One-pot wet ball-milling for waste wire-harness recycling
ResultIn this study, we developed a one-pot wet ball-milling method for the recovery of highly pure copper wire, poly(vinyl chloride) (PVC) coating, and …
اقرأ أكثر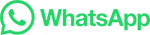
What Are the Differences between Dry and Wet Type Ball Mill?
ResultThe wet ball mill has a low noise, and low environmental pollution. The wet ball mill has a simple transportation device with less auxiliary equipment, so the investment is about 5%-10% lower than that of a dry ball mill. The grinding particle size is fine and uniform. The wet ball milling can not only grind …
اقرأ أكثر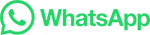
The effectiveness of wet milling materials in ball mills
ResultUDC666.3.022.2. Wetmilling of solids nball mills ismore intensive than dry milling. The reason forthis has been explained by investigators [1-4] in different ways. …
اقرأ أكثر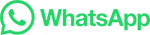
Wet ball milling of niobium by using ethanol, determination …
Result6 Citations. Metrics. Abstract. This study investigates the effect of using ethanol as the process control agent during the wet ball milling of niobium (Nb). Dried nanocrystal Nb powders,...
اقرأ أكثر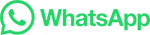
Ball Milling | Material Milling, Jet Milling | AVEKA
ResultTalk to an AVEKA expert to help develop your ball milling process conditions. Download the Grinding and Classification flyer here. Capabilities and Equipment Specs (4) 200 gallon Ball Mills – ceramic lined, dry (1) 100 gallon Ball Mill – ceramic lined, wet (2) 60 gallon Ball Mills – ceramic lined, dry ...
اقرأ أكثر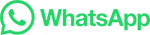
Materials Development Using High-Energy Ball Milling: A …
ResultHigh-energy ball milling (HEBM) of powders is a complex process involving mixing, morphology changes, generation and evolution of defects of the crystalline lattice, and formation of new phases. This review is dedicated to the memory of our colleague, Prof. Michail A. Korchagin (1946–2021), and aims to …
اقرأ أكثر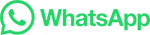
Ball Mill Machine
ResultBecause internal ball mill grinding media are mostly spherical in different specifications and materials, so it is named ball mill machine. ... According to production mode: dry ball mill (without adding water) and wet ball mill. According to the process used: dryer mill, superfine ball mill, open-circuit mill, closed-circuit …
اقرأ أكثر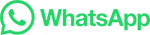
TECHNICAL SPECIFICATION OF WET BALL MILL …
ResultThe Gravimetric feeder feeds limestone to Wet ball mill system. The Wet Ball Mill system consists of Wet Ball Mill, Wet Ball Mill Lubrication system, Mill circuit tank with an agitator, Mill circuit Pump, Mill Hydro cyclone, 3-way distributor and accessories. The Wet Ball Mill is the wet horizontal type. The Process water …
اقرأ أكثر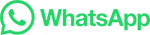
Ball-impact energy analysis of wet tumbling mill using a …
ResultA modified three-dimensional quasi-wet discrete element method (DEM), which is constructed by adding the drag force and buoyancy and the …
اقرأ أكثر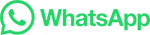
Wet Continuous Production Mills
ResultC-60. Continuous Attritors are best suited for the continuous production and fast grinding of large quantities of material. They are designed to deliver hours of low-cost, maintenance-free operation. The basic model features a system that does not require an expensive shaft seal. Continuous Attritors come in two basic types, "C" …
اقرأ أكثر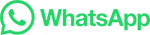
Ball milling as a mechanochemical technology for
ResultMechanochemical technique aims to strike a balance between defect formation via ball milling and size adjustment of a solid grain to nanoscale (<1000 nm) (Ullah et al., 2014).During the process, a high-energy mill is employed and a specific powder charge is placed along with a milling medium (Lin et al., …
اقرأ أكثر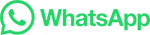
Ball milling process variables optimization for high-entropy …
ResultFor milling time, the ball milling process was interrupted at a regular interval of 10 h for powder extraction and characterization, up to a total milling time of 60 h. It is worth noting that a small ball (which weighs ~1 g) is removed at every 0.1 g of powder extraction to maintain the ball-to-powder ratio.
