Primary Crusher Optimisation for Improved Comminution
The crushing plant can be provided with almost any type of primary rock crusher. The rock/ore determines the type of crusher. The plant capacity determines the size of the crusher. As the term 'primary' implies, these crushers are used in the first stage on any size reduction cycle. The primary crusher is the link between chemical ...
اقرأ أكثر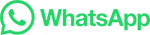
What is a primary crusher
Request a Callback. +1 800 329 3375. Supporting equipment all across the U.S. /. +1 800 329 3375. /. info@machinerypartner. Grow your crushing & screening business with the right equipment, right finance, and expert support. Browse our range of excavators, screeners, crushers + more.
اقرأ أكثر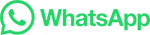
The Complete Guide to Primary Crushing, …
Primary Crushing. Primary crushing is the first stage in the comminution process and involves breaking down large rocks into smaller pieces of a size that can be handled by the downstream …
اقرأ أكثر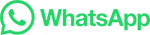
What Type of Crusher Is Best for Primary Crushing?
See more on mclanahan
Explore further
(PDF) Crushing and Screening HandbookWebWhile primary crushers are responsible for breaking down larger rocks and stones into smaller particles, secondary crushers are used to further refine these particles into the desired size and shape. The …
اقرأ أكثر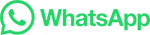
Primary and Secondary Crushing: Understanding …
Secondary crushing is the second stage of crushing that takes place after the primary crushing. The secondary crusher is the equipment that reduces the size of the materials further, after they have …
اقرأ أكثر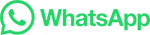
Gyratory Crusher (Gyratory Crushers Explained)
A primary crusher is designed to receive run-on-mine (ROM) rocks directly from the mines. Gyratory crushers typically crush to reduce the size of aggregate to a maximum of about one-tenth of its original size. Gyratory …
اقرأ أكثر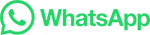
Gyratory Crusher vs. Cone Crusher: What's the Difference?
A gyratory crusher has a mantle that rotates within a concave bowl, while a cone crusher has a mantle that rotates within a bowl-shaped concave. This design allows for a larger feed size and a higher capacity for both types of crushers, but gyratory crushers are typically designed for high-capacity crushing whereas cone crushers are intended ...
اقرأ أكثر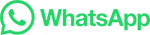
Grizzly bars and feeders improve primary crushing efficiency
Primary Crushing. The primary jaw crusher is the first stage of processing in most sand, gravel, and mining operations. Material that has been excavated from the ground (Pit run) or blasted (Shot Rock) is fed to a large crusher, typically a jaw crusher, where it is crushed down to a manageable size for further processing.
اقرأ أكثر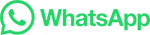
Primary Crushing: A Comprehensive Guide
Before we start primary crushing, the first stage of material reduction, we often need to get them from mines or rock quarries. This is typically accomplished by blowing objects up or digging. This raw material can be big and oddly shaped. It is then moved to the primary crusher. This is usually done by large trucks or a conveyor belt.
اقرأ أكثر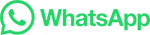
Choosing the Right Crusher
It's a primary crusher. The jaw crusher is a machine for crushing rocks and other hard and abrasive materials, such as granite, ores or recycled concrete, usually for industrial purposes. The crushing device consists of a fixed plate and a swing plate called jaws between which the rock is trapped and crushed. A motor and a belt transmit the ...
اقرأ أكثر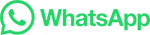
Primary and secondary crushers
The crushing of material into smaller loads is usually undertaken in two steps, starting with the primary crusher that includes jaw crushers, hammer mill crushers, and gyratory crushers. Larger stones or mineral ores are used to produce smaller material. Where the material is not reduced sufficiently in the primary crusher, it is then crushed ...
اقرأ أكثر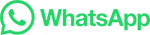
Primary Crushing Station | SpringerLink
Underground primary crushing station (Fig. 3) is generally fixed. It is usually located next to the skip shaft and is characterized by long service life, long infrastructure time, etc. The main equipment of the primary crushing station includes a crusher, feeder, dedusting apparatus, crane, etc. The primary crusher is mainly divided into ...
اقرأ أكثر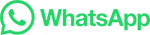
How To Select Your Primary Crusher
by JXSC Mining. How you select the best primary crusher from all of the available primary crushers is required a great deal of design based on the mining plan and operation input. Usually, capacity, feed size, product size, rock compressive strength, abrasion index and mobility of crusher are considering as criteria, and in practice ...
اقرأ أكثر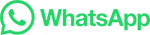
What Is Primary, Secondary, and Tertiary Crushing?
Primary crushing is the first stage of material reduction and can sometimes be the only stage needed to generate the desired product for a job. ... or reclaimed and process it through an impactor, jaw, or gyratory crusher to generate a range of product sizes. For many aggregate producers, utilizing a closed-circuit portable crusher plant with ...
