Solved 3. A cement grinding mill "A" with a capacity of 50
Expert-verified. 3. A cement grinding mill "A" with a capacity of 50 tons per hour utilizes forged steel grinding balls costing P12,000 per ton, which have a wear rate of 100 grams per ton cement milled. Another cement mill "B": of the same capacity uses high chrome steel grinding balls costing P50,000 per ton with a wear rate of 20 grams per ...
اقرأ أكثر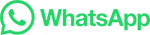
`Grinding Aid Effectiveness in Cement Ball Mill
Mill feeding increasing together with acceleration wear for Balls, Table (2) diaphragm and the linings (mill interior parts) It is well-known fact when using grinding aid in cement ball mills the feeding increase above the …
اقرأ أكثر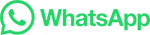
Process technology for efficient and sustainable cement production
Electrical energy only comprises between 10 and 15% of the overall energy demand for cement production but is a notable cost driver [4], [5].Over the last decades the average specific electrical energy consumption has decreased (Fig. 3) [6].However, there are counteracting effects: CO 2-emissions can be significantly reduced by the increased …
اقرأ أكثر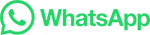
The Effect of Various Grinding Aids on the Properties of Cement …
Grinding aids, first introduced into cement manufacturing in 1930 [], are surface-active substances that facilitate particle comminution during the milling process.In the production of Portland cement, grinding aids are added in small amounts in the range of 0.01 to 0.10% by weight of cement, according to the PN-EN 197-1 standard [].They …
اقرأ أكثر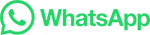
Cement Grinding Mills Of Various Capacities And Prices
Cement grinding mill is usually used in the clinker grinding process.It is the final stage in cement production which will directly affect the cement product quality, output and benefits. Clinker particles, gypsum, and other materials in cement grinding machine will be ground together into fine powder to match the fineness of the finished …
اقرأ أكثر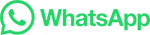
Clinker grinding technology in cement manufacturing
Mill capacities, especially in cement grinding are changing the scenario. There were no high capacity mills in the past for clinker grinding. Advanced VRM …
اقرأ أكثر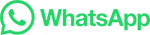
Grinding Mills
The great range of sizes covered by industrial ball mills is well exemplified by Fig. 1.1 and Fig. 1.2. In the first illustration is shown a laboratory batch mill of about 1-litre capacity, whilst in Fig. 1.2 is shown …
اقرأ أكثر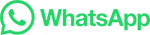
Open and closed circuit dry grinding of cement mill rejects …
The separator reject sample from a nearby cement factory (Oyak Bolu Cement Industry) was collected for the experimental part of this study. The sampling point for the clinker grinding circuit was depicted in Fig. 2.The capacity of the cement mill during the sampling time was 130 t/h and the specific energy consumption was 32 kW h/t.
اقرأ أكثر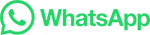
11.6 Portland Cement Manufacturing
In the wet process, water is added to the raw mill during the grinding of the raw materials in ball or tube mills, thereby producing a pumpable slurry, or slip, of approximately 65 percent solids. The slurry is agitated, blended, and stored in various kinds and sizes of cylindrical tanks or slurry basins until it is fed to the pyroprocessing ...
اقرأ أكثر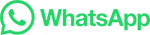
Cutting-Edge Grinding Solutions
ICR looks at the inner workings of grinding mills in the cement industry to understand the technological advancements that are reshaping the landscape against the foreground of sustainability. Innovations to enhance the grinding processes are aimed at minimising their environmental footprint while increasing efficiency and performance. In …
اقرأ أكثر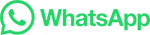
Improvements in New & Existing Cement Grinding Mills by …
Plant Capacity. The plant will have a capacity to produce 1.0 million tonnes of cement per annum (1.0 MTPA). Three different types of Portland cement1 will be …
اقرأ أكثر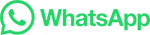
(PDF) Measurements of Vibration and Noise …
Three stations were chosen for each company (raw materials grinding mills, cement grinding mills and exhaust fan stations) having different electrical motor capacities. Noise level meter and ...
اقرأ أكثر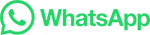
The Effect of Various Grinding Aids on the Properties of Cement …
1. Introduction. Grinding aids, first introduced into cement manufacturing in 1930 [], are surface-active substances that facilitate particle comminution during the milling process.In the production of Portland cement, grinding aids are added in small amounts in the range of 0.01 to 0.10% by weight of cement, according to the PN-EN 197-1 standard [].
اقرأ أكثر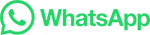
Grinding aids for dry fine grinding processes
Scheibe et al. [25] carried out an extensive investigation of various grinding aids on the batch-wise grinding of cement clinker, quartz and limestone in the 1970s. They found that the impacts of the applied chemical on parameters like the product fineness or the material adhesions inside the mill depend on a complex relation between the ground ...
