Replacement of Wet Ball Milling with High-Pressure …
In response to the Natural Resources Canada "Crush It Challenge," Corem partnered with the University of British Columbia and led a project to develop and demonstrate the use of high-pressure grinding to replace the workhorse of the industry, wet ball milling. Two plant case studies, a small tonnage gold recovery operation and a large …
اقرأ أكثر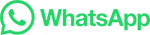
Effect of ball size and powder loading on the milling efficiency …
1. Introduction. Wet ball mill is one of the most predominantly used method for the purpose of mixing and grinding of raw materials in laboratories and industry [1], [2], [3].The ball mill process is very complicated process governed by many parameters, such as ball size, ball shape, ball filling, slurry loading (with respect to ball amount), powder …
اقرأ أكثر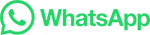
Ball mill, Ball grinding mill
ball grinding mill Ф2200×5500. horizontal for ore for cement. Final grain size: 74 µm - 400 µm. Rotational speed: 21 rpm. Output: 10 t/h - 20 t/h. Ball mill is common used grinding plant in the industry, and it is key …
اقرأ أكثر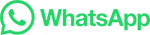
One‑pot wet ball‑milling for waste wire‑harness …
Conclusion. Herein, we described the development of a wire-harness recycling technique. The process involves the simultane-ous extraction of a plasticizer and the removal of the PVC coating from Cu wires by the physical impact of balls in the presence of a solvent, constituting a one-pot wet ball-milling method.
اقرأ أكثر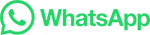
One-pot wet ball-milling for waste wire-harness recycling
The wet ball-milling tests were conducted at different rotating speeds (20, 25, 35, and 45 rpm) using the 20-mm balls. Figure 7a shows the wet ball-milling separation results in n-butyl acetate. Complete separations are achieved within 90, 70, 60, and 50 min of wet ball milling at rotating speeds of 20, 25, 35, and 45 rpm, respectively.
اقرأ أكثر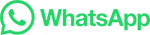
Ball-impact energy analysis of wet tumbling mill using a …
A modified three-dimensional quasi-wet discrete element method (DEM), which is constructed by adding the drag force and buoyancy and the velocity dependence …
اقرأ أكثر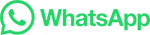
Dry Grinding Vs. Wet Ball Mill Grinding | Economy Ball Mill
Dry ball milling requires less energy than wet ball milling but has a lower throughput. Wet ball milling requires more energy than dry ball milling but also has higher throughput. . Dry ball milling is more efficient for materials that don't require very fine particles or have a low tendency to group together.
اقرأ أكثر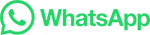
(PDF) DESIGN AND FABRICATION OF MINI BALL …
The ultimate crystalline size of graphite, estimated by the Raman intensity ratio, of 2.5 nm for the agate ball-mill is smaller than that of 3.5 nm for the stainless ball-mill, while the milling ...
اقرأ أكثر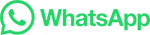
Wet ball milling of niobium by using ethanol, determination …
6 Citations. Metrics. Abstract. This study investigates the effect of using ethanol as the process control agent during the wet ball milling of niobium (Nb). Dried …
اقرأ أكثر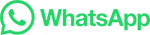
Ball Mills
CERAMIC LINED BALL MILL. Ball Mills can be supplied with either ceramic or rubber linings for wet or dry grinding, for continuous or batch type operation, in sizes from 15″ x 21″ to 8′ x 12′. High density ceramic linings of uniform hardness male possible thinner linings and greater and more effective grinding volume.
