Metal Heat & Surface Treatment | Powder …
A widely used method for painting metal parts, powder coating gives a wide range range of colours. In the process, a dry powder is electrostatically applied to a metal part. The next step is treating the parts …
اقرأ أكثر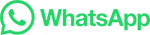
Deposition and characterization of titanium aluminum nitride coatings …
The composition of TiAl target was approximately 50:50 under an atmosphere of argon (99.99990%) as working gas and nitrogen (99.99990%) as reactive gas. Argon and nitrogen were injected into the vacuum chamber in continuous gas flow. ... A comparative research on TiAlN coatings reactively sputtered from powder and from …
اقرأ أكثر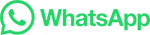
Technology Interchange—Using Nitrogen to Control Variables in Powder
Nitrogen is an inert gas that does not hold moisture. When using only nitrogen gas in a powder application, humidity can be eliminated. ... A Venturi powder pump supplied with compressed air was used to powder coat a 10 ga. steel plate hung on a conveyor set at 8 linear feet per minute. The panel was coated with a Lesta MV6 robot …
اقرأ أكثر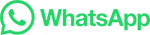
milling powder coating and n2 gas – Grinding Mill China
Aluminum powder (Arno Hahma; Gerald L. Hurst; Tom … If moist air is used, the oxide coating on the Al-particles will be even thicker and the powder … to be powdered in a ball mill … with hydrogen or carbon monoxide gas … » Free Online Chat. Powder Coating Production Equipment – Powder … Nitrogen gas & Chill water: PLC Control ...
اقرأ أكثر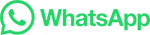
(PDF) EVOLUTION OF TITANIUM POWDER MORPHOLOGY …
Mechanical activation (MA) can be used to obtain nitride phases by grinding titanium in nitrogen [1]. In this work, MA of titanium powder (≤ 100 µm) was performed in an M-3 planetary mill in ...
اقرأ أكثر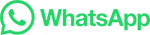
The influence of powder morphology on the microstructure …
The cold spray (CS) technique is a sophisticated additive manufacturing process in which solid metal powder particles (5–100 mm diameter) are accelerated at rates ranging from 600 to 1200 m/s [].The solid-state powders are accelerated by injecting them into a supersonic gas jet created by expanding a preheated and pressurised air, …
اقرأ أكثر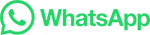
Grinding of Powder Coatings | PCI Magazine
The method does not require the use of a coolant (liquid nitrogen or dry ice), which proves to be an advantage given the cost and safety issues in handling these substances. ... The typical configuration of the ZM 200 for grinding powder coatings is: 12-tooth rotor of stainless steel; distance sieve 1.0 mm, 0.75 mm, 0.5 mm, 0.25 mm or 0.2 …
اقرأ أكثر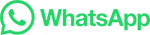
Material Product Data Sheet Polyester Powder
These materials cannot be plasma sprayed using nitrogen/ hydrogen process gases, nor can they be applied using combustion powder Thermospray™ equipment. Coatings of these materials can be finished by machining or grinding. They can be used at service temperatures up to 325 °C (600 °F). Polyester coatings are useful for applications where …
اقرأ أكثر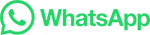
Polifluid
In summary, this system optimises the powder coating operations with a new high-density carrier composed of a mixture of gases contained in the compressed air, modifying their molecular percentages and eliminating all the harmful elements for an optimal application at a constant temperature. It concentrates the nitrogen in the …
اقرأ أكثر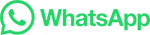
Prevent Combustible Dust Explosions with …
The powders are created by pneumatically conveying plastic pellets into a mill for fine grinding. Particle sizes less than 100µm (140 mesh) are frequently required for coating production. Polyethylene (PE) …
اقرأ أكثر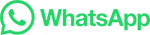
Liquid Nitrogen Cooling Plastic Pulverizer
Liquid nitrogen tank→material solo → machinery grinding machine → draught fan → powder discharging cyclone. Showcase of the liquid nitrogen cryogenic freeze pulverizer machine used more and more in chemical and plastic processing industries: the protecting part can be made from stainless steel 304 or steel coil.
اقرأ أكثر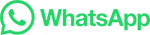
New Cryogrinding System for fine grinding of Plastics
Hosokawa Micron Powder Systems has designed and installed a new system specifically for the size reduction of heat sensitive polymeric materials. The system incorporates state-of-the-art milling and classification equipment and controls allowing for the grinding and classification of a wide range of materials in both fine and coarse applications.
اقرأ أكثر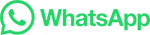
Nitrogen-doped carbon coated zinc as powder-based …
The Nitrogen-doped carbon coating Zinc powders (Zn-NC) were obtained after cooling down. The anode was prepared by mixing the Zn-NC powders, carbon blacks and Poly (vinylidene fluoride) (PVDF) with mass ratio 8:1:1 with N-methylpyrrolidone (NMP) as solvent for grinding to electrode slurry.
اقرأ أكثر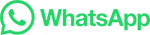
Cryogenics
Liquid. nitrogen (LIN) has been used for more than 30 years in cryogenic grinding to "super-refrigerate" size reduction processes in industries such as food processing, …
اقرأ أكثر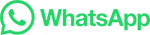
Use Nitrogen Safely
Liquid nitrogen is used in certain particle-size-reduction pro-cesses to super-refrigerate material, including pigments, plastics, powder coatings, waxes, pharmaceuticals, nutraceuticals, spices, and other food products. Liquid nitrogen makes a material more brittle, allowing it to be easily broken up into small particles using less energy ...