اقرأ أكثر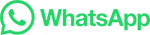
Physicochemical properties of ball milled boron particles: Dry vs. wet
ResultIn the wet milling process, the boron powder and tungsten carbide ball were put into the milling jar as in the dry milling process. Also, 15 ml of anhydrous hexane (Sigma-Aldrich, purity of 95%) as a solvent and 1 ml of oleic acid (Sigma-Aldrich, USA) as a coating material were added to the milling jar.After the …
اقرأ أكثر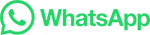
Comparative Study on Improving the Ball Mill Process …
ResultThe ball mill process parameters discussed in this study are ball to powder weight ratio, ball mill working capacity and ball mill speed. As Taguchi array, also known as orthogonal array design, adds a new dimension to conventional experimental design, therefore, Orthogonal array (L9) was carefully chosen for …
اقرأ أكثر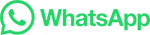
Ball Grinding Process | SpringerLink
ResultBall grinding process is a grinding method of crushing ore with ball-shaped grinding medium in the grinding mill. In the ball grinding process, because the steel ball has 360° free rotation, it is suitable for falling motion and throwing motion. When the rotating speed of the cylinder is low, the medium rises to a …
اقرأ أكثر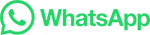
Grinding in Ball Mills: Modeling and Process …
ResultA ball mill is a type of grinder widely utilized in the process of mechanochemical catalytic degradation. It consists of one or more rotating cylinders partially filled with grinding balls …
اقرأ أكثر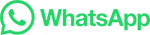
One-pot wet ball-milling for waste wire-harness recycling
ResultThe wet ball-milling tests were conducted at different rotating speeds (20, 25, 35, and 45 rpm) using the 20-mm balls. Figure 7a shows the wet ball-milling separation results in n-butyl acetate. Complete separations are achieved within 90, 70, 60, and 50 min of wet ball milling at rotating speeds of 20, 25, 35, and 45 …
اقرأ أكثر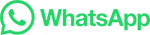
Dynamic Modelling of Temperature in a Wet Ball Mill …
ResultA dynamic model is developed for a wet overflow ball mill based on a set theof mass and energy balances. The energy balance relies on temperature …
اقرأ أكثر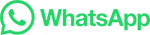
Ball Mill (Ball Mills Explained)
ResultCrushed ore is fed to the ball mill through the inlet; a scoop (small screw conveyor) ensures the feed is constant. For both wet and dry ball mills, the ball mill is charged to approximately 33% with …
اقرأ أكثر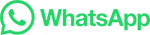
Process Control of Ball Mill Based on MPC-DO
ResultThe grinding process of the ball mill is an essential operation in metallurgical concentration plants. Generally, the model of the process is established as a multivariable system characterized with strong coupling and time delay. In previous research, a two-input-two-output model was applied to describe the …
اقرأ أكثر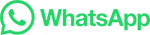
Ball Milling
ResultBall milling, a shear-force dominant process where the particle size goes on reducing by impact and attrition mainly consists of metallic balls (generally Zirconia (ZrO 2) or steel balls), acting as grinding media and rotating shell to create centrifugal force.In this process, graphite (precursor) was breakdown by randomly striking …
اقرأ أكثر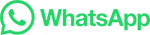
Modern Wet Milling and Material Processing | …
ResultTraditional Wet Milling. The coatings industry is no different from others in its search for modern manufacturing techniques. The traditional high-speed dissolver, ball mill, vertical mill and standard horizontal mill have been the primary methods used to mill pigmented materials for more than 50 years, and are still …
اقرأ أكثر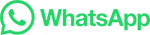
Energy-Mass-Size balance model for dynamic control of …
ResultThe model combines information from energy-mass balance, material breakage mechanisms, fundamental material properties and the milling conditions in a …
اقرأ أكثر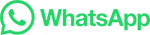
Ball mill simulation in wet grinding using a tumbling mill …
ResultVisualization of actual ball motion in wet milling. The mill used in this work was a tumbling ball mill made of stainless steel having 81-mm inner diameter and 110-mm length. Monosize steel balls of 10-mm diameter were used as grinding media. In order to visualize the motion of balls, one side of the mill lid was made …
اقرأ أكثر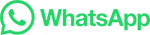
Foods | Free Full-Text | Emulsification Characteristics of
ResultTo improve the application potential of pomelo peel insoluble dietary fiber (PIDF) in emulsion systems, acetylation (PIDF-A), cellulase hydrolysis (PIDF-E), and wet ball milling (PIDF-M) were investigated in this paper as methods to change the emulsification properties of PIDF. The impact of the methods on PIDF …
اقرأ أكثر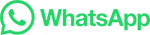
Load State Identification Method for Wet Ball Mills Based on …
ResultAbstract. To overcome the difficulty of accurately judging the load state of a wet ball mill during the grinding process, a method of mill load identification …
اقرأ أكثر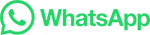
Preparation of Natural Rubber Composites with High Silica …
ResultThe optimum conditions for silica dispersion preparation were calculated to be a 22% silica content and 62 h of ball milling, to get the smallest silica particle size (5.0 μm). However, this long ball milling time needed good engineering management and economic analysis of this process for industrial …
اقرأ أكثر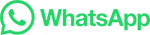
Energy-Mass-Size balance model for dynamic control of …
ResultA dynamic model is developed for a wet overflow ball mill based on a set of mass and energy balances to simulate the mill. The energy balance relies on temperature and mass flow data. The key control parameters to be measured are mill temperature (feed and discharge streams), mill power draw and the mass flow …
اقرأ أكثر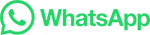
Wet milling
ResultThe wet milling machine benefits make them attractive investments. IKA wet milling machines are based on the rotor-stator principle. Exhibiting a high level of shearing energy input, milling machines can achieve particle sizes of 10 µm and below. IKA wet mill machines are capable of processing products with a broad spectrum of …
اقرأ أكثر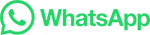
Ball milling: a green technology for the preparation and
ResultThe ball mill Ball milling is a mechanical technique widely used to grind powders into ne particles and blend materials.18 Being an environmentally-friendly, cost-effective technique, it has found wide application in industry all over the world. Since this mini-review mainly focuses on the conditions applied for the prep-
اقرأ أكثر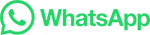