Counteracting ring formation in rotary kilns
Avoiding the formation of rings in rotary kilns is an issue of primary concern to the cement production industry. We developed a numerical combustion model that …
اقرأ أكثر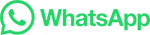
cement kiln lnlet coating reasons – Grinding Mill China
what is the reason for excess coating in cement kiln inlet …. REDUCHLOR® – Chlorine Bypass for Cement Kiln Systems! … Bypass for Cement Kiln Systems … problems of coating by dust deposition in kiln riser duct, meal pipes … » More detailed kiln inlet coating. Home » Forum » Technical Cement Forum » kiln inlet coating 55 posts. Time …
اقرأ أكثر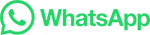
(PDF) Combined calcination and CO2 capture in …
The required electrical energy input for calcination in a kiln system producing 1 Mt of clinker per year, is about 85 MW. An early-phase cost estimate was conducted resulting in total annualized ...
اقرأ أكثر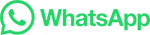
What are the reasons behind formation of Kiln build-ups
The bonding is created by the freezing of the clinker liquid phase. This phenomenon occurs especially in the burning zone inlet, where the liquid phase is just starting to form, at approximately 1250°C. Due to the rotation of the kiln, the material freezes with each kiln rotation and deposit of clinker particles having less than 1 mm diameter ...
اقرأ أكثر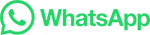
Impact of coating layers in rotary cement kilns: Numerical
In the case of heavy coating, a temperature shift towards the solid material inlet of the kiln occurs, which outweighs the beneficial insulation effect of the coating in …
اقرأ أكثر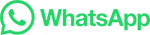
Elimination of cyclone blockages in a cement works
The following tasks in a cement plant are among those associated with considerable hazards and stresses: Working in the preheater tower (PT) Elimination of blockages in the PT. Working in the kiln. Working in silos. Operation of packing machines. Loading into tankers. Mill maintenance and repair. Fuel use (coal dust, substitute fuels)
اقرأ أكثر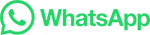
Snowman Formation and Prevention
Build ups are often the reason for kiln shut downs. Increased pressure losses or the different chemical compositions of intermediate products, give first indications. Very often salt compositions (e.g. alkali chlorides and sulfates) cause those undesired build ups, which can be found from the kiln inlet up to the cyclones of the preheater tower.
اقرأ أكثر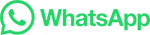
Cement Manufacturing and Process Control | SpringerLink
Kiln heat up. Kiln shutdown. Download chapter PDF. 4.1 Cement Manufacturing: Basic Process and Operation. To design the Refractory for the lining of …
اقرأ أكثر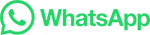
Reliable Kiln Inlet Gas Analysis: Part 1
Using this technique, the kiln inlet gas is kept above acid dewpoint in the sample system and is transferred into the analyser without any further gas conditioning or drying treatment. Benefits of the hot-wet measurement technique. Combustion gases at kiln inlet are mainly composed of O 2 (2 – 4%), CO 2 (12 – 15%), H 2 O (8 – 10%) and N 2.
اقرأ أكثر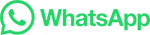
Problem Material leakage at kiln inlet
5. Check kiln tyre migration and floating. 6. If the spillage is just after shutdown then please check there is no step in inlet slope cast able. 7. If kiln is due for shut then there might be some castable failure of kiln inlet slope. 8. Check that there is no coating in front of cycle 6 (for 6 stage P/H) Feed pipe… 9.
اقرأ أكثر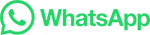
cement kiln inlet coating reasons – Grinding Mill China
what is the reason for excess coating in cement kiln inlet …. REDUCHLOR® – Chlorine Bypass for Cement Kiln Systems! … Bypass for Cement Kiln Systems … problems of coating by dust deposition in kiln riser duct, meal pipes … » Free online chat! kiln inlet coating. Home » Forum » Technical Cement Forum » kiln inlet coating 55 posts. Time …
اقرأ أكثر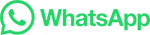
Coating and Burnability of Clinker | SpringerLink
The effect of severity of prevailing condition, inside the kiln, can be mitigated by the formation of a stable coating on the refractory surface. Three different conditions related to coating formation may arise, namely: 1. Stable coating formation of normal thickness, with minimum stress on the Refractory lining. 2.
اقرأ أكثر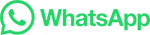
Cement kiln inlet gas analysis
The payback of an on-line kiln inlet gas analysis system from FL is less than 200* days. After that, it is helping you extend your margins and overhaul the competition every day. Benefits of gas analysis components measured at the kiln inlet In general, gas analysis gives you the chance to deal with problems and issues as they arise at ...
اقرأ أكثر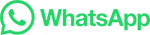
The reason of snowman and measures for prevention – THE CEMENT
2. Stabilize the thermal system in the kiln, avoid excessive kiln temperature and liquid phase quantity, and carefully observe the fire. 3. Improve the structure of grate bed; 4. The high-sulfur raw coal is limited to the factory and used together to ensure that the SO3 in the pulverized coal entering the kiln does not exceed the standard; 5.
اقرأ أكثر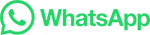
The Air Circuit in a Rotary Kiln
By weigh each unit of fuel burned (lb or kg) requires approximately units (lb or kg) of combustion Air, at standard conditions, has a specific volume of approximately 0.7735 m3fkg (12.39 ft3/Jb). Hence, to bum 1 kg of fuel requires approximately 8.12 m3 of air for combustion in the kiln. Likewise, burning l lb of fuel requires approximately 130 ...
