مرحبًا بكم في قاعدة إنتاج معدات التعدين. نحن ننتج بشكل أساسي معدات التكسير والطحن والتعدين ذات الصلة. إذا كان لديك أي احتياجات ، يمكنك الاتصال بخدمة العملاء عبر الإنترنت أو ترك رسالة من خلال النموذج أدناه. سوف نخدمك بكل إخلاص!.
Research into the crushing and grinding processes of …
Technological cycle of iron ore crushing and grinding under production conditions is possible only in terms of mechanical load being rather labour-consuming and energy-intensive. Application of physical impact methods on iron ore to intensify its crushing and grinding processes is still at the stage of research and development [9].
اقرأ أكثر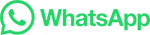
A review of modeling and control strategies for cone crushers …
Run-of-mine ore is usually too large to be useful for construction or metallurgy. Large particles must be reduced to specific sizes to either comply with aggregate sizing regulations, or facilitate mineral liberation; therefore, in the aggregates and mineral processing industries, run-of-mine ore is broken in crushing circuits by cone …
اقرأ أكثر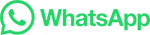
Iron ore mining & Washing | The Hira Group
IRON ORE CRUSHING . GPIL: Iron Ore Crushing Unit has always strived towards achieving a cleaner and a greener environment through its activities. It adheres to all the environmental norms and that forms the basis of its functioning as a socially responsible organization. The company considers it as one of its responsibilities to manage the ...
اقرأ أكثر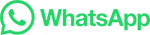
Iron Processing | Equipment, Process Flow, Cases
The former mainly selects magnetite ore, and the latter is mainly used for sorting hematite, mixed iron ore and weak magnetic ore. 6.2 Magnetic separation – cation reverse flotation process The grade of …
اقرأ أكثر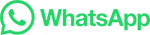
How to Process Talc (the Softest Mineral)? | Fote Machinery
1 Coarse crushing: First, the talc ore is evenly sent to a jaw crusher through a vibrating feeder for coarse crushing; 2 Drying: Then the crushed ore is sent to a dryer through a bucket elevator for dying; 3 Further crushing: After drying, talc ore is sent to a hammer crusher for medium and fine crushing; 4 Grinding: Next, talc ore is sent to a ...
اقرأ أكثر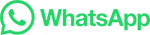
Improvement of heat pattern and sinter strength at high …
@article{Cheng2017ImprovementOH, title={Improvement of heat pattern and sinter strength at high charcoal proportion by applying ultra-lean gaseous fuel injection in iron ore sintering process}, author={Zhilong Cheng and Shangshang Wei and Zhigang Guo and Jian Yang and Qiuwan Wang}, journal={Journal of Cleaner Production}, …
اقرأ أكثر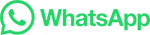
Solved In crushing a certain ore, the feed is such 80% is
Chemical Engineering questions and answers. In crushing a certain ore, the feed is such 80% is less than 50.8 mm in size and the product size is such that 80% is less than 6.35 mm. The power required is 89.5 kW. The power required using the same feed so that 80% is less than 3.18 mm is roughly around . Assume that Bond's Law applies.
اقرأ أكثر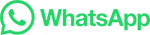
Iron ore crushing equipment and process flow
Iron ore crushing equipment and process flow. 17/08/2022 admin. Introduction of iron ore crusher: iron ore crusher is a kind of mechanical equipment that crushes iron ore raw ore step by step, from large pieces of raw iron ore (about 500mm) to millimeter-level fine materials. Usually, the iron ore dry separator is used to enrich the …
اقرأ أكثر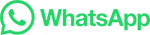
(PDF) Research into the crushing and grinding processes of iron ore
Research into the crushing and grinding processes of iron ore with its simultaneous effect by mechanical load and electric field of ultra-high frequency January 2019 E3S Web of Conferences 123(89 ...
اقرأ أكثر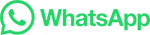
Advances in superfine crushing – a study on IMPTEC …
Because of this, there is the need for frugal energy use in mineral processing and this motivated the development of a novel super-fine crusher (SFC) that reduces coarse feed to fine and ultra-fine products with minimal recycle loads and lower energy input. In this study, the effect of selected operating parameters of the SFC on product ...
اقرأ أكثر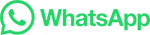
Advances in Ore Processing Technologies: Crushing, Milling …
Special Issue Information. Dear Colleagues, Advances in the mineral processing steps are constant. Crushing develops more efficient particle breaking, avoiding fine particles, and optimizing energy consumption. The liberation step is the grinding process and consumes most of the energy in a mineral processing plant.
اقرأ أكثر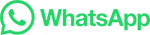
A Review on the Beneficiation of Ultra-Lean Iron Ores
Abstract. Nowadays, the demand of Chinese market for iron ores exceeds the supply. However, more than 90% the iron ores in China is of low grade with 30%Fe in average; the sub-marginal and ultra ...
اقرأ أكثر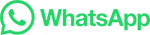
Iron ore beneficiation: an overview
The quality of Indian iron ore resources is generally good with high iron content and high percentage of lumpy ore. More than 85% of the hematite ore reserves are of medium- to high-grade (+62% Fe) and are directly used in blast furnace and in direct-reduced iron (DRI) plants in the form of sized lump ore, agglomerated sinter, and …
اقرأ أكثر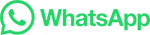
Ultra-high intensity blasting for improved ore …
the lower layer which comprises ultra-high powder factors and hence considerably higher blast energy. The broken rock from the earlier-firing upper layer provides an effective buffer to avoid ...
