines: Working Principle, Types, Parts
The most common types include: Overflow Ball Mills: These mills have a horizontal cylindrical shell with an outlet at one end. The materials are fed into the mill through the hollow trunnion at the other end. ... Mining and Ore Processing: Ball mills are used for grinding ores and minerals, enabling the extraction of valuable metals. They are ...
اقرأ أكثر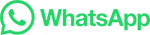
Ball Mill Maintenance & Installation Procedure
Ball Mill Sole Plate. This crown should be between .002″ and . 003″, per foot of length of sole plate. For example, if the sole plate is about 8′ long, the crown should be between .016″ and .024″. Ball Mill Sole Plate. After all shimming is completed, the sole plate and bases should be grouted in position.
اقرأ أكثر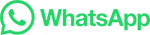
17 Signs of Problems with Ball Mills: Quickly …
Here we list 17 signs to mention you that the ball mill is running and needs to be checked in. Find the abnormal signs early is very important to prolong the ball mill service life. 1. The sign of "swollen …
اقرأ أكثر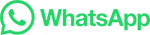
Ball Mills
Ball Mills. Ball mills have been the primary piece of machinery in traditional hard rock grinding circuits for 100+ years. They are proven workhorses, with discharge mesh sizes from ~40M to <200M. Use of a ball mill is the best choice when long term, stationary milling is justified by an operation. Sold individually or as part of our turn-key ...
اقرأ أكثر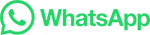
Copper Ball Mill: A Comprehensive Guide
The ball mill is an integral piece of equipment in the copper ore grinding process. The Significance of Copper Ball Mills: Ball mills are cylindrical devices used to grind materials such as ores, chemicals, and ceramics. In the copper mining industry, ball mills are primarily used for grinding copper ores into a fine powder, enabling further ...
اقرأ أكثر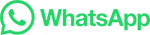
Ball Mill Grinding Theory
The classifier delivered 33 T. of sand per hour. The total ball-mill feed was therefore 40.37 T. per hr. or 550 per cent, of the original feed. Two Stage Grinding. The object of these tests was to determine the capacity of ball-mills when crushing in two stages. The conditions of the test were as follows: First Stage of Ball Milling
اقرأ أكثر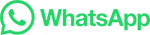
Process Control of Ball Mill Based on MPC-DO
The grinding process of the ball mill is an essential operation in metallurgical concentration plants. Generally, the model of the process is established as a multivariable system characterized with strong coupling and time delay. In previous research, a two-input-two-output model was applied to describe the system, in which some key indicators of the …
اقرأ أكثر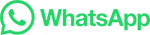
News
The added amount of high-quality steel balls is calculated based on the processing volume per ton of ore (ie 0.8㎏ per ton of ore). Ordinary steel balls need to process one ton of ore (1㎏—1.2㎏). In short, the ratio of steel balls in a ball mill is a more complicated technical issue. Each concentrator must carefully analyze its own actual ...
اقرأ أكثر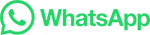
Grinding Mills
Common types of grinding mills include Ball Mills and Rod Mills. This includes all rotating mills with heavy grinding media loads. This article focuses on ball and rod mills excluding SAG and AG mills. ... It is …
اقرأ أكثر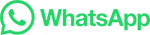
Key Factors for Ball Mill Optimization in the Mining Industry
Successful ball mill optimization in the mining industry requires careful consideration of a range of factors, including mill design, operating conditions, grinding media properties, feed material properties, particle size distribution, and slurry rheology. ... The most common mistakes made during ball mill optimization include poor liner ...
اقرأ أكثر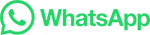
Copper Ball Mill: A Comprehensive Guide
The ball mill is an integral piece of equipment in the copper ore grinding process. The Significance of Copper Ball Mills: Ball mills are cylindrical devices used to grind …
اقرأ أكثر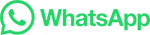
Keys to best practice comminution
An example is Lake Shore Mine, in Timmins, Canada, which used a converted ball mill as a single-stage SAG mill to grind the ore from a feed F 80 of 152 mm to a final cyclone overflow product P 80 of 75 µm, the liberation size recommended for downstream separation. The single stage grinding option should be evaluated for every new project …
اقرأ أكثر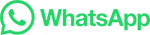
What is the difference between a SAG mill and ball mill?
Principle of SAG Mill operation. SAG is an acronym for semi-autogenous grinding. SAG mills are autogenous mills that also use grinding balls like a ball mill. A SAG mill is usually a primary or first stage grinder. SAG mills use a ball charge of 8 to 21%.[6][7] The largest SAG mill is 42′ (12.8m) in diameter, powered by a 28 MW (38,000 HP ...
اقرأ أكثر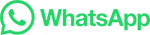
Intelligent optimal control system for ball mill grinding …
The ball mill grinding process is mainly composed of a ball mill, a hydrocyclone cluster, a sump, a slurry pump and an ore bin. The schematic diagram of this process is shown in Fig. 1. Fig. 1 Schematic diagram of ball mill grinding process. The variables of this process shown in Fig. 1 are ex-plained as follows: W
اقرأ أكثر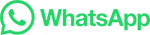
Effect of grinding media on the milling efficiency of a ball mill
The size of grinding media is the primary factor that affects the overall milling efficiency of a ball mill (e.g. power consumption and particle size breakage). This article tackles the lack of a ...
اقرأ أكثر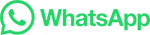
Ball Mill VS AG Mill: What are the Similarities and Differences?
1. Structure. Although the overall structure of autogenous grinding mill and ball mill are similar, but there are differences in details. There are differences in the ratio of the length and width of the barrel between ball mill and AG mill. The large diameter and short length of the barrel of the AG mill reduce the axial segregation of ...
اقرأ أكثر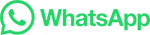
Stirred media mills in the mining industry: Material …
1. Introduction1.1. Fine grinding in the mining industry. It has been estimated that approximately 2% of the world's energy usage is applied to mineral comminution, and around a quarter of this is used specifically in metalliferous ore grinding [1] where it is typically the most energy intensive set of operations [2].The purpose of comminution in …
اقرأ أكثر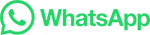