اقرأ أكثر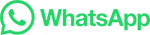
Kiln Inlet Coating
Re: Kiln Inlet Coating. Usually coatings or buildups in this area are due to an elevated sulphur cycle caused by either poor combustion in the main flame, or use of high SO3 fuels such as petcoke. The key is to ensure enough O2 at the kiln inlet to control excessive SO3 recirculation. High sulphur levels in the raw materials can also be a cause.
اقرأ أكثر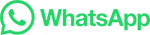
Kiln Inlet Coating
Re: Kiln Inlet Coating. Usually coatings or buildups in this area are due to an elevated sulphur cycle caused by either poor combustion in the main flame, or use of high …
اقرأ أكثر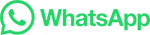
ProKiln GAC400 | Gas sampling system for kiln and calciner
ProKiln is the 4th generation of ABB for gas sampling at the kiln inlet and calciner in the cement industry. The premium product has been developed to meet the changing process conditions in cement plants due to the increased use of alternative fuels. ... With 60 years' combined experience, the 4th generation kiln inlet solution of ABB has ...
اقرأ أكثر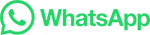
The cement kiln
Manufacturing - the cement kiln. Most Portland cement is made in a rotary kiln. Basically, this is a long cylinder rotating about its axis once every minute or two. The axis is inclined at a slight angle, the end with the …
اقرأ أكثر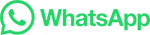
Coating and Burnability of Clinker | SpringerLink
Coating plays a very important role on the refractory life in burning zone, of the rotary kiln, where the condition is most arduous. The mechanism of coating …
اقرأ أكثر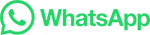
reasons of boulder formation in cement kiln | Mining
what is the reason for excess coating in cement kiln inlet … Posts Related to what is the reason for excess coating in cement kiln inlet. … Cement Lime Gypsum; Coating Formation in Kiln Inlet (Clinker Production) Category: Uncategorized « craigslist roof panel machine used portable. gold mine business ...
اقرأ أكثر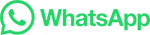
What is the formation mechanism of "Snowman", "Rhino …
2). Occasionally large lumps of coating discharge from the kiln, these lumps of kiln coating act as "seeds" for the formation of snowmen. Snowmen form when fines fall from the kiln above, onto the top surfaces of these lumps on top of the clinker bed within the cooler.
اقرأ أكثر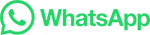
Coating formation in Kiln Inlet
Coating at kiln inlet ia mainly due to the volatiles like Chlorides, alkalies ( Na2O and K2O) and SO3. To minimise the coating formation, the alkali sulfate ratio …
اقرأ أكثر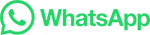
Practical Guide about Kiln REFRACTORIES
6.4 Kiln Cleaning (kiln coating removal) Kiln with diameter Ø bigger than 4.0 m has to be free of his coating and clean. Completely from the nose-ring to the inlet. – To protect the workers from the falling coating – To permit a good inspection of the bricks lining Kiln with smaller Ø don't loose easily its coating, thus it is possible ...
اقرأ أكثر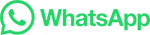
Pyroprocessing and Kiln Operation
January 16, 2023. By. admin. Dr SB Hegde, Professor, Jain University, Bangalore, talks about pyroprocessing and the role of preheater, rotary kiln and clinker cooler in the cement manufacturing process. In the concluding part of the two-part series, we will learn more about the various factors aiding pyroprocessing. False Air in Pyro Processing.
اقرأ أكثر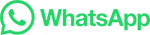
Everything you need to know about combustion in Cement Kiln
Previous Post Next Post Contents1 Everything you need to know about combustion in Cement Kiln1.1 GAS LAWS1.1.1 Boyle's Law.1.1.2 Charles' Law.1.1.3 Gay-Lussac's Law.1.1.4 A General Law.1.2 THE COMBUSTION REACTION1.3 THE STANDARD COAL FACTOR, COMBUSTION AIR REQUIREMENTS1.3.1 Effect of Kiln Air on Combustion …
اقرأ أكثر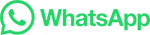
Reasons for drop in Kiln inlet temperature
Kiln inlet temp drop due to following reason. 1. Heavy coating at kiln inlet - check temp. profile in kiln calcination zone ( kiln inlet to 10. mtr ) 2. Can having co formation at kiln inlet .-. To avoid co formation for it. PL send your sreen shot of kiln and calciner on same time on forum. Thank for sharing your problem.
اقرأ أكثر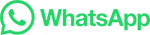
Numerical investigation of the impact of coating layers on …
Fig. 22 shows that the residence time of the material in the case of heavy coating is above 11 s in the segments near the kiln inlet, while the reference case has an even residence time distribution of 2.81 s. The simulation with light coating also has increased material residence times near the kiln inlet of up to 4.81 s.
اقرأ أكثر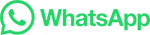
re Reasons for drop in Kiln inlet temperature
re Reasons for drop in Kiln inlet temperature. Dear Mr. Ramesh, There may be possibilities that material which enters in the Calciner, part of material directly falling at Kiln inlet. Reason may be whatever so. 1. Please check dispersion plate of material entering in Calciner, check the angle and shape of dispersion plate. 2.
اقرأ أكثر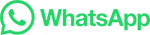
CEMTEC gas sampling probe system | ENOTEC
Information. The CEMTEC ® gas sampling probe system was developed for continuous analysis of flue gas in cement plant rotary kiln inlets and other extremely dusty, high temperature processes such as in lime plants with the goal of increasing product quality with reduced fuel usage while simultaneously reducing harmful emissions.. Particularly in view …
اقرأ أكثر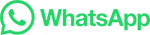