مرحبًا بكم في قاعدة إنتاج معدات التعدين. نحن ننتج بشكل أساسي معدات التكسير والطحن والتعدين ذات الصلة. إذا كان لديك أي احتياجات ، يمكنك الاتصال بخدمة العملاء عبر الإنترنت أو ترك رسالة من خلال النموذج أدناه. سوف نخدمك بكل إخلاص!.
Making Iron Directly From Concentrate by Gaseous …
A sketch of the Flash Ironmaking process is shown in Fig. 1. A gaseous fuel is partially oxidized with industrial oxygen to generate a reducing gas at 1600–1900 K. Iron ore …
اقرأ أكثر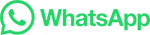
Development of Ironmaking Technology by the Direct …
A sketch of the Flash Ironmaking process is shown in Fig. 1. A gaseous fuel is partially oxidized with industrial oxygen to generate a reducing gas at 1600–1900 K. Iron ore concentrate is fed from the top, and the reduced iron product can be collected as a solid powder or as a molten bath for direct steelmaking.
اقرأ أكثر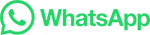
From Ore to Iron with Smelting and Direct Iron …
Smelting Reduction. Figure 2: The smelt reduction vessel (SRV) is the core technology component of the Hismelt process. Source: RioTinto While years of ironmaking technology innovations have …
اقرأ أكثر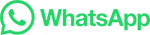
From Ore to Iron with Smelting and Direct Iron …
Smelting Reduction. Figure 2: The smelt reduction vessel (SRV) is the core technology component of the Hismelt process. Source: …
اقرأ أكثر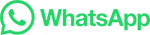
Compagnie minière IOC
The crude ore is loaded into trucks, which dump the material into the loading pockets or into the in-pit crusher located in the Luce pit.","3825":"IOCu2019s operations are integrated across our mine and processing plant in Labrador City, Newfoundland and Labrador; our port, stockpile and vessel loading facility in Sept-Iles, Quebec; and the ...
اقرأ أكثر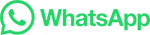
Drying and Roasting Characteristics of Iron Ore Pellets with …
Drying and roasting behavior of iron ore pellets with microwave and conventional heating have been comparably investigated. The results showed that the dehydration time of green pellets can be shortened by approximately two-thirds with microwave heating. Meanwhile, the average compressive strength of pellets with organic …
اقرأ أكثر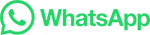
Our Operations
We are Iron Ore. Tacora Resources is an innovative iron ore mining and mineral processing company focused on the acquisition, development, and operation of iron ore reserves and assets which allow for the sale of high-grade iron ore products throughout the world. At Tacora, we drive progress – the right way; sustainably producing the most ...
اقرأ أكثر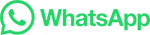
Iron Ore Pelletizing Essential in Meeting Future Steel Needs
As the world leader in tumble growth agglomeration, FEECO provides a variety of services and equipment for iron ore pelletizer plants. As the needs of the steel industry change, one production component looks to be increasingly important in meeting the needs of the modern steel industry: iron ore pelletizing. Iron ore pelletizing, or balling, is the process …
اقرأ أكثر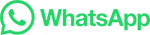
Magnetation to close iron ore concentrate facility in …
Iron ore concentrate and pellet producer Magnetation has announced plans to close its Plant 1 iron ore concentrate facility in Keewatin, Minnesota, US, citing low global iron ore prices. The plant, which will be indefinitely idled by the end of March, would be placed on a care and maintenance programme.
اقرأ أكثر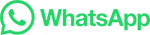
Iron Ore Operations | Fortescue
Iron Bridge. Iron Bridge signifies Fortescue's entry into the high grade segment of the iron ore market, providing an enhanced product range while also increasing annual production and shipping capacity. Located 145km south of Port Hedland, Iron Bridge is Fortescue's first magnetite operation and incorporates the North Star and Glacier ...
اقرأ أكثر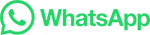
Introduction to Iron ore Pellets and Pelletizing …
There are four stages involved in the production of iron ore pellets. These stages consist of (i) raw material preparation, (ii) formation of green balls or pellets, (iii) induration of the pellets, and (iv) cooling, …
اقرأ أكثر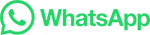
Optimal ceramic filtration operating conditions for an iron-ore concentrate
Ceramic filtration is used for the final dewatering stage of the concentrate product at a Brazilian iron ore operation. This research was aimed at improving the understanding of the suitability of ceramic filtration technology for full-scale operation, to identify factors that positively and negatively impact filter efficiency, and to evaluate …
اقرأ أكثر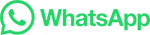
Iron ore – tailored solutions
Concentrate dewatering: higher throughput, lower costs. Dewatering iron ore concentrates is a crucial step in enhancing their handling and transportation by removing excess water. …
اقرأ أكثر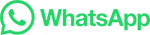
Highly efficient and green separation of iron from complex …
According to Table. 1, the total iron content of the raw ore is 37.72%, and the ferrous iron content is 6.07%.The REO content is 5.33%, the CaO content is 11.2%, and the F content is 6.07%. The major impurity is SiO 2 with a content of 7.4%, while MgO and Al 2 O 3 contents are 1.4% and 1%, respectively. Penalty elements such as P and S have …
اقرأ أكثر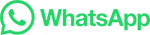
Iron ore | BHP
Iron ores are rocks and minerals from which metallic iron can be extracted. There are four main types of iron ore deposit: massive hematite, which is the most commonly mined, magnetite, titanomagnetite, and pisolitic ironstone. These ores vary in colour from dark grey, through to deep purple, rusty red and bright yellow.