اقرأ أكثر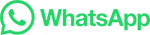
OPTIMIZATION OF CEMENT GRINDING OPERATION IN …
The consumption of energy by the cement grinding operation amounts to one third of the total electrical energy used for the production of cement. The optimization of this process …
اقرأ أكثر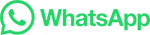
Calculations for design of ball mills for cement grinding
There are a few factors that need to be considered while designing a ball mill for grinding cement. These include the following: 1) Ball mill design requirements - The first step in ball mill sizing is to determine what design requirements should be met by the ball mill. This will depend on the type of cement being ground and the specific application requirements of …
اقرأ أكثر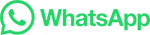
The most reliable and eficient mill for raw and cement …
Proven commercially, the OK mill is the premier roller mill for finish grinding of Portland cement, slag and blended cements. The OK mill's grinding efficiency can contribute …
اقرأ أكثر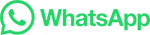
Cement grinding optimisation
1. Introduction. For all dry grinding applications, cement production is certainly the most important. The estimate for the world energy consumption for cement …
اقرأ أكثر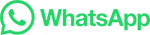
Effects of grinding aids on model parameters of a cement ball mill …
The advantages of using grinding aids in the cement industry on the performance of ball mills and air classifiers [1], as well as the effects of various dosages of different types of chemical ...
اقرأ أكثر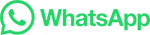
OPTIMIZATION OF CEMENT GRINDING OPERATION IN …
Operation and Elements of a Closed-Circuit Ball Mill System . Cement ball mills typically have two grinding chambers. The first chamber is filled with larger diameter grinding media andlined with lifting liners . The first chamber coarse-grinds the feed material and prepares it for the second chamber. The second chamber is the fine grinding ...
اقرأ أكثر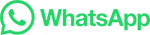
Blended Cement Grinding: Energy Intake and Fineness
The grinding media are usually made of high-chromium steel. Fineness is a controlled parameter for cement to ensure better hydration and strength development. Ground cement is then stored in a water-proof concrete silo for packing. Making Cement Green. The rise of blended cement, starting from use of fly ash (30 per cent to 35 per …
اقرأ أكثر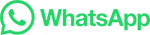
(PDF) Cement grinding optimisation | Alex Jankovic
These models can be used to simulate cement grinding circuits and to assist their optimisation. The "work horse" of the cement grinding plant is the two-compartment ball mill, commonly called the tube mill. Significant advances in model development were achieved in recent years (Benzer et al, 2001, 2003) through research on industrial scale.
اقرأ أكثر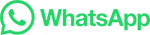
Answered: A cement grinding mill "A" with a… | bartleby
Accounting. A cement grinding mill "A" with a capacity of 50 tons per hour utilizes forged steel grinding balls costing ₱ 12,000 per ton, which have a wear rate of 100 grams per ton cement milled. Another cement mill "B" of the same capacity uses high chrome steel grinding balls costing ₱ 50,000 per ton with wear rate of 20 grams ...
اقرأ أكثر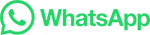
Cement grinding optimisation
Cement grinding optimisation. In this chapter an introduction of widely applied energy-efficient grinding technologies in cement grinding and description of the operating principles of the related equip‐ ments and comparisons over each other in terms of grinding efficiency, specific energy consumption, production capacity and cement quality ...
اقرأ أكثر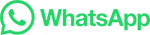
How to choose proper grinding media for your ball mill
Steel balls are one of the most widely used grinding media in cement ball mills, their diameters can range from 20mm to 120mm according to different grinding requirements. In a cement ball mill, generally, φ50–100mm steel balls are used in the coarse grinding chamber, φ20–50mm steel balls are used in the fine grinding chamber. 2.
اقرأ أكثر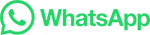
Overview of cement grinding: fundamentals, additives, technologies
Abstract. Grinding is an essential operation in cement production given that it permits to obtain fine powder which reacts quickly with water, sets in few hours and hardens over a period of weeks ...
اقرأ أكثر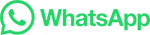
Characterization of various cement grinding aids and their …
The evaluation of the grinding aids (GA) was carried out by interground 0.015% of each grinding aid with gypsum and a Portland cement clinker (95% clinker, 5% gypsum), in a 1 kg laboratory rotating ball mill, using steel balls as grinding medium, to a Blaine surface area of about 4000 cm 2 /g (according to the Blaine air permeability …
اقرأ أكثر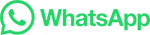
Latest trends in modular cement grinding plants
One such opportunity is modular cement grinding plants. Various proven compact plant concepts are available on the market. In this article we will have a closer look into the technology and discuss the regional markets where it is used. ... depending on the mill size, much larger cement capacities can be achieved. However, in the compact sector ...
اقرأ أكثر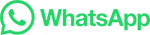
An industrial comparative study of cement clinker grinding …
Comparing industrial clinker grinding for three different grinding systems. Energy consumption and cement quality variations at the same cement fineness. The …
اقرأ أكثر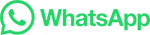
Energy-Efficient Technologies in Cement Grinding | IntechOpen
In this chapter an introduction of widely applied energy-efficient grinding technologies in cement grinding and description of the operating principles of the related equipments and comparisons over each other in terms of grinding efficiency, specific …
اقرأ أكثر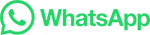