Advances in Sintering and Pellet Technology
Sintering and pelletization processes are largely influenced by the source of iron ore and the way in which the beneficiation flowsheet is adopted. The …
اقرأ أكثر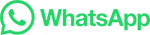
Iron Ore Agglomeration Technologies | IntechOpen
There are several agglomeration processes including: briquetting, extrusion, nodulization, pelletizing and sintering, although …
اقرأ أكثر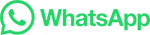
Iron Ore | ScienceDirect
Iron ore is regarded as the second most important commodity behind oil. As an essential input for the production of crude steel, iron ore feeds the world's largest trillion-dollar-a-year metal market and is the backbone of global infrastructure. To meet the growing demand for steel products, world iron ore production has increased ...
اقرأ أكثر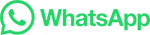
Iron ore pelletization
Iron ore pelletization 15 D. Zhu. 1, J. Pan, L. Lu. 2, R.J. Holmes. 3. 1. ... purities, the finer size distribution of concentrates limits their usage in iron ore sintering. Therefore ...
اقرأ أكثر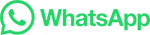
Iron ore pelletization
Direct reduction (DR) of iron ore with hydrogen is a potential route for near-zero CO 2 steelmaking, but vertical shaft DR reactors require that iron ore fines must first be pelletized. This study reports an investigation of the pelletization and subsequent sintering behaviour of titanomagnetite (TTM) ironsand, which is the main iron ore …
اقرأ أكثر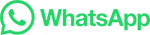
"Iron Ore Pelletization: Part II. Inorganic Binders" by S. K.
The addition of pellet binders often represents a compromise between the pellet grade and quality measures as strength, reducibility, and dustiness. Each inorganic compound present within the pellet plays a specific role in each aspect of creating a high-quality pellet. This review seeks to clarify the roles of both binders and coincidentally …
اقرأ أكثر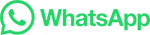
Pelletization and Sintering of New Zealand Titanomagnetite …
Direct reduction (DR) of iron ore with hydrogen is a promising alternative ironmaking process with near-zero CO2 emissions. This approach is applicable for the reduction of New Zealand (NZ) titanomagnetite (TTM) ironsand, which offers the potential for establishing a clean steelmaking industry in NZ. However, iron ore fines must first be …
اقرأ أكثر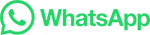
(PDF) Iron Ore Pelletizing Process: An Overview
PDF | On Jul 11, 2018, Sandra Lúcia de Moraes and others published Iron Ore Pelletizing Process: An Overview | Find, read and cite all the research you need on ResearchGate Chapter PDF Available...
اقرأ أكثر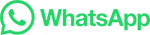
Utilization of Pellet Fines in the Iron Ore Sintering Process
Sintering Behavior of Pelletizing Feed in Composite Agglomeration Process (CAP) of Iron Ore Fines. Chapter © 2016. Recycling and Reuse of Iron Ore Pellet Fines. …
اقرأ أكثر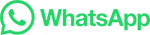
Preparation of Iron Ore Micro-pellets and Their Effect on …
The iron ore fines with less than 10 mm size are usually fed to the sintering process, and only limited fraction (less than 20%) of − 150 micron size of iron ore fines are allowed in the sintering process. The finer sized iron ore may choke the sinter bed and hinder the uniform air suction through the bed.
اقرأ أكثر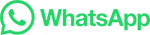
Iron Ore Pelletization: Part II. Inorganic Binders
Iron Ore Pelletization: Part II. Inorganic Binders. S. K. Kawatra Department of Chemical Engineering, Michigan Technological University, Houghton ... such as differential scanning calorimetry to predict sintering heat requirements, roll-press mixing to improve the dispersion of clay binders, and cold bonding techniques as an alternative to ...
اقرأ أكثر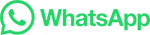
A review of binders in iron ore pelletization
The most common agglomeration technique is pelletization, which requires the use of binders to hold the iron oxide grains together so that the agglomerates can be sintered into high-strength pellets. Although bentonite clay is the most commonly used binder, there are many other possibilities that could be competitive in a number of …
اقرأ أكثر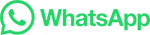
Iron Ore Pelletization Technology and its Environmental …
Agglomeration technologies such as Pelletization / Sintering have to be added to Steel Plant so that concentrates can be used as feed material. This paper will give an insight about the potential of pelletization technology of iron ore. ... Iron ore Pelletization has been identified as an alternative substitute for steel making process. …
اقرأ أكثر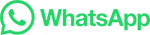
Iron ore pelletization
A brief introduction to recent developments in iron ore pelletizing is provided in this chapter, including the world output of fired pellets, pellet production processes, preparation of pellet feed, inorganic and organic binders, and new additives. Throughout the chapter, the authors have used a difficult pellet feed, that is, a Brazilian ...
اقرأ أكثر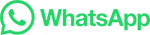
Prediction of Sinter Properties Using a Hyper-Parameter …
The sintering process produces iron ore agglomeration of size 10–40 mm with better reducibility values than lumps. Utilization of a higher proportion of quality agglomerates in the burden increases the productivity of the blast furnace. The sintering process increases the productivity and reduces the requirement of fuel, flux, and …
اقرأ أكثر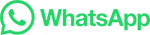
Iron ore pelletization
Iron ore lump, sinter, and pellets comprise the main burden of modern blast furnaces. However, sinter and pellets are now the dominant blast furnace burden, …
اقرأ أكثر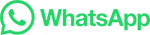
Introduction to Iron ore Pellets and Pelletizing processes
Raw material preparation – During the process for pelletization iron ore concentrate from iron ore beneficiation plant is dried and heated to around 120 deg C. The dried material is fed to the ball mill for grinding. Concentrate/ground iron ore of typical size 80 % less than 45 microns (0.045 mm) with a moisture content of around 9 % is ...
