A Comprehensive Guide on Optimizing Cement Plant Design
Designing an efficient and reliable cement plant is a crucial task that demands a strategic approach, technical expertise, and a focus on sustainability. …
اقرأ أكثر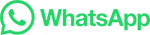
EVERYTHING YOU NEED TO KNOW ABOUT ESTABLISHING CEMENT GRINDING PLANT
The cement production would be dictated by local and foreign demands, and, by the targeted 1.0 MTPA. Grinding operations would therefore necessarily be carried out 24 hours a day through three eight hour shifts for 365 days a year. The packing plant is planned to operate 24 hours a day through three 8-hour shifts, 365 days a year.
اقرأ أكثر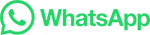
Drum Mix Plants | The Gencor Ultraplant | Gencor …
Gencor's Ultraplant® concept is the most fuel efficient, environmentally clean and lowest maintenance design available to the hot mix industry. A totally integrated drum concept that allows high production continuous mix with high-volume, high moisture recycle and the optional flexibility of feeding a batch tower, all in a unitized drum design.
اقرأ أكثر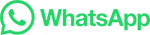
Design of solar cement plant for supplying thermal energy in cement …
Thermal energy needed for operating the conventional cement plant in solar mode mainly depends on the heat losses in the solar reactor given in Eq. (1). Solar reactor design for a solar cement plant is as follows ( Meier et al., 2006 ): (1) Heat and mass balance for the solar reactor is shown in Fig. 3.
اقرأ أكثر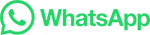
Optimization of the Clinker Production Phase in a Cement Plant …
The study and design phases of the project for the development of the system began in September 2014 and ended in November 2014. Since February 2015, the controller has been installed on the considered Italian cement industry for the optimization of the clinker production phase, replacing plant operators' manual conduction.
اقرأ أكثر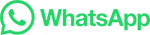
Welcome to Dangote Cement Plc – We are an Integrated Cement …
Our vision is for West and Central Africa to be cement and clinker self-sufficient, with Nigeria the main export hub. Dangote Cement is focusing on an 'export to import' strategy in West and Central Africa. Nigeria has a relative abundance of quality limestone especially in key southern regions near to demand centers and export facilities.
اقرأ أكثر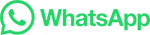
U.S. Portland Cement Industry: Plant Information …
The 2013 plant survey reflects the industry emerging from the economic downturn as total capacity is 3.7 mmt less than the 2010 plant summary and 19 kilns totaling 5.7 mmt of capacity remain idle. From the 2010 survey, daily clinker capacity decreased 11,121 metric tons to 307,077. Typical annual down days for scheduled kiln maintenance, repair ...
اقرأ أكثر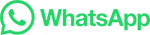
Cement Manufacturing Process
Part One: Raw Material Preparation. General. The production of cement is started from quarrying the raw material. The main raw materials are limestone, basalt, sand stone, pumice, gypsum. Site Exploration of suitable deposits, for the raw material has three main aims:-. Verifying the quality of the raw materials.
اقرأ أكثر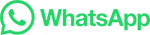
Concrete Batch Plants for Sale: Ready Mix, Precast & Central Mix
F Direct offers custom concrete batching plants for sale: ready mix, precast, & central mix. Call us for new or used concrete batching plants. ... Adding a high-powered automatic concrete mixer washout system dramatically reduces the man hours used for cleaning and lowers your maintenance costs. With the time saved on cleaning, you can ...
اقرأ أكثر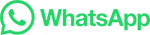
CEMEX and RTI awarded $3.7 million cooperative agreement …
The front-end engineering design (FEED) study, which is to be conducted at CEMEX's Balcones Cement Plant in New Braunfels, ... The company recently updated its 2030 goals which include reducing CO 2 emissions by 47% per ton of cementitious material and delivering concrete with 35% less carbon content when compared to 1990 baseline …
اقرأ أكثر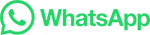
Maps of global cement plants worldwide. (a) CO2 emissions …
Global cement demand and production has increased compared to that in 1995, when the total volume of global cement production was 1.39 billion tons, and it is estimated to reach 4.1 billion tons ...
اقرأ أكثر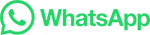
Brooksville
Here are just a few of the ways CEMEX cares: Safety is a priority at the CEMEX Brooksville South Cement Plant with multiple upgrades at the facility in the past year. The plant has also been recognized repeatedly for its safety initiatives and efforts. Brooksville South earned the 2017 PCA Chairman Award and the 2018 PCA Safety. Innovation Award.
اقرأ أكثر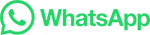
Nomograms for Design and Operation of Cement …
OPC, ratio of cement to clinker is 1.05. Every ton of cement produced releases 0.8 ton of CO 2. By increasing the cement/clinker ratio that is by making 'blended cements' this emission can be reduced to 0.53 to 0.30 ... 5 Developing Layouts for a Green Cement Plant 6 Layout for Despatch of Cements Bagged and in Bulk Machinery C. by S. P ...
اقرأ أكثر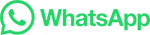
'Build, Build, Build'-ing in the Philippines
Top 5 players in 2020. Lafarlcim: The largest cement producer in the Philippines at the start of 2020 is the Swiss-French giant Lafarlcim, which operates 9.9Mt/yr of capacity across four integrated plants (9.1Mt/yr) and one grinding plant (0.8Mt/yr). Lafarlcim added 0.7Mt/yr of capacity to its Davao plant in 2019.
