Grinding ball data
ResultChemical composition of test grinding balls listed in table 7.5.1. (see table 7.5.2.). ... Wear rates of grinding media and mill liners of the Soviet cement industry (see table 7.7.7.1.). ... Dettmer claims that with increasing mill diame ter, the mill liner wear per ton of mill feed decreases. This statement is expressed by the above ...
اقرأ أكثر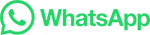
Cement Analysis and Production Information
ResultThese additives, along with the limestone, are fed from bins to the raw mill. An extremely important step in the cement process is to proportionally feed these materials to the raw mill to ensure the correct "blend" of these materials. One can think of this process as a "recipe" for making various types of cement.
اقرأ أكثر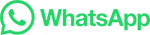
NEW Cooperative Invests in Huge New Feed Mill For …
ResultThe mill has been manufacturing feed since February 2017. The slipform concrete mill tower stands on a 42-foot-x-95-foot footprint, not including warehouse space, two loading bays and a receiving/grinder building that can receive ingredients at 12,500 cubic feet per hour. Ancillary buildings are of concrete tilt panel construction.
اقرأ أكثر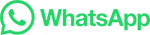
Vertical Cement Mill | Magotteaux
ResultMagotteaux's proprietary vertical cement mill technology has been developed through decades of innovation and expertise in grinding processes. Our vertical cement mills are designed to provide optimal grinding efficiency, quality, and reliability for cement production. Our systems and parts are like no other, thanks …
اقرأ أكثر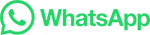
Effect of Feed Amount and Composition on Blaine and Residue in Cement Mill
ResultThis study investigates the effect of the amount and composition of cement ball mill feed on Blaine fineness and cement residue. The collected data were obtained using a ball mill for grinding clinker and additive materials (pozzolana and gypsum) at different amounts and composition of feed. The fineness of cement was …
اقرأ أكثر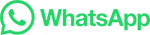
Effect of Feed Amount and Composition On Blaine and …
ResultEffect of Feed Amount and Composition on Blaine and Residue in Ce - Free download as PDF File (.pdf), Text File (.txt) or read online for free.
اقرأ أكثر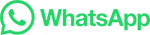
EVERYTHING YOU NEED TO KNOW ABOUT THE CHEMISTRY …
The basic ingredients for portland cement consist of limestone, sea shells, marl, or chalk, that provide the calcareous components; clay, shale, slate, or sand, to provide the silica and alumina; and iron ore, mill scale, or similar material to provide the iron components. The number of raw materials required at any one pl…See more on cementequipment
Explore further
Kiln fuel mix of the clinker production process under study.researchgateCalculation of the formation process of clinker inside the …researchgateRecommended to you based on what's popular • FeedbackEffect of Feed Amount and Composition on Blaine and …
Web ResultThis study investigates the effect of the amount and composition of cement ball mill feed on Blaine fineness and cement residue. The collected data were obtained …
اقرأ أكثر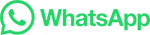
Raw milling and blending
ResultContinuous blending involves simultaneous feeding of the silo, overflow to a second silo and final discharge to kiln feed. Modern equipment generally uses continuous CF silos, each having capacity of more than 24-hours' kiln feed and yielding a blending ratio (or 'blending factor') of 4-8, or around 2-3 for older silos.
اقرأ أكثر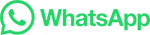
Better and cheaper cement: Optimising the right clinker …
ResultClinker mineralogy and nodule size depend largely on the feed composition and the amount, distribution and nature of the melt phase formed in the burning zone. The clinker melt promotes the reaction between belite (C 2 S) and free lime to form alite (C 3 S), so it is critical for clinker reactivity. The melt also binds …
اقرأ أكثر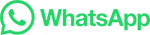
Review on vertical roller mill in cement industry & its …
ResultExtracted cooled clinker and other additives like gypsum, fly ash etc. are fed to the cement mill in a controlled manner in specific quantity. The cement …
اقرأ أكثر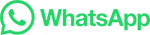
What are factors that will affect the output of a cement mill?
ResultThere are several factors that can affect the output of a cement mill, including: Feed rate and composition: The feed rate of the material into the mill, as well as its chemical composition, can ...
