Quality requirements of iron ore for iron production
As shown in Figure 16.1, world DRI production has seen constant growth since 1980 and reached over 75.2 million tonnes in 2013.Among the various DRI processes, MIDREX® dominates the market accounting for almost 63.2% of the total DRI production in 2013, followed by 21.2% for coal-based processes and 15.4% from the HYL/Energiron …
اقرأ أكثر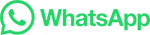
Beneficiation of Fine Iron Ores using the Desand Process
The desand process is designed to treat the -1.0 mm range from -8.0 mm natural fines, to recover a -1.0 +0.038 mm higher-grade fraction by rejecting to tailings any low-grade clay-rich ultrafines and low density sand-size fine chert/quartz gangue and shale.The desand process consists of wet screens with a nominal 0.7-1.0 mm cut point which ...
اقرأ أكثر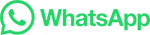
Iron Ore Sintering: Process: Mineral Processing and …
Sintering is a thermal agglomeration process that is applied to a mixture of iron ore fines, recycled ironmaking products, fluxes, slag-forming agents, and solid fuel (coke). The purpose of the sintering process is manufacturing a product with the suitable characteristics (thermal, mechanical, physical and chemical) to be fed to the blast furnace.
اقرأ أكثر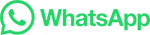
(PDF) Iron Ore Sintering: Process
Sintering is an agglomeration process that fuses iron ore fines, fluxes, recycled products, slag-forming elements and coke. The purpose of sintering is to obtain a product with suitable ...
اقرأ أكثر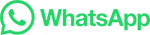
Iron ore beneficiation: an overview
Mineral Processing. Beneficiation Operations and Process Optimization Through Modeling. 2023, Pages 55-77. Chapter 2 - Iron ore beneficiation: an overview. …
اقرأ أكثر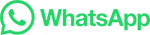
Iron Ore Processing, General | SpringerLink
First Online: 20 October 2022. 215 Accesses. Abstract. Iron ore resource has its own peculiar mineral characteristics requiring suitable processing or beneficiation to produce …
اقرأ أكثر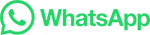
Iron processing | Definition, History, Steps, Uses, & Facts
Iron ore sintering consists of heating a layer of fines until partial melting occurs and individual ore particles fuse together. For this purpose, a traveling-grate machine is used, …
اقرأ أكثر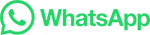
Iron ore mining and dressing
An ironworks (or iron works) is an industrial plant for the production of steel from iron ores! Before the iron ores can be fed to the ironworks, they must first be mined (ore extraction) and specially processed for the blast furnace process (ore processing). These process steps are described in more detail in the following sections.
اقرأ أكثر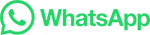
Optimization of carbon deposition process during the
2.2. Experimental procedure. For the pre-reduction process, 8.00 g iron ore were first heated at 500 °C in the fluidized bed reactor with the protection of 1.0 L/min N 2.After maintaining the system at 500 °C for 5 min, N 2 was switched to 1.5 L/min CO–H 2 gas mixture for pre-reduction and carbon deposition. When the desired time was …
اقرأ أكثر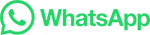
Iron Ore Sintering: Process: Mineral Processing and Extractive
Sintering is a thermal agglomeration process that is applied to a mixture of iron ore fines, recycled ironmaking products, fluxes, slag-forming agents, and solid fuel …
اقرأ أكثر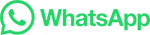
From Ore to Iron with Smelting and Direct Iron Reduction
Smelting Reduction. Figure 2: The smelt reduction vessel (SRV) is the core technology component of the Hismelt process. Source: RioTinto While years of ironmaking technology innovations have optimized blast furnace productivity, two alternative processes—smelting reduction and direct iron reduction— are growing in adoption. The …
اقرأ أكثر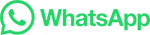
Hematite: A primary ore of iron and a pigment …
Hematite is the world's most important ore of iron. Although magnetite contains a higher percentage of iron and is easier to process, hematite is the leading ore because it is more abundant and present in deposits in …
اقرأ أكثر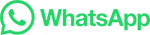
Fine Iron Ore Separation | ST Equipment & Technology LLC
Consider what just a small percent increase in iron ore recovery from the same materials that are currently being mined and processed would mean to a company's bottom line, especially considering that a large percentage of fine iron ore particles are currently going into a waste stream.
اقرأ أكثر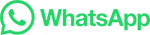
Fluidized-bed technology for the T production of iron …
the direct use of iron-ore fines and non-coking coals. The FINMET ®process is a direct-reduction process based on the direct use of iron-ore fines and natural gas as reductant. The key technology for both processes is a four-stage, bubbling, fluidized-bed reactor system where fine iron ore is reduced to
اقرأ أكثر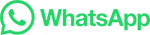
Comminution and classification technologies of iron ore
Most of the high-grade hematite iron ores are typically subjected to simple dry processes of crushing and classification to meet the size specifications required for direct shipping ore (DSO). This involves multistages of crushing and screening to obtain lump (−31.5 + 6.3 mm) and fines (approximately −6.3 mm) products.