اقرأ أكثر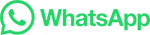
powder coating liquid nitrogen – Grinding Mill China
Cooling Hot Coatings with Nitrogen – PCI Magazine | …. AkzoNobel Powder Coatings to Take Control of South African JV … The atomization of the liquid nitrogen and rapid boil-off is designed to prevent part … » Free Online Chat Air Products — Cooling Hot Coatings with Nitrogen. time and the amount of powder and process gases consumed in the coating …
اقرأ أكثر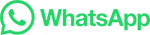
Selecting Cartridge Filters for Powder Coating Operations
BIO John Walz is the manager of the powder coating and dust collection division at Chemco Manufacturing Co. in Northbrook, Ill., a major filter manufacturer in the finishing and dust collection industries. For more information on the new "dual dimple" polyester powder cartridges, call (800) 323-0431, ext 199.
اقرأ أكثر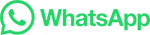
to compare grinding technology systems to determine …
nitrogen (LIN), it becomes more brittle and can be broken up more easily into small particles using less energy. The same technology also has been widely used in the …
اقرأ أكثر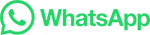
PolarFit™ Ultra-Fine-Grinding Mill
of liquid nitrogen Our ultra-fine-grinding system uses the cooling power of liquid nitrogen to remove heat produced in the grinding process by controlling the temperature of your product or the mill. Key benefits include the following: • Ultra-fine particle size • More uniform particle distribution • Higher yields of particles in your
اقرأ أكثر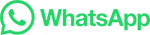
PolarFit™ Ultra-Fine-Grinding Mill
of liquid nitrogen Our ultra-fine-grinding system uses the cooling power of liquid nitrogen to remove heat produced in the grinding process by controlling the temperature of your …
اقرأ أكثر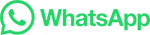
Preparation of epoxy coatings by plasma-electrostatic …
Electrostatic spraying has a certain requirement for the resistivity of the sprayed plastic powder due to its process and principle. A powder with a resistance that is too low will lead to powder redispersion, and a powder with a resistance that is too high will affect the thickness of the coating. 15,16 Additionally, coatings prepared by the …
اقرأ أكثر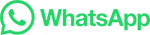
Proper Grounding Techniques for Powder Coating
Permanently attach a ground strap of at least a 14-gauge wire with a good clamp on the end that will be used to ground parts. When the ground rod is in rather sandy or dry soil, a small amount of water can be poured into the grounding rod hole and allowed to soak in prior to powder coating. For the best ground, make sure your clamp (left) is ...
اقرأ أكثر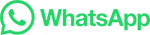
Grinding of Powder Coatings | PCI Magazine
The method does not require the use of a coolant (liquid nitrogen or dry ice), which proves to be an advantage given the cost and safety issues in handling these …
اقرأ أكثر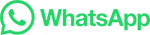
Effect of Moisture Content on the Grinding Process and Powder …
Grinding is a staple size-reduction process to produce food powders in which the powdered form is chemically and microbiologically stable and convenient to use as end products or intermediate products. The moisture content of food materials before grinding is a particularly important factor, since it determines the materials' physical properties and …
اقرأ أكثر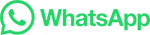
Powder Coating Grinding Nitrogen
poder coting grending grinding nitrogen coating - ngena-ds.co.za. powder coating grinding nitrogen manufacturer in Shanghai, China powder coating grinding nitrogen is manufactured from Shanghai Xuanshi,It is the main mineral . Problem - Powder Coating ExpertsIs there any way to remove the oxide coating from the laser cut edge besides …
اقرأ أكثر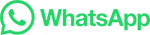
Outgassing in Powder Coatings > Powder Coated Tough …
1. Castings: Outgassing can occur when a powder coating is applied over a cast metal surface (iron, steel, aluminum, brass, etc.). Gasses are entrapped into the casting material during the pouring process of both sand and die type castings. These gasses can be anything from entrapped air to gas formed during the cooling of the molten metal.
اقرأ أكثر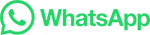
Particle Size Reduction | Disputanta VA | Ancos
Particle size reduction, or grinding, is a process to produce a polymer powder necessary for a particular industry or technology. This can be accomplished by starting with resin pellets or a powder that is ground to …
اقرأ أكثر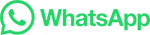
Powder Coating Grinding Nitrogen
I am trying to grind PET into powder using PET powder grinder and liquid nitrogen. May I know the required liquid nitrogen amount for 20-30 g of PET samples? ... Apr 24, 2022 · Grinding of Powder Coatings November 1 preferably in a small laboratory mill in order to produce a fine powder with a Ultrasonic Deblinding System Improves Know More ...
اقرأ أكثر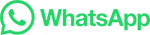
Prevent Combustible Dust Explosions with Nitrogen Inerting
The powders are created by pneumatically conveying plastic pellets into a mill for fine grinding. Particle sizes less than 100µm (140 mesh) are frequently required for coating production. Polyethylene (PE) is the most common plastic used in powder coating manufacturing, but polyvinylchloride, polyester and polyurethane compounds are also …
اقرأ أكثر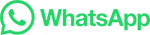
#11 Particle Size Distribution
Powder coatings are an assortment of various sized particles produced in a grinding process. The size of powder particles have a major influence on many properties including fluidity, charging, application, and the final film appearance. Figure 2: Packing Efficiency DIAMOND VOGEL | 1019 ARIZONA PLACE SW | phone 712.737.4993 | fax 712.737.4997
اقرأ أكثر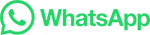