اقرأ أكثر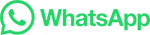
Ball Mill
Mechanical Crushing and Grinding. Oleg D. Neikov, in Handbook of Non-Ferrous Metal Powders (Second Edition), 2019 Tumbling Ball Mills. Tumbling ball mills or ball mills are most widely used in both wet and dry systems, in batch and continuous operations, and on small and large scales.. Grinding elements in ball mills travel at different velocities. …
اقرأ أكثر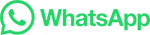
Modeling of Bauxite Ore Wet Milling for the Improvement …
Size reduction is a necessary operation in mineral processing plants and provides the desired size for separation operations and the liberation of the valuable minerals present in ores. Estimations on energy consumption indicate that milling consumes more than 50 % of the total energy used in mining operations. Despite the fact …
اقرأ أكثر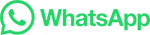
Dry Grinding Vs. Wet Ball Mill Grinding | Economy Ball Mill
We Service Internationally! Dry Ball Mill Grinding Vs. Wet Ball Mill Grinding. JSB Industrial Solutions • Sep 15, 2023. Dry grinding and wet grinding are two different …
اقرأ أكثر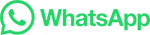
Ball Mill | Ball Mills | Wet & Dry Grinding | DOVE
DOVE small Ball Mills designed for laboratories ball milling process are supplied in 4 models, capacity range of (200g/h-1000 g/h). For small to large scale operations, DOVE Ball Mills are supplied in 17 models, capacity range of (0.3 TPH – 80 TPH). With over 50 years experience in Grinding Mill Machine fabrication, DOVE Ball Mills as ...
اقرأ أكثر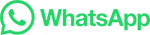
How Ball Mills Contribute to Battery Technology
In this article, the four main application areas of Retsch laboratory ball mills in battery technology will be outlined. Each area can be categorized under specific application examples: Section 1: Reduction of the material particle size in batteries. Section 2: Mixing and coating of particles.
اقرأ أكثر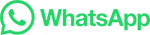
The Ultimate Guide to Ball Mills
• Edge driving ball mill: the motor drives the gear on the edge of the cylinder through the reducer to drive the cylinder movement. 6. According to the operation characteristics of ball mill: • Wet ball mill: Adding water when feeding, the discharging material is discharged when it is in a certain concentration of slurry. The wet ball mill ...
اقرأ أكثر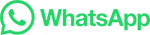
Ball Grinding Process | SpringerLink
Ball grinding can be carried out in either dry-operation or wet-operation. The former is widely used in coal-fired power plants and cement industry, and the latter is widely used in metal and nonmetal mines. There are three types of mills used: grate ball mill, overflow ball mill, and peripheral discharge ball mill.
اقرأ أكثر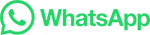
Ball Mill Loading
The starting point for ball mill media and liquid charging is generally as follows: 50% media charge. Assuming 26% void space between spherical balls (non-spherical, irregularly shaped and mixed-size media will increase or decrease the free space) 50% x 26% = 13% free space. Add to this another 45% to 50% above the ball charge for total of 58% ...
اقرأ أكثر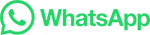
Wet Milling vs Dry Milling: The Differences, Advantages, and Challenges
Wet milling, also known as wet grinding, is a process through which particles that are suspended in a liquid slurry are dispersed in that liquid by shearing or crushing. Once the milling process is complete, these particles are ready for use or can be dried and separated for incorporation into additional products. Wet milling is more complex ...
اقرأ أكثر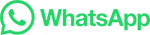
TECHNICAL SPECIFICATION OF WET BALL MILL …
The Gravimetric feeder feeds limestone to Wet ball mill system. The Wet Ball Mill system consists of Wet Ball Mill, Wet Ball Mill Lubrication system, Mill circuit tank with an agitator, Mill circuit Pump, Mill Hydro cyclone, 3-way distributor and accessories. The Wet Ball Mill is the wet horizontal type. The Process water is supplied to Wet ...
اقرأ أكثر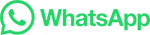
Wet ball milling of niobium by using ethanol, determination …
This study investigates the effect of using ethanol as the process control agent during the wet ball milling of niobium (Nb). Dried nanocrystal Nb powders, of high purity, with particle sizes ...