اقرأ أكثر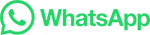
Pressing iron ore concentrate in a pilot-scale HPGR. Part 1
The successful application of HPGR technology prior to iron ore pellet formation has been associated to: • reduction of energy consumption through the introduction of microcracks, which increase the production rate and reduce the particle size of the pellet feed final product (Ehrenraut and Rao, 2001, Van der Meer, 2015);generation …
اقرأ أكثر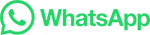
Nordic Iron Ore will produce a highgrade iron ore concentrate …
Blötberget is the first deposit that Nordic Iron Ore will process and is home to ore for at least 10 to 12 years of mining. ... Nordic Iron Ore will produce an iron ore concentrate with an average iron content of close to 69 per cent. ... For additional information on our operations and to see what the facility in Blötberget will look like ...
اقرأ أكثر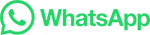
Development of Ironmaking Technology by the Direct …
The reduction kinetics of iron ore concentrate particles were measured in the temperature range expected for the proposed process using a thermogravimetric analysis (TGA) unit . The rate equations for the hydrogen reduction of iron concentrate, formulated from the experimental data, are given for different temperature ranges, as …
اقرأ أكثر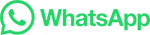
Iron Ore Flotation Process: The Journey from Ore to Concentrate
Iron ore flotation process. 1. Grinding: Crushing and grinding the raw ore to a certain particle size is a necessary preparation before iron ore flotation.The purpose of grinding is to fully ...
اقرأ أكثر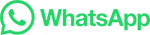
Pressing iron ore concentrate in a pilot-scale HPGR. Part 1
The paper analyzes tests with an iron ore concentrate sample carried out over a range of pressures, roll velocities, feed size distributions and moisture contents in a pilot-scale facility. It is ...
اقرأ أكثر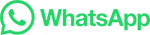
Making Iron Directly From Concentrate by Gaseous Reduction
The overall process of developing a novel Flash Ironmaking Technology (FIT) have been described in this article. Rate equations for the reduction of iron ore concentrate by hydrogen, carbon monoxide, and a mixture of the two formulated in this work established the fundamental … See more
اقرأ أكثر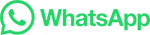
Idled Iron Range iron unit plant to re-start
The new company will process former natural iron ore mining waste material into high-grade, low-impurity iron ore concentrate at the site. Concentrate produced at the plant will be a higher grade than what was formerly produced at the facility and supply the growing electric arc furnace steelmaking segment, Lehtinen said. "We will …
اقرأ أكثر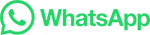
Optimal ceramic filtration operating conditions for an iron-ore concentrate
The concentrate is then pumped 529 km to a port facility where it undergoes additional thickening before reporting to Outotec Larox CC-144 ceramic filter units for final dewatering of product. ... Thus ceramic filtration is considered a suitable method for the metallurgical process of dewatering of iron-ore concentrate. Acknowledgements. The ...
اقرأ أكثر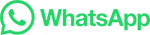
The six main steps of iron ore processing
Iron ore concentrate is an output product from processed iron ores that have been milled (crush, grind, magnetic separation, flotation) to separate deleterious …
اقرأ أكثر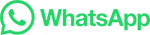
Innovative utilization of refractory iron ore via suspension
Analyses of the iron ore before and after SMR followed by LIMS. The performance of the SMR reactor was evaluated based on the yield (γ), TFe (α for the raw iron ore, β for the magnetic concentrate and θ for the magnetic tailing), and iron recovery (ε) of products from the LIMS process, as follows [35]: (8) γ = α − θ β − θ × 100 % ...
اقرأ أكثر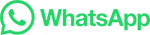
Iron Concentrate Particles
Iron ore concentrate is an output product from processed iron ores that have been milled (crush, grind, magnetic separation, flotation) to separate deleterious elements and produce a high-quality product. Sintering and pelletizing are economic and widely used agglomeration processes to prepare iron ore fines/iron concentrate for …
اقرأ أكثر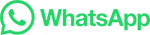
Making Iron Directly From Concentrate by Gaseous …
The second process is the direct reduction of iron ore in a shaft furnace operated with hydrogen only. The third process is the melting of the carbon-free direct …
اقرأ أكثر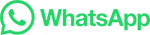
Mechanism of magnetite iron ore concentrate morphology …
1. Introduction. Iron ore pellets are one of the significant sources of iron for iron and steel making due to their superior metallurgical performance, low energy consumption, and less emission of environmentally harmful dust and gases during the production process [1], [2], [3].The two primary raw materials for pellet production are …
اقرأ أكثر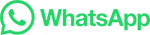
HYFOR: Hydrogen-Based Fine-Ore Reduction
Hydrogen-based Fine-Ore Reduction (or HYFOR for short) is the world's first direct-reduction process for iron-ore concentrates from ore beneficiation that does not require any preprocessing of the material like sintering or pelletizing. Building on comprehensive experience from Primetals Technologies' Finmet and Finex processes, …
اقرأ أكثر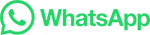
Pressing iron ore concentrate in a pilot-scale HPGR. Part 2: …
An iron ore concentrate from the Iron Quadrangle area (Minas Gerais, Brazil) has been selected for the study. It is essentially composed of hematite with minor amounts of quartz as contaminant. Pilot-plant experiments have been conducted at a pilot-plant HPGR, which consists of a studded roll with 0.32 m in width and 1 m in diameter.
اقرأ أكثر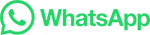