اقرأ أكثر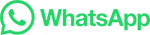
Concrete Batching Plants | SCHWING Stetter India
Concrete Batching Plants are basically divided into three major types based on quantity of concrete to be produced per hour, namely Less than 30cu.m/hour, 30 to 60 cu.m/hour, More than 60 cu.m/hour. We at SCHWING Stetter India provide all types of batching plants suitable for RMC, Infrastructure, Roads, Rural and Metro applications. Every ...
اقرأ أكثر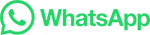
Cement Manufacturing Plant
Gidday Mark, Model Railroader, July 1994, "Add a cement plant to your layout" by Ken Nelson, and April 1995, "Kit bashing a cement company in HO scale" by Walt Niehoff. Walthers HO scale "Valley Cement Plant" kit still appears to be available if you wished to go down that track.
اقرأ أكثر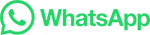
U.S. cement industry
Production capacity of cement in the United States from 2020 to 2022, by plant type (in million metric tons per year) Premium Statistic U.S. cement shipments to final customers 2010-2023
اقرأ أكثر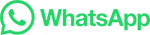
To decarbonize cement, the industry needs a full… | Canary …
The U.S. cement industry has already cut its emissions-intensity per metric ton of cement by roughly 10 percent since 1995, largely by replacing coal and coke with fossil ... Another option available right now is to retool cement plants to be more efficient, which Holcim is also doing to clean up the 1, 500-degree-Celsius kilns it uses to make ...
اقرأ أكثر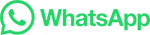
WHAT TO CONSIDER IN A CONCRETE BATCH PLANT LAYOUT
Local concrete markets will determine the amount and number of on-site storage silos or bunkers. Delivery's might be limited to non-communute hours reducing the congestion on local streets. Concrete Reclaimers and washout area's are trending to be located closer to the batch plant to recycle water into fresh concrete. Some States are ...
اقرأ أكثر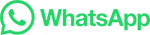
EVERYTHING YOU NEED TO KNOW ABOUT ESTABLISHING …
PROJECT DESCRIPTION. The present chapter describes the technical aspects of the clinker grinding plant, namely its capacity, imported raw materials, size and type of …
اقرأ أكثر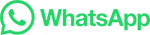
Cementing the future
In the U.S., the Charlevoix, Michigan plant can produce 1.4 million tons of cement each year. The newly upgraded plant will not only increase capacity to 2 million tons of cement, but also meets new standards for eco-friendly operation, with new efficiencies and carbon mitigation strategies to reduce greenhouse gas emissions.
اقرأ أكثر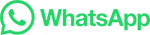
Every KPI you should use in Cement Industry
Measured for: Crusher, Raw mill, Kiln, Cement mill, Packing plant (separate for each line) Target: Crusher: Raw Mill: Kiln: Cement Mill: Packing plant: Purpose: Measure of actual output performance in relation to the …
اقرأ أكثر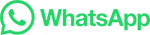
asphalt plant 160 tons / hour complete project
asphalt plant 160 tons / hour complete project | 3D CAD Model Library | GrabCAD. Join 9,360,000 engineers with over 4,850,000 free CAD files Join the Community. The CAD files and renderings posted to this website are created, uploaded and managed by third-party community members.
اقرأ أكثر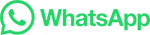
(PDF) Cement plant operation handbook
Eliana Motta. The cement production is one of the most energy consuming processes, typically accounting for 50 to 60% of the production costs. However, there are several …
اقرأ أكثر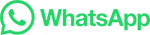
Answered: A cement plant has a design capacity of
A cement grinding mill "A" with a capacity of 50 tons per hour employs P12,000 per tonforged steel grinding balls with a wear rate of 100 grams per ton of cement processed.Another cement mill of the same capacity, "B," utilizes P50,000 per ton high chromesteel grinding balls with a wear rate of 20 grams per ton of cement …
اقرأ أكثر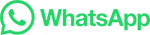
ConCrete BatCh Plants
Modular Design Weigh Belt System, Low Profile Batch System, Modular Design Volumetric System or Stack-Up Gravity Feed System, whatever your preference, Besser will design a batch plant to meet your needs. Besser has built custom-made aggregate bins with capacities up to 1000 tons (900 tonnes) that incorporate ten compartments and silos of …
اقرأ أكثر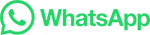
BASIC CEMENT PLANT LAYOUT – Process Cement …
01 Limestone Stock Pile. The raw material is stored at either the quarry or at the plant. Typically, circular or longitudinal stockpiles are …
اقرأ أكثر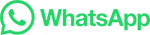
How to Start a Cement Factory | Design & Construction of Cement Plants
1. Clarify Your Production Scale and Cement Type. The first thing to do when you are planning to start a cement factory is to determine which type of cement you are going to produce and how many tons you are going to produce per day. The most widely used cement for concrete works is ordinary portland cement (OPC), apart from that, there is …
اقرأ أكثر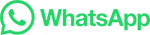
Cement Silo Design & Manufacturing
Nowadays, the cement used in the concrete batching plants is mostly bulk, and the air pressure of bulk cement trucks conveying cement is 0.2~3.0MPa, which is enough for the bin with a 3m diameter. For cement silo safe, a gravity safety valve is installed on the top of the silo, and the opening pressure of the safety valve is set at …
اقرأ أكثر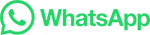