اقرأ أكثر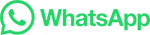
Ore Crushing
sizing crusher for clay with 10% of stones. Clay is sticky. sizing crusher is best choice for crushing the sticky material. 1. The crushing work conditions: Raw material: clay with 10% of stones The feeding size: 200 The discharged size: less than 100mm Capacity: 300-400t/h Solutions Model: FP 63AS Power: 200KW Weight: 22 ton Dimension: refer ...
اقرأ أكثر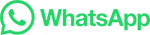
Measurement-Control for Crushing and Screening Process
Measurement for Crushing and Screening Process. It mainly includes the measurement for the material level of ore bin, solid material flow, the state of belt …
اقرأ أكثر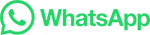
Improvement of heat pattern and sinter strength at high …
Fig. 11 presented the benefits from the equivalent calorific heat replacement of solid fuel with ultra-lean methane. It was observed that, the solid fuel consumption (the main contributor of contamination dust during the production, transportation and storage) would reduce 3.01%, 4.51%, 6.02% and 7.52% (on the basis of fuel mass in Case 1) at ...
اقرأ أكثر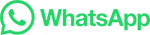
Improvement of heat pattern and sinter strength at high …
The sinter ore strength and yield were improved, and the effect of injecting ammonia in the early sintering stage was more significant. When the ammonia injection segregation degree is 0.042 %/min, the sinter ore yield and tumbler index increase from 61.93% and 49.4% to 68.85% and 58.8%, respectively, the average fuel combustion …
اقرأ أكثر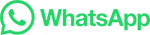
Ultra Fine Grinding
This method efficiently liberates finely disseminated gold or gold in solid solution. Whilst such oxidative reactions are metallurgically sound and are capable of achieving high …
اقرأ أكثر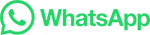
Suggestions on the Development and Utilization of Ultra
Ultra-lean magnetite refers to the iron ore that can be exploited and profitable under the current technical and economic conditions, where the total iron grade is 10% -20% and the magnetic iron ...
اقرأ أكثر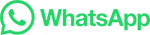
Achieving Ultra-Lean Combustion Using a Pre-Chamber …
This paper focuses on the performance evaluation of a pre-chamber spark ignition system operating under ultra-lean conditions. An experimental campaign is carried out using a rapid compression-expansion machine fueled with liquid iso-octane as a surrogate fuel for gasoline. The initial layout of the machine is modified to accommodate …
اقرأ أكثر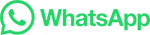
Background Report AP42 12.18 Lead-Bearing Ore …
After extraction, the ore is processed by crushing, screening and milling. Domestic lead mine production for 1991 totaled 480,000 megagrams (530,000 tons) of lead in ore concentrates, a decrease of some 15,000 megagrams (16,500 tons) from 1990 production. Except for mines in Missouri, lead ore is closely interrelated with zinc and silver. Lead
اقرأ أكثر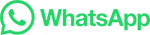
Depth-induced crushing mineral separation technology of super-lean
A magnetite ore and process technology, which is applied in the field of deep crushing and beneficiation of ultra-lean magnetite ore, can solve the problems of high tailings processing cost, low economic benefit of beneficiation, large raw ore grinding capacity, etc., and achieve reduction of ore grinding capacity, The effect of saving mineral processing costs …
اقرأ أكثر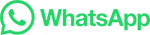
Mineral separation process and system for ultra-lean …
The mineral separation process for the ultra-lean magnetite ore comprises the following steps of sequentially carrying out coarse crushing, intermediate crushing and fine …
اقرأ أكثر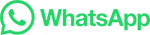
HuangLong Intelligent Crushing Technology Co Ltd
YGE series coarse crushing movable crushing station is the new stone crushing equipment, which is designed and promoted by Henan Mining Machinery Co., Ltd. Pangolin (Beijing) Intelligent Technology Co.,Ltd – drilling …
اقرأ أكثر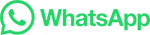
Ore Crushing | SpringerLink
Development trend of ore crushing: (1) Research and develop high-efficiency crushers to improve the energy conversion rate of fine crushers; (2) develop …
اقرأ أكثر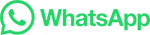
The effect of microwave pretreatment on impact crushing of lead-zinc ore
Compared with continuous microwave pretreatment, pulsed microwave pretreatment could improve the drop weight impact crushing efficiency of lead-zinc ore. When the specific comminution energy were 5 kW h/t, 10 kW h/t respectively, the crushing characteristic parameters t 10 were 60.42% and 67.46% respectively by continuous microwave.
اقرأ أكثر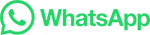
Crushing characteristics and performance evaluation of iron …
The effects of the eccentric speed on the residence time of particles in the crushing chamber can be indicated by its influence on the number of circulations, while …
اقرأ أكثر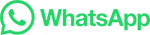
Advances in superfine crushing – a study on IMPTEC …
Because of this, there is the need for frugal energy use in mineral processing and this motivated the development of a novel super-fine crusher (SFC) that reduces coarse …
اقرأ أكثر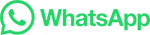
Research into the crushing and grinding processes of …
1 Introduction. The effectiveness of simultaneous effect of mechanical load and electric field of ultra-high frequency (UHF) in the process of iron ore crushing is substantiated in …
اقرأ أكثر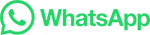