اقرأ أكثر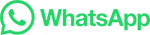
Influence of jaw crusher parameters on the quality of primary …
In the second crushing stage, the product from the first crushing stage is loaded into the crusher in a single batch. The amount of material used in laboratory crushing is minimum 30 kg. The crusher was tested at several settings, and 11 mm was chosen because this was the setting which generated the most material in the 10–14 mm …
اقرأ أكثر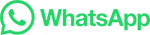
Crushing 101 – Different types of crushers for distinctive needs
Jaw crushers can be divided into two basic types, single and double toggle. In the single toggle jaw crusher, an eccentric shaft is on the top of the crusher. Shaft rotation, along with the toggle plate, causes a compressive action. A double toggle crusher has two shafts and two toggle plates. The first shaft is a pivoting shaft on the top of ...
اقرأ أكثر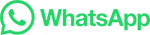
Crushers and Their Types – IspatGuru
Crushers are classified into three types based upon the stage of crushing they accomplish. These are (i) primary crusher, (ii) secondary crusher, and (iii) tertiary crusher. The primary crusher receives material directly from run of mine (ROM) after blasting and produces the first reduction in size. The output of the primary crusher is fed …
اقرأ أكثر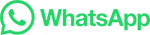
Primary Crushing Stations I FL
Our indirect-fed Primary Crushing Plants are highly suitable for hard rock applications where IPCC systems are in place. Apron feeders are typically used to feed materials to the crusher as the first step in an In-Pit Crushing and Conveying operation. After the crusher, a discharge conveyor connects the Primary Crushing Unit to the following ...
اقرأ أكثر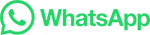
How to Select the Right Primary Crusher | Mellott
We're here to help you make the right decision. At Mellott, we're experts at navigating all the factors involved in primary crusher selection. If you're considering a replacement crusher or looking for a …
اقرأ أكثر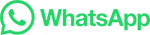
Crusher
Crushing is accomplished by compression of the ore against a rigid surface or by impact against a surface in a rigidly constrained motion path. Crushing is usually a dry process and carried out on ROM ore in succession of two or three stages, namely, by (1) primary, (2) secondary, and (3) tertiary crushers. 13.3.1.1 Primary Crusher
اقرأ أكثر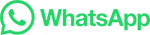
Understanding Types of Jaw Crusher: A Comprehensive …
Blake jaw crushers, also as double toggle jaw crushers, are characterized by the position of the pivot of the swing jaw, which is located at the top of the machine. This design allows for a larger feed size and a higher capacity, making it suitable for primary crushing. The motion of the swing jaw in a Blake crusher is predominantly vertical ...
اقرأ أكثر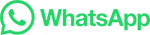
Primary Crushing: A Comprehensive Guide
Gyratory crushers, with their rotating mantle and conical-shaped opening, elevate the efficiency and capacity thresholds of primary crushing. Designed to handle …
اقرأ أكثر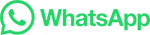
Choosing the right primary crusher for your …
The first step in choosing a primary crusher takes place at a high level. It's necessary to identify the purpose the crusher will be used for. This purpose is a given that precedes the entire decision-making process. Sometimes, …
اقرأ أكثر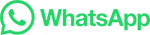
what is a primary and secondary crusher?
The primary crusher is designed to handle large rocks and to produce a product that is easy to transport and process further in the aggregate processing plant. Examples of primary crushers include ...
اقرأ أكثر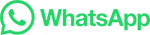
Gyratory Crushers
The primary rock breaker most commonly used in large plants is the gyratory crusher, of which a typical section is shown in Fig. 5. It consists essentially of a gyrating crushing head (521) working inside a crushing bowl (522) which is fixed to the frame (501). The crushing head is carried on a short solid main shaft (515) suspended …
اقرأ أكثر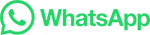
Working Principle of Crushers
The gyratory crusher is used as a primary and secondary stage crusher. The cone crusher is used as a secondary, tertiary, and quaternary crusher. The action of a typical gyratory-type crusher is illustrated above. ... These are generally designed for primary crushing in large-scale rock crushing applications up to 6000 t/h. Typically a …
اقرأ أكثر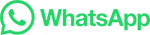
CG820 Primary Gyratory Crusher For Safe Crushing …
CG820i. Capacity (by hour) 1,500 - 4,000 mtph (1,650 - 4,400 stph) Feed opening. 1,372.0 mm (54.0 in.) Motor power. 525 kw (700 hp) CG820i crusher is built to be robust, reliable and efficient. Connected to SAM by , they revolutionize availability and optimize uptime by giving you actionable insights into how the crusher is ...
اقرأ أكثر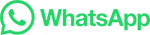
Jaw Crusher
Jaw Crusher. ₹ 65,000 Get Latest Price. Brand: Shambhavi IMPEX. This is a primary crusher and sometimes used as a secondary crusher too. It is used for size reduction of minerals, ores, chemicals, Ferro-alloys (except low …
اقرأ أكثر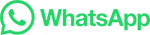
Below the surface: Setting up an underground primary jaw crusher
Jaw crushers are the most common solution in underground applications when the throughput is below 1000 tonnes per hour, depending somewhat on the scalping solutions. Above 1000 tph, primary gyratory crushers are an option. After the throughput reaches 2000 tph, jaw crushers are very rare, with the exception of a parallel plant layout.
اقرأ أكثر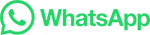
What Is Primary, Secondary, and Tertiary Crushing?
Primary crushing is the first stage of material reduction and can sometimes be the only stage needed to generate the desired product for a job. Depending on the …
اقرأ أكثر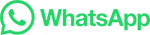