اقرأ أكثر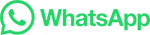
The Decision Algorithm of Cement Mill Operation Index …
ResultAbstract An improved differential evolutionary cement mill operation index decision algorithm based on constraint control and selection strategy is proposed to address the problem that the operation index is usually decided by manual experience in the cement mill operation process, which causes …
اقرأ أكثر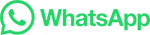
Composition of cement
ResultPortland cement is manufactured by crushing, milling and proportioning the following materials: Lime or calcium oxide, CaO: from limestone, chalk, shells, shale or calcareous rock. Silica, SiO 2: from sand, old bottles, clay or argillaceous rock. Alumina, Al 2 O 3: from bauxite, recycled aluminum, clay. Iron, Fe 2 O 3: from …
اقرأ أكثر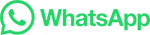
Optimization of Cement Manufacturing Process
ResultAbstract. Cement manufacturing process is now operated with the aid of various control systems, such as raw meal composition control, kiln control …
اقرأ أكثر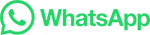
HOMOGENIZATION STRATEGY IN THE CEMENT …
ResultCement clinkering process demands specific chemistry consistency of the kiln feed and for a ... the average kiln feed composition. Some strategic steps to be considered are listed below. ... consideration is to minimize the deviation in - the composition. This is done by installing an online analyzer on the mill feed belt, …
اقرأ أكثر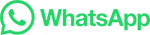
Cost-efficient strategies for sustainable cement production
ResultThe robust control of cement composition safeguards key cement performance characteristics such as strength. Such control begins at the quarry and extends …
اقرأ أكثر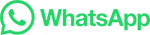
HOMOGENIZATION STRATEGY IN THE CEMENT …
Result• The singlemost important consideration is to minimize the deviation in - the composition. This is done by installing an online analyzer on the mill feed belt, …
اقرأ أكثر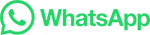
Review on vertical roller mill in cement industry & its …
ResultThe cement mill is either a Ball mill with two chambers or Vertical roller mill with inbuilt classifier. Material is ground till desired Blaine is achieved and then final product is stored in concrete silos for further blending. ... Mill feed size can normally be reduced by adjustment of bars on the crusher, or fitting a screen with …
اقرأ أكثر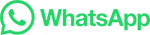
Fundamentals of Cement Chemistry, Operations, and Quality …
ResultA 33-grade cement concrete mortar made with cement, water, and sand in the ratio of 1:1:3 cured for 28 days under controlled conditions achieves a minimum compressive strength of 33 N/mm 2. A 33-grade cement is used in plain cement concrete (PCC) where it is not subjected to stress. It complies with the …
اقرأ أكثر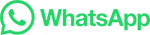
Cement Manufacturing Process
ResultKiln Feed Chemical Composition The primary goal when designing kiln feed chemistry must be to produce a clinker that when ground with appropriate additives produces a marketable product. …
اقرأ أكثر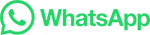
Ball mill for cement grinding
ResultThe ultimate ball mill – with flexibility built in. You can't optimise cement grinding with a one-size-fits-all solution. That's why our ball mills are designed to adapt to your requirements, with a high degree of flexibility built in. You decide whether to operate the mill in open or closed circuit, with or without a pre-grinder and with ...
اقرأ أكثر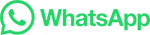
OPTIMIZATION OF CEMENT GRINDING OPERATION IN …
ResultClinker, Gypsum and other desired additives are fed to the ball mill in specific proportions based on the quality requirement. Feed material is ground in the ball …
اقرأ أكثر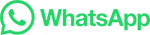
Analysis of material flow and consumption in cement
ResultIn the surveyed cement plant, three balances are established between input and output material in the raw mill, clinker production, and cement grinding system. 2.48 t, 4.69 t, and 3.41 t of materials are required to produce a ton of the product in raw material preparation, clinker production, and cement grinding …
اقرأ أكثر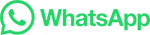
Everything you need to know about Kiln System Operations …
ResultKiln feed chemical composition has a large effect on kiln operations. Several of the more impor-tant parameters are silica ratio, percent liquid, and C3S content (or …
اقرأ أكثر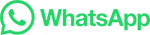
From raw materials to 8 steps of cement manufacturing, …
ResultRaw Mix Proportioning and Raw Mix Design of cement. The raw materials mixture is called raw mix or raw meal or kiln feed, The continuous production of high-quality cement is possible only if the raw mix possesses optimum composition, The purpose of calculating the composition of the raw mix is to …
اقرأ أكثر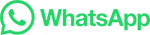
Effects and Control of Chemical Composition of …
ResultAbstract. This research focused the role to study the effects and ways to control the chemical composition of clinker for better cement production. Cement is a substance produced by …
اقرأ أكثر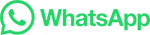
Butterball Builds Large-Scale Slipform Concrete …
ResultThe freight cost would be prohibitive," says Dr. Vernon Felts, senior director of live production. Instead, Butterball decided to consolidate the two steel mills into a single large slipform concrete mill. The …
اقرأ أكثر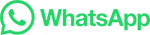
The Cement Manufacturing Process
ResultThe clinker is ground to a fine powder in a cement mill and mixed with gypsum to create cement. The powdered cement is then mixed with water and aggregates to form concrete that is used in construction. Clinker quality depends on raw material composition, which has to be closely monitored to ensure the …
اقرأ أكثر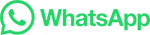
Everything you need to know about clinker/cement Grinding
ResultFor a cement mill: intermediate or outlet diaphragm. For the case of; cement mills with a drying chamber see raw mills. Mill working conditions: ventilation air speed through the mill. Bigger or smaller than 1.2 [m/s]. Material abrasivity. The [%] of slag or pouzzolana content on the fresh mill feed for cement grinding.
اقرأ أكثر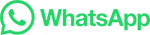