اقرأ أكثر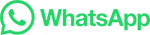
Iron Ore: Mineralogy, Processing and Environmental …
Iron Ore: Mineralogy, Processing and Environmental Sustainability, Second Edition covers all aspects surrounding the second most important commodity behind oil. ... 15 Iron ore sintering. 489: 16 Iron ore pelletization. 539: 17 Blast furnace ironmaking and its ferrous burden quality requirements. 579: 18 Alternative ironmaking processes and ...
اقرأ أكثر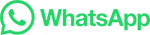
Iron Ore Sintering: Process
Sintering is a thermal agglomeration process that is applied to a mixture of iron ore fines, recycled ironmaking products, fluxes, slag-forming agents, and solid …
اقرأ أكثر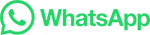
Pelletization and sintering of New Zealand
Direct reduction (DR) of iron ore with hydrogen is a potential route for near-zero CO 2 steelmaking, but vertical shaft DR reactors require that iron ore fines must first be pelletized. This study reports an investigation of the pelletization and subsequent sintering behaviour of titanomagnetite (TTM) ironsand, which is the main iron ore …
اقرأ أكثر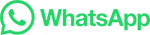
CO 2 -Free Flux for Sustainable Iron Ore Pelletizing
The iron and steel manufacturing sector directly accounts for 7–9% of global CO 2 emissions. Raw material preparation, such as iron ore sintering, pelletizing, and cock making, is the major CO 2 emitter. As climate change becomes a bigger concern, steel manufacturers need to lower CO 2 emissions without hindering efficiency or increasing …
اقرأ أكثر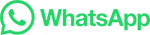
Iron Ore Pelletizing Process: An Overview
2014 •. Ottavio Carmignano. Pelletizing iron ore fines is an agglomeration process that through a thermal treatment converts the ultra-fines fraction thereof into small balls ranging in size from 8mm (0.31 in.) to 18mm (0.71 in.), with adequate characteristics for feeding steel reduction works.
اقرأ أكثر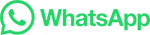
Iron ore pelletization
The pelletization process is the primary consumer of binders in the iron ore industry. The selection of an appropriate binder type and dosage is of critical importance in producing good quality pellets at a reasonable price. Binders accomplish two very important functions in iron ore pelletization: •.
اقرأ أكثر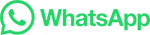
Hazard Identification, Risk Assessment, and Control
India has the fourth largest iron ore reserves in the world after Russia, Brazil, ... Agglomeration technologies such as pelletization/ sintering have to be added to steel plant so that concentrates
اقرأ أكثر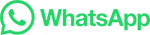
Iron Ore
Purchase Iron Ore - 2nd Edition. Print Book & E-Book. ISBN 9780128202265, 9780128202272. Skip to main content. ... 15.4 Recent developments in iron ore sintering. 15.5 Conclusions. Acknowledgments. References. Chapter 16 Iron ore pelletization. Abstract. 16.1 Introduction. 16.2 Specification requirements of pellet feed. 16.3 Green ball ...
اقرأ أكثر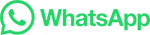
Iron ore pelletization | Semantic Scholar
Semantic Scholar extracted view of "Iron ore pelletization" by De‐qing Zhu et al. ... Pelletization and Sintering of New Zealand Titanomagnetite Ironsand. S. Mendoza B. Yin A. Zhang C. Bumby. Materials Science, Engineering. Advanced Powder Technology. 2022;
اقرأ أكثر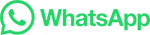
SINTERING AND PELLETISATION OF INDIAN IRON ORES
ROM iron ore with Fe less than 58 – 60% discarded as waste. After beneficiation iron ore availability can improve by about 50%. Steel community and the country demand technological solutions for utilising low grade ores. The technology task that would be imperative: 1. Utilisation of low grade iron ores after beneficiation. 2.
اقرأ أكثر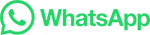
Pelletization
The pelletization process is the primary consumer of binders in the iron ore industry. The selection of an appropriate binder type and dosage is of critical importance in producing good quality pellets at a reasonable price. Binders accomplish two very important functions in iron ore pelletization: •.
اقرأ أكثر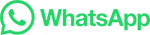
FLOFORM ™ Iron Ore Pelletization
FLOFORMTM, an alternative. elements such as silica and alumina. FLOFORM is typically dosed at 0.01-0.05% prior to balling, i.e. about 1/20th of Bentonite. Depending on the quality of iron ore, a dual binder system comprising both FLOFORM (0.02 to 0.03%) and bentonite ( 0.2 to 0.33%) in the addition range could also give excellent results thus ...
اقرأ أكثر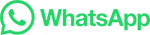
Study on applicability of biomass in iron ore sintering …
To Substitute coke breeze by charcoal in iron ore sintering process: Results are found negative on even replacement of coke breeze with charcoal and also increasing the fuel input from 3.62% to 4.17%. Lu et al. (2013) [5] To perform quantitative analysis of Polychlorinated napthalenes (PCN) emissions generated from iron ore …
اقرأ أكثر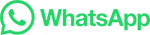