اقرأ أكثر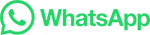
Mineral Processing | SpringerLink
For example, the average iron grade of the iron ores in China is only around 33%, but the iron ore grade required for blast furnace smelting is at least 60% or even above 65%; the average copper grade of copper ore resources is 0.87%, while the copper ore grade required for copper smelting plant is usually 20%, and the Grade 5 copper ore, …
اقرأ أكثر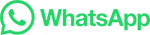
Recent practices in mine tailings' recycling and reuse
With the increase in situational awareness and environmental perception in recent years, more effective management of mine tailings has become necessary. 13.5. Recycling and reuse: recent approaches. Nowadays, the development of societies is based on limited fossil fuels and mineral deposits.
اقرأ أكثر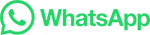
[PDF] Iron Ore Agglomeration Technologies | Semantic Scholar
Until the 1950s of the last century, the oxidized iron ores that were loaded into the blast furnace had granulometries within 10 and 120 mm. However, the depletion of high-grade iron ore sources has made necessary the utilization of concentration processes with the purpose of enriching the iron ore. Because of these processes, a fine …
اقرأ أكثر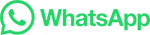
The Sintering Process of Iron Ore Fines – IspatGuru
The process of sintering is basically a pre-treatment process step during iron making for the production of the charge material called sinter for the blast furnace from iron ore fines and also from metallurgical …
اقرأ أكثر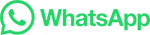
Iron Ore Agglomeration Technologies | IntechOpen
Briquetting is the simplest agglomeration process. Fine grained iron ore is pressed into two pockets with the addition of water or some other binder agent (molasses, starch, or tar pitch) ... (1300–1400°C) by which a mixture of iron ore, return fines, recycled products of the iron and steel industry (mill scale, blast furnace dusts, etc.), ...
اقرأ أكثر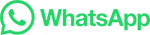
Iron ore | Anglo American – Kumba Iron Ore
These iron ore reserves are all of high quality Hematite allowing us to produce both high quality lump (64.0%Fe) and high grade sinter fines (63.5%Fe) for the domestic and export markets. We are unique in that we are primarily a principle lump producer with a product of recognized exceptional chemical and metallurgical quality.
اقرأ أكثر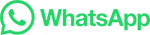
(PDF) IRON ORE PELLETIZING PROCESS
As greater amounts of fine iron ore concentrates enter the marketplace, new investments in iron ore pelletizing capacity are inevitable to deliver these concentrates to steel industry consumers.
اقرأ أكثر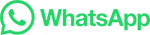
Mechanical properties and hydration mechanism of high-volume ultra-fine
To obtain ultra-fine particles, IOT was processed via grinding in water, and the particle characteristics were characterized using a laser particle-size analyzer, scanning electron microscope (SEM), Fourier transform infrared spectroscopy (FT-IR) and inductively coupled plasma (ICP). ... Iron ore tailings (IOT) ... Particularly in an ultra-fine ...
اقرأ أكثر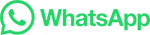
Iron ore beneficiation | Commodities | Mineral Technologies
Our solutions. Latest news. Zero Harm. Delivering solutions for fine iron ore beneficiation. The world's largest producers rely on Mineral Technologies for iron ore processing …
اقرأ أكثر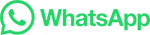
World leader in fine iron ore beneficiation
Optimising metallurgical recovery and grade for fine iron ore. Helping to deliver your project vision, we provide core services from early analysis through to complete metallurgically …
اقرأ أكثر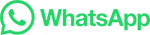
Mineral Magnetic Modification of Fine Iron Ore Tailings and …
In this paper, the properties, mineral magnetic modification, and beneficiation of tailings from the central mining and processing plant in Kryvyi Rih, Ukraine, have been studied. Samples were investigated by X-ray diffraction, X-ray fluorescence, microscopy, and magnetization measurements. The beneficiation was conducted using magnetizing …
اقرأ أكثر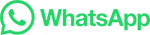
From Ore to Iron with Smelting and Direct Iron …
In the smelting reduction process, pelletized iron oxide ore or fine ore powders are pre-reduced in a fluidized bed or reduction shaft. The reduced iron along with coal and lime is fed to a gasifier-melter, …
اقرأ أكثر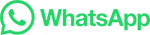
Iron ore beneficiation: an overview
Dry processing of iron ore: In dry processing of iron ore, ROM is generally crushed below 40 mm through three-stage crushing and thus segregated by screening into 10–40 and −10 mm fractions. For softer ore, tumbler index is generally low and hence lump ore is crushed below 10 mm to produce fine product. Yield from the plants has …
اقرأ أكثر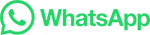
Manufacturing Process From Ore To Stainless Steel: A Step …
The first step in this process is crushing and grinding the ore to a fine powder. This powdered ore is then subjected to a process called magnetic separation, where magnets are used to separate the iron particles from other minerals present in the ore. This helps in purifying the iron ore and increasing its iron content.
اقرأ أكثر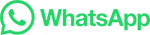