اقرأ أكثر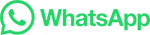
Planetary Ball Mill PM 100
The Planetary Ball Mill PM 100 is a powerful benchtop model with a single grinding station and an easy-to-use counterweight which compensates masses up to 8 kg. It allows for grinding up to 220 ml sample material per batch. The extremely high centrifugal forces of Planetary Ball Mills result in very high pulverization energy and therefore short ...
اقرأ أكثر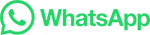
Wet Ball Mill for Metal Ores and Non-ferrous Metals Wet …
Buy wet ball mill from trusted wet grinding ball mill supplier. Energy saving wet ball mill, small energy consumption, large productivity, effectively improving grinding efficiency.
اقرأ أكثر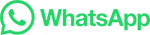
4x1000ml Gear-Drive 4-Liter Planetary Ball Mill
They are the ideal wet/dry milling tools for acquiring research samples with high efficiency and low noise. Vacuum jars may be used to process sample within a vacuum environment. PQ-N4 planetary ball mills have four grinding stations arranged on the "Sun Wheel" of the planetary ball mill. When the Sun Wheel rotates, the grinding balls inside ...
اقرأ أكثر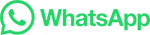
A method to identify wet ball mill's load based on
In this paper, a novel method of wet ball mill load identification based on CEEMDAN, RCMDE and SRNN is proposed. Firstly, CEEMDAN-RCMDE is used to extract the load features of the ball mill. Then, taking the advantage of SRNN's fast training speed and strong generalization ability, a mill load identification model based on SRNN is …
اقرأ أكثر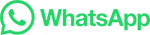
What is the Principle of Wet Ball Mill?
The principle of wet ball milling is based on the energy transfer between the grinding media and the material being ground. In the process of wet ball milling, the grinding media are typically made of steel or ceramics, and they are loaded into the mill in a specific proportion. As the cylinder rotates, the grinding media and the material being ...
اقرأ أكثر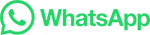
wet ball mill ball malaysia
Wet Ball Mills In Malaysia - marietvanderzande.nl 2.4. wet ball milling only biochar from pyrolysis temperature of 400 and 500 c with pyrolysis time of 30 and 60 minutes were chosen to proceed with wet ball milling process. deionized water was mixed with the biochar to produce 50 wt.% of biochar dispersion. mill jar of 2.5 liters capacity was used …
اقرأ أكثر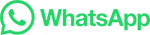
Ball Mill | SpringerLink
Peripheral discharge ball mill, and the products are discharged through the discharge port around the cylinder. According to the ratio of cylinder length (L) to diameter (D), the ball mill can be divided into short cylinder ball mill, L/D ≤ 1; long barrel ball mill, L/D ≥ 1–1.5 or even 2–3; and tube mill, L/D ≥ 3–5. According to the ...
اقرأ أكثر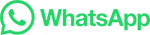
Chapter 1 – Soils Tex-116-E, Ball Mill Method for …
The result of this test is known as the Wet Ball Mill (WBM) value. Apparatus The following apparatus is required: ♦ wet ball mill machine, consisting of a watertight steel cylinder, closed at one end, with inside dimensions of 258.8 ± 3 mm (10.188 ± 1/8 in.) in diameter and 273.1 ± 3 mm (10.75 ± 1/8 in.) in length.
اقرأ أكثر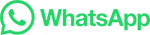
Pharmaceutical nanocrystals: production by wet milling …
Wet milling using planetary ball mills has been successfully used to produce nanosuspensions for drugs such as indometacin and brinzolamide 45, 58. Based on the principle of planetary ball milling, Juhnke et al. [59] developed a screening media mill equipped with up to 24 milling beakers of 0.05–1.0-ml individual milling chamber …
اقرأ أكثر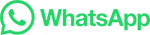